Because research has shown that the earlier a defect or nonconformance is caught the less expensive it will be in the long-run, it’s critical that end-to-end quality capabilities extend from suppliers all the way through service and everything in between. This is especially true in discrete manufacturing industries such as electronics or high-tech, where the ability to balance quality and product complexity is often the source of a competitive advantage.
To achieve this balance, one area market-leaders are investing in is supplier quality management (SQM). SQM capabilities that enable communication and collaboration with design and manufacturing are central to reducing the instance of a defective part or component from making its way into the supply chain in the first place. We’ve seen that companies with effective SQM capabilities tend to perform better in key quality metrics, which are often indicative of financial performance.
With the use of benchmark data from LNS’s 2012-2013 Quality Management Survey, this post aims to highlight several trends in and key functionalities for managing the quality of suppliers.
Critical Technologies for Managing the Quality of Suppliers
Ensuring that your supplier relationship reaches its full potential requires not only a high level of visibility, but also the ability to interact and understand the risk of engaging in business with upstream partners. There are three important functionalities to note, each of which are increasingly being offered as part of the larger enterprise quality management software (EQMS) portfolio.
- Real-Time Visibility of Supplier Data with Statistical Process Control (SPC): Real-time visibility of test data as well as manufacturing data helps OEMs eliminate the black box effect of outsourcing critical components. It also eliminates surprises on the receiving dock nonconforming materials. Adding SPC to this data further enhances visibility by allowing for action to be taken before a process becomes out of control. Unfortunately, there are challenges to implementing this approach. Suppliers have to believe it won't just be used to further squeeze on pricing but will allow for shared benefits and a deeper collaborative relationship.
- Supplier Risk Scorecards: Scorecards enhance the operational risk management aspects of SQM, providing a central and standardized environment for suppliers to be rated based on past and current performance. By keeping up-to-date supplier scorecards, experiences (good and bad) can be shared across the enterprise and managers can make more informed decisions that will positively impact the operational risk portfolio. In discrete manufacturing industries where companies typically have to rely on the global supplier network, scorecards are vital.
- Supplier Portals: Often delivered over the cloud, portals open up a line of communication and collaboration that can help internal decision makers identify non-conformances or deviations before they make it into the supply chain. In addition to enabling cross-functional interaction that’s imperative for closing the loop on quality issues between suppliers and manufacturing, with real-time visibility into upstream operations suppliers are held more accountable for performance.
Intel's Supplier Portal as a Market-Leading Example
With the rise of EQMS, the global adoption of scorecards and portals is gaining momentum. A great example of this is Intel’s web-based Supplier Quality Portal. Front and center, a quote from the company’s Director of Materials Quality and Reliability supports this notion: “Our mission is 100% of materials and services used by Intel and its customers will function as expected at the lowest total cost. Clear and high quality communication between suppliers and Intel is one of the key items to achieve this mission.”
The Impact of SQM Capabilities on Quality Metrics
Although there are a number of metrics (cost of quality, OEE, first pass yield) that experience improvements when supplier quality technologies are used, we will hone in on one specific to discrete manufacturing industries: new product introductions (NPI). In the fast-paced world of, for instance, consumer electronics, quick and effective NPI cycles are often required for survival. With reliance on global suppliers to battle ever-tightening operating margins, supplier portals are making a significant difference.
The data point below was taken from LNS’s Quality Management Survey, cross-analyzing the adoption of a web-based portal that streamlines supplier quality data with NPI performance. As shown, companies that currently had these automated data collection capabilities outperformed others in successful NPIs with a median performance of 94%, as compared to 70% performance for those without the capability. For discrete manufacturing companies, this data point alone is enough to warrant an investment.
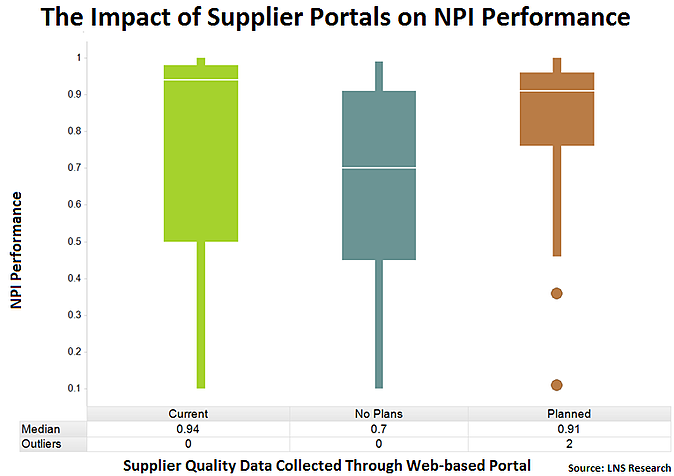
Because supplier portals automate and enhance many of the traditionally manual processes that impact NPI, the data point shown in the box plot above makes sense. Rather than having to rely on email communications and Excel spreadsheets, companies using these portals have more visibility into delivery times, production status, and inventory control.
Strengthening the argument, the automation aspects of supplier portals are only part of the equation. Although the data point above depicts the automation capabilities of portals, it’s important to remember that it is a two-way street. There is also the capability to communicate with suppliers to share changes to best practices, standards, quality specifications, and so on.
Learn More about the Benefits of Supplier Quality Management
For a more complete discussion of the positive impacts that supplier quality management can have on quality metrics and operational performance, join LNS’s President and Principal Analyst, Matthew Littlefield, in a webcast this Thursday, June 6, at 2p.m. EST. He will highlight which are the right quality metrics to measure and provide a roadmap for making dramatic improvements in performance.
You might also be interested in:
Top 6 Challenges in Electronics Manufacturing
Reducing the Cost of Quality in Electronics Manufacturing
Overall Equipment Effectiveness: Benchmark Data by Industry