Most people think quality's all about compliance, but it delivers operational benefits as well. From our research, it’s apparent that companies that have taken an integrated, holistic approach to quality with technology such as enterprise quality management software (EQMS) considerably outperform others in key quality performance indicators.
In identifying areas for cost savings and efficiencies, it's often helpful for an organization to focus on measuring and continuously improving the overall equipment effectiveness (OEE) metric. Combining parts of quality, efficiency, and asset availability, OEE is a holistic business measurement that many market leaders are focusing on.
With the use of benchmark data from LNS’s 2012-2013 Quality Management Survey, this post will discuss which technologies and strategies organizations are utilizing to improve OEE as well as provide some insight into the performance improvements experienced by organizations that have implemented an automated EQMS solution.
The Operational Benefits of Enterprise Quality Management Software Processes
When used correctly, the OEE metric can deliver visibility into the effectiveness of quality management processes and solutions from across the value chain. Today, many of these processes can be automated with EQMS, providing managers with a robust, centralized and standardized solution for globally inspecting quality process data and content.
Automating the following processes and functionalities with EQMS can have a dramatic impact on OEE:
Automated CAPA management streamlines traditionally manual and paper-based processes such as approvals and escalation. EQMS facilitates the use of CAPA management, enabling organizations to identify root causes quicker and communicate those root causes to the entire organization, which is a critical component for realizing continuous improvements in processes as well as OEE over time.
Change Management
In many cases, manual change management processes have resulted in a lack of communication, making it difficult to identify how a specific change may have impacted a manufacturing process. By automating change management, managers can leverage a centralized solution as products and processes alter over time, facilitating the prevention as well as resolution for any nonconformances that may arise.
Audit Management
The process of audit management can be beneficial to both internal and external efficiencies. By automating the process with EQMS, organizations can ensure that issues are being identified, resolved, and followed up on in a timely manner. Especially in a large, global organization, a strong, automated, standardized, and centralized audit management solution can provide considerable improvements to efficiencies that reach down to the bottom line.
A main challenge many companies have is realizing the potential of the global supplier network. Suppliers can help to improve costs, but the lack of visibility into upstream operations often gets in the way of this. By automating SQM with EQMS, managers can open up a line for communication and collaboration with suppliers and partners, which can help to identify nonconformances earlier the in value chain.
Which Functionalities are Organizations Automating with EQMS?
The 2012-2013 Quality Management Survey asked nearly 500 executives questions regarding people, processes, technology, and metrics. Those executives that indicated using EQMS to manage quality were prompted to list which specific functionalities their organizations currently had implemented, which is depicted in the chart below.
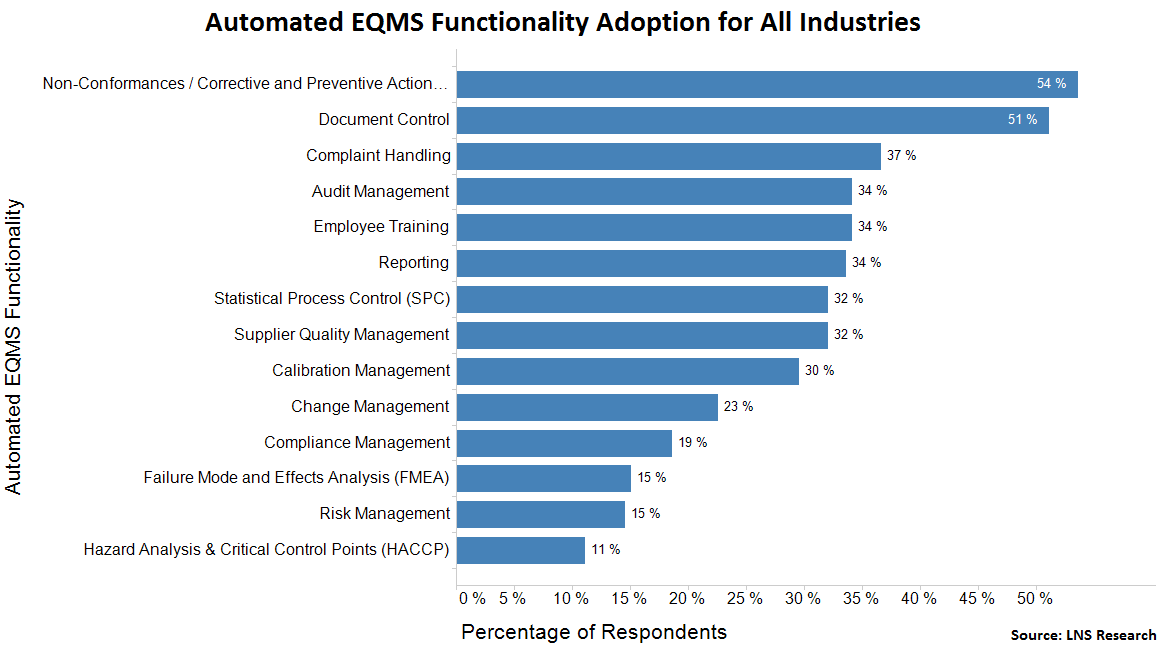
54% of companies are automating the CAPA process with Enterprise Quality Management Software tweet this stat!
As you can see, 54% of executives stated automating the CAPA process with EQMS. Numbers were lower for the other functionalities that have a direct impact on OEE, with audit management at 34%, SQM at 32%, and change management at 23%. However, from our discussions with industry-leading executives, there is a growing interest in the EQMS solutions category and this will be an important data point to inspect over the years.
The Impact of EQMS Adoption on OEE Performance
In our analysis of the quality data, one area that stands out is the impact of EQMS on OEE. As shown in the chart below, executives that listed having an EQMS solution outperformed others with a median OEE performance of 88%. This is considerably higher than those companies with no plans for an EQMS implementation (79.5%).
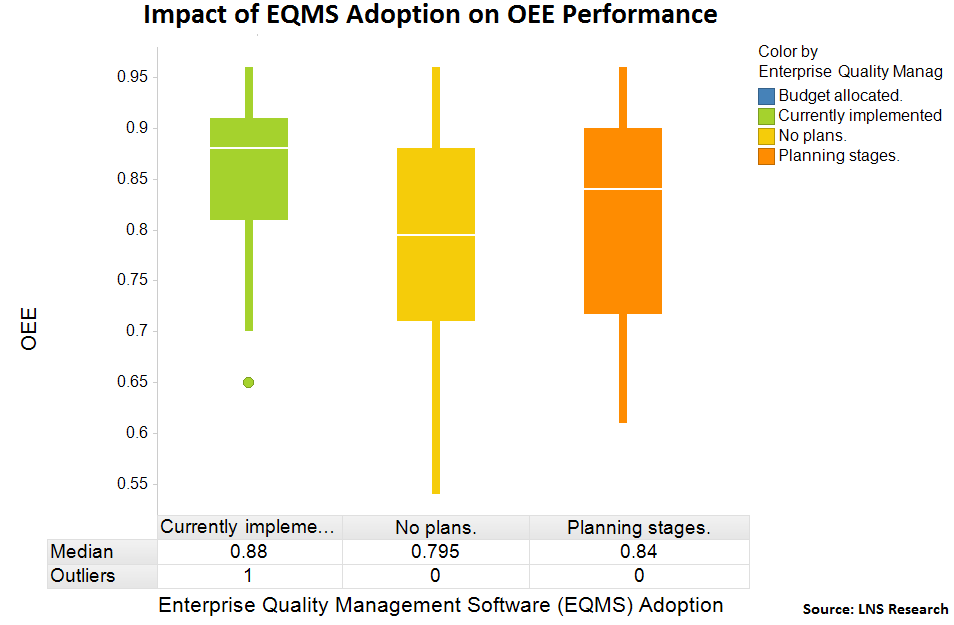
Companies that automate quality processes with EQMS outperform competitors in OEE performance tweet this stat!
With more than 50% of organizations using an EQMS solution reporting a median OEE of 88% or higher, this is strong evidence of the consitencies that EQMS can deliver to quality management. Companies looking to improve the OEE metric should consider implementing an automated EQMS solution to strengthen the effectiveness of that individual process as well as related processes that can benefit from a closed-loop quality environment.
There are a variety of ways companies can implement an EQMS solution, ranging from standalone functionalities or modules to extensions of existing enterprise IT investements. It is highly recommended that those responsible for making quality management decisions educate themselves on the EQMS space.
LNS Research's EQMS Solution Selection Guide has helped hundreds of exexcutives on their quality management journies learn about the software category's top vendors. It can be found below. In the comments section of this post, please feel free to share your experiences with automating quality management processes.
You might also be interested in:
Manufacturing Metrics: First Pass Yield Benchmark Data
Cost of Quality: What's Driving EQMS Adoption?
Reducing Risk and Improving OEE with Audit Management