The way technology’s improved manufacturing and industrial capacities over the past few decades is fascinating. A great example of this is the evolution of work instructions. What was once just a printed list of step-by-step directions created by supervisors and engineers for shop-floor workers has transformed into a high-tech, interactive process.
Today, electronic work instructions (EWI) software is instrumental to the shop floor. And market leaders are investing in the integration of EWIs with 3D visualization and simulation software, so operators aren’t just following along with instructions, they’re able to view animations of each step and sometimes even improve things right on the spot.
In this post, I’ll break down what you need to know about the past, present, and future of electronic work instructions in manufacturing operations management, as well as discuss eight ways they’re transforming the shop floor.
From Paper-based to Next-Generation Electronic Work Instructions
It’s vital that you have clear and repeatable instructions for every manufacturing process. Traditionally, shop-floor workers would hang laminated pieces of paper on the wall with diagrams and explanations of each step. The shortcomings of this are obvious, particularly when an engineering change order (ECO) was required and those changes needed to be sent to engineering, revamped, sent back to manufacturing, reprinted, relaminated, and so on. If we’re talking about a global operation, this becomes even more of a challenge.
The more complex something you’re building is, generally the more complex those instructions have to be, and a paper-based approach can be limiting. But computer technology on the shop floor wasn’t always as easily accessible and widespread as it is today.
Since document control software has become widely adopted, however, EWIs have made their way into the manufacturing environment. EWIs have improved the way supervisors and operators build products, and the way they interact with engineers and maintenance personnel. The technology enables a centralized, standardized, and automated document management system, and can be found on most modern manufacturing shop floors.
In addition to improving communication and collaboration on the shop floor, streamlining EWIs mitigates many of the traditional risks associated with changing a work order. In the past, an engineering change may have been ordered, but never completed or at least never communicated to the appropriate personnel once completed. With automated workflows, notifications can be triggered to ensure the process is completed and the appropriate personnel are notified. Workflows can also ensure that the right instructions are being followed on time and in the context of the manufacturing process.
As the use of simulation and 3D visualization software becomes more prevalent, moving from engineering onto the shop floor, EWIs are becoming an even more effective tool. By integrating EWIs with this technology, an operator can watch each step of a process played out via animations. In some cases, operators and supervisors are trained to actually make changes and improvements to these processes in real time rather than waiting for an ECO.
With the continuous advancement of technology, we expect to see further integration between plant and process design, 3D visualization, simulation software, workflow software, manufacturing execution systems and electronic work instruction software.
The Role of EWIs in the Manufacturing Operations Management Software Platform
Increasingly, modern manufacturing operations management (MOM) platforms offer EWIs as an application within a broader portfolio of applications that integrate via the same software platform. Standardization on the MOM platform facilitates the sharing of information and workflows, and is often a driver of greater collaboration capabilities in globally distributed manufacturing environments and even between functional units.
The infogrpahic below helps to put EWI's positioning in manufacturing operations management into perspective.
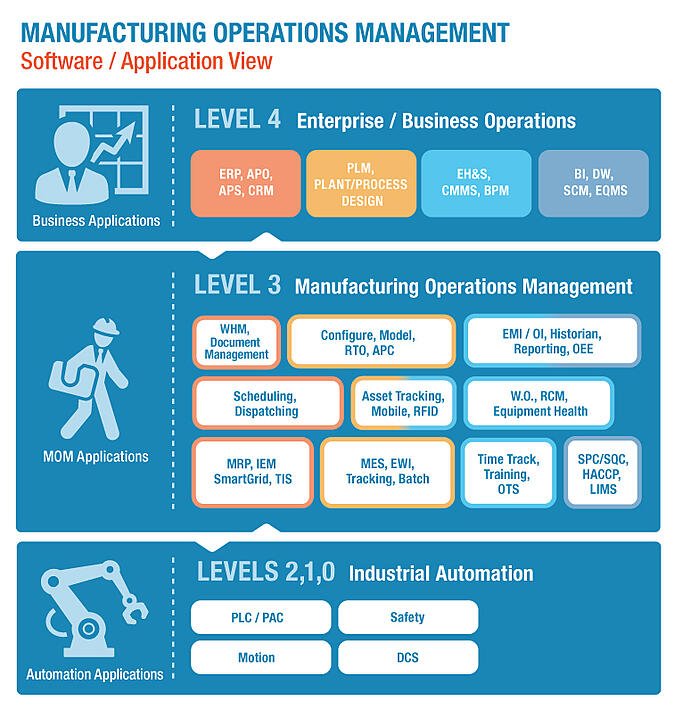
8 Benefits of Electronic Work Instructions
Moving from paper-based work instructions to EWIs, there are many benefits. When accounting for the centralization, standardization, and automation capabilities offered by today’s MOM software platforms, those benefits increase dramatically. Below are 8 ways EWIs are improving shop-floor operations and making manufacturers more effective:
- Reduced downtime: Because communication is easier with an electronic routing and delivery system, less time is required to take maintenance actions or make engineering change orders.
- Stronger Communication: A centralized document management system enables greater ability to share documents across within the manufacturing environment, across facilities, and between functional units. Stronger communication creates fewer errors.
- Closed-loop manufacturing and quality processes: With a centralized platform, EWI/ECO content and data can be more easily shared with corrective and preventive action management and audit management processes.
- Closed-loop manufacturing and engineering processes: With a centralized platform, EWI/ECO content and data can be more easily shared with the failure more and effects analysis (FMEA) processes.
- Reduced waste/scrap: The ability to communicate and collaborate with engineering more effectively helps to improve first-time quality and reduce waste in the manufacturing environment.
- Easier communication of regulatory changes: Because many industries face dynamic regulatory environments, EWIs help to quickly communicate changes required for shop-floor processes and validate that personnel have been made aware of and are following them.
- Faster new product introduction process: Streamlining communication and collaboration between manufacturing and engineering reduces the time required to develop, test, and build new products.
- Reduced risk and improved efficiency: With automatic notifications triggered for both shop-floor and engineering workers, the likelihood of a non-conformance or compliance issue is much lower.
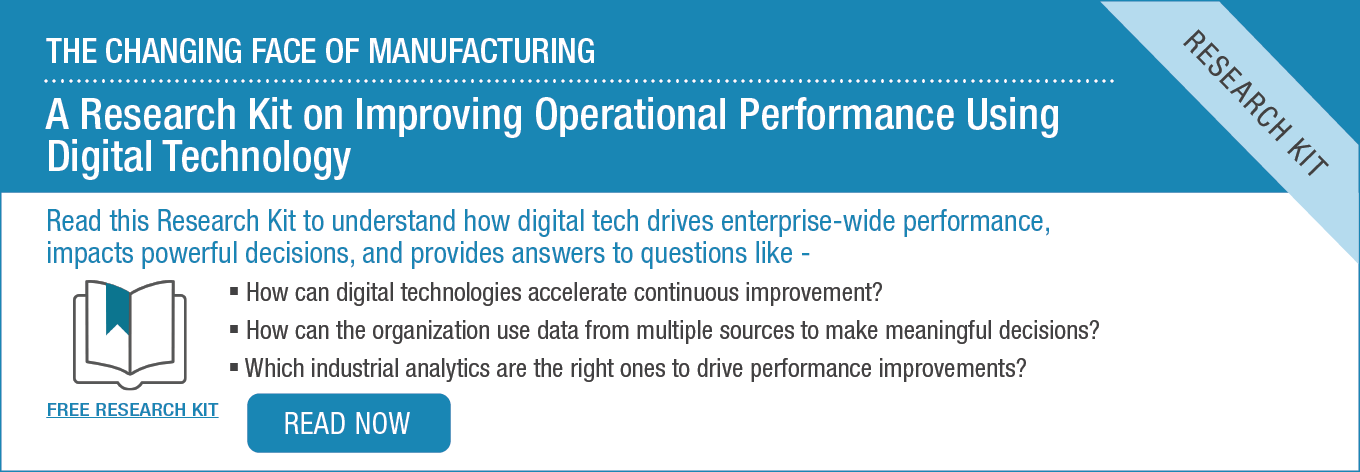