For a number of reasons, every organization has a unique approach to IT. When it comes to manufacturing in particular, the approach is often dictated by the type of products and processes involved. For some companies aiming to improve manufacturing operations capabilities, it may make sense to build on the enterprise backbone, which is typically ERP. For others, however, it makes sense to build upon existing manufacturing operations management (MOM) or industrial automation investments.
Since there are various types of IT foundations found in today's complex organizations, it's important to understand the various approaches to building out MOM capabilities. Based on the three IT models described above, we've identified three different approaches: a top-down or ERP-centric approach, a center-out or MOM-centric approach, or a bottom-up or industrial automation-centric approach. In this post, we’ll detail the main pros and cons of each.
Understanding the Different Manufacturing Software Strategies
While there is usually a need to simplify and consolidate processes where possible, it’s also important to integrate key processes and ensure that the systems that support manufacturing operations are actually helping to improve the business and not just feeding other systems and people in the organization with information that may not be necessary. This takes a tactical approach, and depending on your existing investments, the approach may vary.
Pros: A top-down software approach takes the existing ERP structure and uses it as a backbone on which to build. One of the largest advantages of this approach is the master data consistency that it allows the business, as well as the opportunity to have strong integration/enforcement between business and manufacturing processes. Additionally, an ERP-centric manufacturing IT structure allows for a combination of business and manufacturing intelligence, requires fewer IT suppliers and points of enterprise application integration that require management. That said, you will still need to feed real-time information by integrating to automation layer for many industry use cases.
Cons: One of the main disadvantages of an ERP-centric approach is its lack of agility. The inherent rigidity of an ERP system makes any changes in manufacturing processes or improvements more difficult to implement. Typically, these are processes that need to be modified at a much faster rate than business processes. Additionally, detailed manufacturing functionality is not always as rich as with a manufacturing specific (center-out) strategy, and as a result, performance and availability issues can be factors.
Vendors such as SAP, Plex Systems, Oracle, and Epicor fall under this category; however, there are a wide variety that serve this space.
Center-Out/MOM Software-Centric Manufacturing Strategy
Pros: A center-out, or MOM-based IT approach is built upon the manufacturing operations management (MOM) software systems that support plant operations. One of the main benefits of this approach is the rich manufacturing operations functionality it offers. As can be seen in the infographic below, it integrates directly with the enterprise and automation level software above and below. This approach supports the needs of the plant operations and opens integration with different ERP, PLM, and industrial automation systems that provide detailed manufacturing intelligence capabilities, typical support of enterprise application integration standards like ISA-95, and industrial automation application integration standards like OPC/OPC UA that delineate and simplify integration with other systems. Unlike an ERP-based architecture, a center-out approach enables a much greater level of agility for modifying manufacturing systems and processes.
Cons: One of the disadvantages to the MOM-based model is that it sometimes won’t scale enterprise wide and may require multiple instances to manage across plants. It also may not be an ideal choice if you have multiple databases to manage across its application set. A center-out approach requires management of master data separate from bill of materials/ERP master data and manually linking business workflows with manufacturing workflows.
Vendors such as Apriso, Camstar, Lighthouse Systems, Parsec Automation, Aegis Software, and iBASEt fall under this category; however, there are many more that play in this space.
Bottom-Up/Industrial Automation System-Centric Manufacturing Strategy
Pros: When a manufacturing IT architecture is built around an automation system, it can readily match the plant, area, unit, and line structure defined in the automation system. Data collection is performed at a detailed level of operations, including what is occurring at the equipment level. However, this real-time information still needs to be modeled and correlated into production information. Like center-out, this approach also typically supports standards like ISA-95 and OPC/OPC UA.
Cons: Unfortunately, there are typically many different automation systems in place across a manufacturing enterprise, so a bottom-up approach doesn’t provide a common foundation for standardizing applications. Automation systems are also typically configured from an automation process and equipment point of view as opposed to a production/product manufacturing point of view, so the software is not sufficient to provide full/rich MOM functionality.
Vendors such as ABB, AspenTech, Emerson, Invensys Operations Management, GE IP, Honeywell, and Siemens, fall under this category, in addition to a number of others that serve this space.
Which Direction to Take?
So which approach is most popular and effective? These days, companies are mostly taking either the center-out or top-down approach, but different trends emerge based on company size and specific vertical industry needs, and for some organizations, bottom-up may make perfect sense.
The LNS Research Manufacturing Operations Management Survey dives deep into this and other important information in the MOM space. Click below to take find out what other important trends are surfacing with the intersection of technological advancements and market demands.
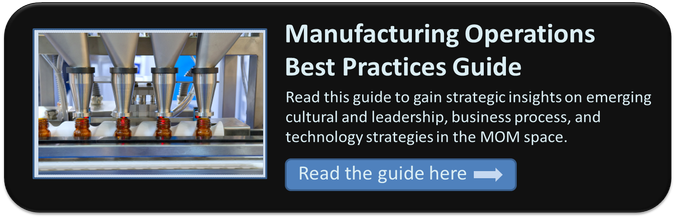