On December 3, LNS Research and Environmental Leader hosted a webinar entitled, "Capturing the Business Value of EHS Software." Throughout the event, we had an influx of questions and insufficient time to address them, which we'll do below.
For those who were unable to tune in live, the event was focused on the evolution and growing importance of Environment, Health & Safety (EHS) across manufacturing and production industries today, as well as how leading EHS professionals are deriving additional business value from integrating EHS initatives across the entire value chain as part of a larger Operational Excellence strategy.
This focus shows marked improvement in areas like Manufacturing Operations Management (MOM), quality management, risk, and compliance. More than ever, leading manufacturers are requiring more effective EHS management and software to meet their growing sustainability initiatives. Building upon this theme, specifically, the webcast covered:
- The top objectives and challenges of today's EHS professionals
- The criticality of EHS visibility across the value chain
- Strategies for building tighter EHS culture and streamlined processes
- Benchmark data on EHS software adoption and efficacy
- Recommended actions for success
The full on-demand recording of the webcast can be accessed here.
Q. How do you think the release of ISO 45001 will impact EHS?
A. ISO 45001 could go either way. If it becomes a go-to standard, it will take some time for it to gain traction. Of course it has the ISO name and brand behind it, but existing default standards like OHSAS 18001 have already become fairly entrenched, and a health and safety standard has been a glaring omission in ISO’s catalog for some time.
All signs say the new standard will be risk-based, like the newest version of ISO 9001, which could be a positive sign, given the increasing traction of risk management in EHS. But the jury is still out on whether ISO 45001 will establish relevance.
Q. What trends are you seeing in integrating energy management into EHS as a component of sustainability?
A. In our webinar we talked about all of the co-relationships that EHS has with all other areas of enterprise performance management, including asset performance, manufacturing operations, quality management, and more, and how all of these elements factor into overall enterprise sustainability management.
Industrial energy management speaks to so many of the key metrics—energy use, energy intensity, energy efficiency, for example—that factor into both environmental performance and holistic sustainability. So there is a clear relationship and a growing trend there, and that’s something we’ll dive into across our 2015 content.
Q. To what extent are you seeing company officers other than the VP of EHS embracinging or even championing these sorts of initiatives? Which roles seem to be most engaged?
A. I think the cornerstone of a program that can produce or appoint a sustainability champion has top-level executive engagement. The CEO/President has to have identified the kind of cross-departmental collaboration and the importance of the goals and objectives associated with sustainability objectives is critical to success as a company, but also has communicate to all parties that it is a corporate priority.
To answer the question, I’ve seen VPs and Directors of Sustainability act as the champion as well. It is hard to have someone without some executive authority coordinate sustainability initiatives effectively across all enterprise activities.
Q. Many companies find it difficult to make a business case for EHS software. Do you have suggestions for demonstrating the value of these systems to senior management?
A. Quick wins would be an immediate suggestion. I think when we evaluate EHS solutions we tend to get preoccupied with the ‘grand vision’ and the whole suite of offerings a vendor suggests it can provide. Sometimes an executive is fully invested in a complete, robust offering, and such situations provide a bit of leeway.
If those that hold the purse strings are reluctant, pick an area of EHS performance—Incident Management is a common go-to—and implement an aspect of a solution with clear objectives and KPIs (that, ideally, are tied directly to financial metrics) to demonstrate the success of a solution over a six-to-12-month period post-implementation.
This will build the case for further investment in a more comprehensive solution spanning all areas of EHS management.
Q. In your experience what are the numeric relationships between incident rates and profitability?
A. We often talk about the ‘iceberg’ in incident management: the fact that the hard costs of an incident (e.g. medical, compensation, insurance) are but the tip of the iceberg.
What's beneath the water, as it were, are the myriad costs of lifecycle incident management, including direct costs (claims management, remediational costs, legal fees, property damage) and indirect costs (e.g. worker culture, brand perception/equity), the latter of which are harder to quantify but do have bearing on overall costs.
Between building an incident ROI calculator and leveraging case studies for examples, it can be an easy process to prove the value of incident rates (and thereby costs) and revenue (and therefore profitability).
Q. Any particular reason for the rapid consolidation in fragmented market of EHS software solutions?
A. Just as we used to realize the efficiency costs associated with the many disparate and manual systems we used to use (e.g. paper-based documents, no document management system, isolated spreadsheets, etc.), now we are realizing the inefficiency costs associated with software systems that have poor or nonexistent interaction or interoperability and aren’t able to ‘talk’ to one another.
Lagging businesses are spending a lot of time reconciling data from one piece of management system software, or figuring out how to get it to better speak to other enterprise applications and ERP systems in general.
As alluded in the webinar, the similarity of frameworks behind management system approaches broadly in tandem with both the expanding collateral impacts one performance area (e.g. APM) has with another (e.g. EHS), and the growing potential of the relationships between data we are seeing, is presenting new opportunities that invite the consolidation of EHS and other enterprise solutions.
Q. What kind of business value are you seeing in sustainability reporting with EHS metrics?
A. For example, if we assume an average incident cost of $45,000, that only covers the direct costs of the incident--medical costs like emergency room/doctor visits, direct damage to property, and others that are immediately visible to the employer. This represents but the tip of the iceberg.
The actual lifecycle costs of the incident can be a staggering five to 10 times more, if not greater, when we consider uninsurable costs like associated production downtime, shipment delays, FTE and overtime costs, training replacement workers, potential regulatory penalties, impacts on employee morale, legal fees, brand damage, and an array of other factors, depending on the situation.
So to take a small sample of metrics we can tie to financial performance when evaluating the costs of an incident, we might consider:
- Lost-time
- Incident-related administrative costs
- Replacement training hours/replacement wages
- Incident-related OSHA penalties
- Incident-related claims costs
Over time the lifecycle costs of that one $45,000 incident can amplify to between $180,000 to potentially over $400,000.
Interested in learning more about EHS Management and Software? Check out our new complementary eBook on the topic. You can get it by following the button below:
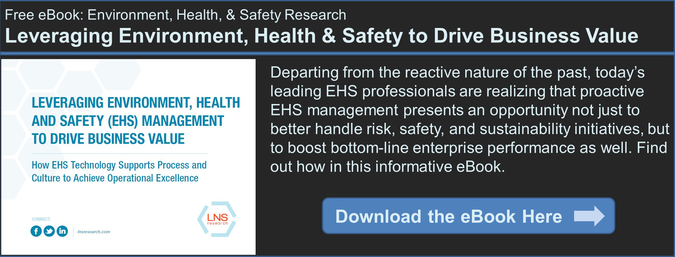