The third annual National Manufacturing Day is slated for this Friday, October 3, and more than 1,500 separate events are scheduled around the country to celebrate it. That said, it’s important to take a moment to discuss one of the major motives behind the day in the first place: raising awareness around the growing manufacturing skilled labor problem and exposing younger generations to what the sector has to offer.
Tweet this: #MFGDAY14: Manufacturing’s Skilled Labor Problem Explained http://bit.ly/1uDRlnY
According to recent U.S. Bureau of Labor Statistics data, nearly half of the manufacturing workforce—the proportion mostly comprised of “baby boomers”—is set to retire in the next ten to 15 years. As those professionals leave the shop floor for some much-deserved rest and relaxation, naturally they need to be replaced. But there are a few challenges standing in the way of companies simply swapping out the old and replacing them with the new.
The Dark, Dirty, Dangerous, Low-Paying Perception of Manufacturing
Namely, there’s the challenge of attracting the next generation of skilled laborers to the sector. For the most part, younger generations seem to be maintaining this mindset that manufacturing is full of dark, dirty, dangerous and low-paying jobs, despite the fact that the shop-floor environment has changed dramatically in recent decades. As a result, relative to many other industries fewer college-bound students and recent grads have a career in manufacturing on the radar.
With the pool of talent continuing to be sparse and more workers retiring, this is the foundation of manufacturing’s skilled labor problem. It’s the foundation, because the brunt of the problem is more complex and serious than that. The Bureau of Economic Analysis reported in 2013 manufacturers contributed $2.08 trillion to the economy, up from $2.03 trillion in 2012, and accounted for 12.5% of GDP. The manufacturing sector in America is moving forward, and consequently so is the demand for skilled labor. If this gap endures, it’s poised to put the U.S. in a competitive disadvantage.
What Manufacturing Is Really Like Today
The frustrating thing about this—but also the bright side—is that much of the skilled labor problem is merely the result of a misperception and lack of communication about what it means to be a manufacturer in 2014. Manufacturing is no longer dark, dirty, and dangerous—in fact, many of today’s workers are now using exciting technology like industrial automation, digital media, robotics, and simulation.
There’s also the fact that the sector’s largely driven by technology innovation, and that in and of itself is creating a whole new set of career opportunities. The Internet of Things (connected devices and intelligent sensors), virtual reality, augmented reality, wearables, 3D printing, and more, all have their place in manufacturing and should garner interest of the younger generations. Not to mention that because of the consumerization of IT, they’re also positioned to more organically understand these technologies.
With the sector becoming more digital and automated, outdated conditions associated with manufacturing facilities have been phasing out for decades. At a recent Siemens PLM analyst conference, CEO Chuck Grindstaff said, “Factory workers of the future, whether we’ll call them blue or white collar, that distinction will become harder to make.” In reality, manufacturing professionals today and increasingly those of the future are probably more likely to get carpal tunnel syndrome than lose a finger on the job.
To close this gap, manufacturers need a sustainable recruitment pool filled with professionals capable of understanding and using next-generation technology. And it’s important to note that those recruits won’t go unrewarded. Wages in the increasingly tech-centric sector have been rising over the years. The Bureau of Economic Analysis reported in 2013, the average manufacturing worker in the United States earned $77,506 annually, including pay and benefits, while the average worker in all industries earned $62,546.
Despite manufacturing's progress, though, it still has some issues. Few manufacturers have changed their management styles to accommodate digital natives. They don't have the social media savvy, the graphical UI experience, and—most of all—the management philosophy and style that accommodates today's youth. Other professions have made some of those adjustments, and so that is where youth is going. Meeting the youth on their own turf—so to speak—will be crucial for the industry as it goes forward. It’s not just about the money, manufacturers have to commit to making the workplace more attractive, and many are planning that investment or in the process of doing so.
Communicating What Manufacturing Has to Offer
So, the question is, how do we change the perception of millions of children, teens, and young adults and communicate that there are interesting and rewarding manufacturing careers today? It’s not an issue that’s gone unnoticed. Rather, schools, universities, associations, software companies, summer camps, maker spaces, and much more around the country are doing their part to offer the next generations of workers opportunities to experience the manufacturing environment.
And those behind Manufacturing Day have been working to do this for years. The collection of events are orchestrated by six national organizations, including Fabricator & Manufacturers Association International, National Association Of Manufacturers, Manufacturing Extension Partnership, Manufacturing Institute, Industrial Strength Marketing, and Science Channel. It’s sponsored by an additional one hundred more.
On Friday, October 3, manufacturers across the country will open their doors in an effort to connect with their communities, bringing to light the notion that manufacturing in 2014 is vastly different than the perception many have in their minds. It’s a collective effort to not just educate the public on manufacturing's role in America, but also to help them realize how it's evolved into an innovative and highly skilled working environment.
Participating organizations will be offering factory tours, career workshops, and open houses. Students as well as those already in the workforce will gain access to behind-the-scenes peek into why modern manufacturing is a viable career option. As shown below, events are already scheduled spanning nearly every state in the U.S.
Of course, raising awareness and overcoming the manufacturing skilled labor problem isn’t something that’s going to happen in a day. Like most major changes in public perception, it’s an effort that will progress incrementally. But this Friday is a great place to start for students, parents, teachers, public officials, and community members just joining the party. If you’re interested in attending a free event, more information can be found here.
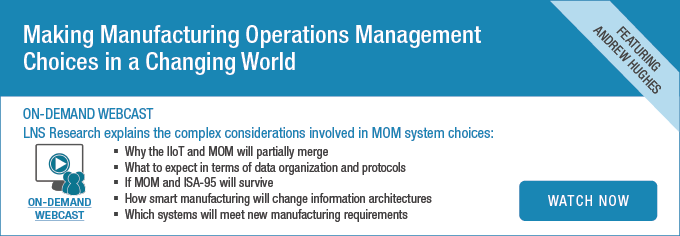