It’s no surprise that the manufacturing sector has a growing problem with its aging workforce. Partly due to the outdated perspective where one might go to work in an old factory, making sure screw A goes into hole B all day, the career path isn’t a top choice for today’s young adults just graduating from college. In reality, though, modern manufacturing entails a considerable amount of interaction with advanced technologies and interesting applications that require a diverse and educated skillset.
As proof of how dynamic and challenging manufacturing careers can be, consider the fact that in spite of a manufacturing labor force in the U.S. that is half of what it was in 1970, innovative applications of technology in the manufacturing arena have led to unprecedented levels of output, productivity, and global competitiveness.
As the average manufacturing operations management worker's hair gets greyer, companies are faced with two sets of challenges. First, there’s the battle of attracting new, young employees and then grooming the talent to become the next generation of leaders. And second, manufacturers have to face the reality that the details and idiosyncrasies that make things run smoothly on the shop floor are at a higher risk of being retired rather than transferred to the next generation. According to U.S. Department of Labor Bureau statistics, the average U.S. manufacturing worker's age is now 50 years old and half of the U.S. manufacturing workforce is ten to 15 years away from retirement.
This post will focus on the latter challenge and the efforts that organizations are taking to preserve and leverage tribal knowledge. In many cases, companies are utilizing emerging technologies such as manufacturing operations management software to optimize its value and mitigate associated risks.
Approaches to Preserving Tribal Knowledge
Manufacturing workers aren’t simply expected to produce products over and over again, they’re also expected to apply their knowledge to continuously rise to new levels of efficiency and productivity by measuring and improving processes. As knowledge slowly fades away due to retiring expertise and the lack of knowledge transfer to younger workers, the real danger becomes that organizations may lose the ability to innovate and drive manufacturing competitiveness forward. Market leaders are taking several measures to make sure functional depth gets passed along and to enable this type of innovative environment.
- Knowledge and Document Management Initiatives - Many companies are making use of solutions such as knowledge management systems, which essentially compile all process and procedural documentation, and training materials in one place. Rather than allowing this critical information to be scattered across different manuals and computers at distributed workcenters, organizations are aggregating it and creating global best practices.
- Standardizing Processes - Just because one plant or division or region is doing something one way, that doesn’t mean that it’s the best way. Manufacturers are evaluating the effectiveness of processes across the enterprise, identifying areas for global synergies, and standardizing when applicable. This not only allows the 'best of the best practices' to be shared across an enterprise, but also simplifies knowledge transfer and enables more universal talent sharing and moving across an organization.
- Understanding Exception Processes - Manufacturers focus considerable efforts on standardizing processes with the assumption that things will run smoothly. However, there are some things you cannot plan for. Identifying and recording exceptions, along with expanding or modifying procedures for when these situations reoccur, can help to reduce risk and improve the ability to respond to adverse events during production.
- Escalation Policies - Developed out of experience, many plants have tacit processes for escalating issues. For instance, if a particular manufacturing nonconformance transpires, a line worker may notify a manager. Though, when that worker retires, handling future instances of that nonconformance may be left to the discretion of a new employee without formal escalation policies in place. Escalation policies and procedures need to be part of the important knowledge that is documented and transferred across an organization.
- Automating Work Processes - To reduce risk and variability across the enterprise, companies are increasingly taking efforts to systematize manual processes. Manufacturing software is driving the ability to capture knowledge and automate work processes where possible, allowing the broader enterprise to benefit from best practices.
The Role of Manufacturing Software
In general, software has revolutionized how business is conducted. It’s opened up the capability to capture and analyze large amounts of manufacturing operations and performance data, and for organizations to communicate and collaborate on issues, which was traditionally one of the biggest roadblocks for large and distributed companies. When it comes to the issue preserving and leveraging tribal knowledge in the manufacturing industry, manufacturing software has been a game changer. Companies are using it in various ways to reduce risk associated with the aging workforce.
- Industrial Automation and Safety Systems - At the level of the system architecture that is closest to physical machines and processing equipment, industrial automation and safety systems are the first line of defense. If, for instance, a vessel is getting too much pressure or a temperature gets too high that it becomes dangerous, in some cases companies are still relying on people to shut them down. By automating these most critical processes, it mitigates risk and improves safety.
- Workflow and Electronic Work Instructions - Manufacturers can provide in-context manufacturing step instructions and training, as well as validating that particular work instructions are followed during manufacturing processes by mapping process workflows into software. Eliminating reliance on homegrown and local processes, these solutions can require approvals for particular actions and also trigger the need for and routing of escalation when issues surface.
- Manufacturing Execution System Software - On the shop floor, MES software can ensure that manual and semi-automatic manufacturing plans, recipes, and procedures are followed and enforced. Large companies can build and make changes to MES driven processes from a central engineering/IT location and distribute them to shop floors globally.
- Remote Management/Mobile and Collaboration Software - Reducing the need for on-site experts, organizations can use remote management, mobile, and collaboration solutions to securely make changes and adjustments to processes from anywhere in the world. Although this doesn’t necessarily capture knowledge, it allows companies to harness specialized talent when needed.
- Operator Training Simulator Software - Simulating operational practices with OTS software helps to train employees on new processes and operations, but it’s also critical for honing the ability to respond to new or unusual situations. By realistically simulating the manufacturing environment and all of the critical operational interactions, employees can use OTS software to become proficient in this 'safe sandbox' environment, leaving them better prepared for real-world situations.
- Maintenance Management Software - Today's maintenance management software solutions can capture, organize and enforce maintenance procedures. These solutions can be extended even further beyond maintenance planning and procedures to include the proper lists of tools and materials, and can even include instructional videos to assist maintenance personnel in the proper diagnosis and repair of manufacturing assets. Maintenance information can be collected and delivered, in context with the work being performed by maintenance personnel using mobile devices - right where the action is taking place.
Balancing People, Processes, and Technology
With many companies bringing back, or at least reconsidering the reshoring of manufacturing activities, we can see positive signs that manufacturing careers will regain popularity in the younger generations. Regardless, manufacturers will continue to find new ways to optimize key resources across people, processes, and technology to enable environments for continuous improvement. In the future, we will be covering each of these areas more in depth. But in the meantime, please feel free to share your own thoughts and opinions on the topic in the comments section below.
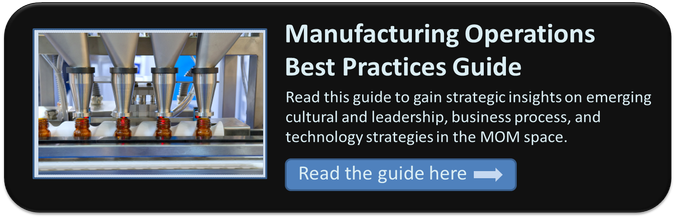
You might also be interested in:
What is Manufacturing Operations Management?
Manufacturing Operations Management: Exit Clipboard, Enter iPad
Creating a Business Process Platform