Today’s manufacturing environment exudes more data than most companies know how to handle. For a global manufacturer, it’s typical for there to be hundreds or even thousands of different processes, data sources, and systems in place. While this data can be one of your greatest assets, in many cases it’s surfacing as a source of confusion and proving too difficult and costly to manage. For many, IT architecture is actually the foremost challenge for achieving visibility into manufacturing operations.
Relatively recent advancements to manufacturing software technology, however, have turned this abundance of data into a competitive advantage for cutting-edge manufacturers. Market leaders are taking a software platform approach to manufacturing operations management (MOM) software, effectively simplifying and rationalizing traditionally disparate applications and data sources. Moving away from a variety of monolithic database-driven systems, the analytical capabilities found with modern MOM software solutions are delivering dramatically more actionable intelligence while requiring only a fraction of the resources.
In this article we’ll discuss the challenges with traditional manufacturing IT architectures, and how taking a MOM platform approach to operations can help to overcome them. We’ll also discuss why such an approach is critical to harnessing the future potential of manufacturing Big Data on the horizon.
Identifying the Source of IT Disconnects In Manufacturing
Looking at data from our 2013 Manufacturing Operations Management survey, we can put this challenge into perspective. In one question, we asked executives about their manufacturing challenges, and they were instructed to select three their top three. As shown, of the nearly 300 executives who took the survey, 25% reported that the number systems and data sources in place were a roadblock to achieving their strategic objectives.
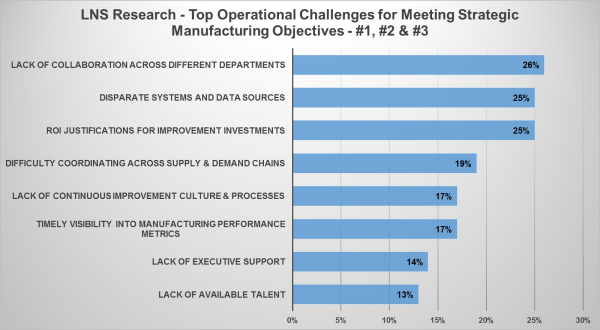
The culprit behind this data management challenge is likely a combination of factors. For starters, in the past there were simply technological limitations, many of which are still impacting operations today. Also, shortsighted IT investment strategies have left many large manufacturers with a variety of disconnected but overlapping solutions. And finally, M&A activities add a layer of complexity. With newly acquired or merged organizations entering the mix, comes a diversity of new technology that needs to be managed. The result is a disconnected IT architecture that’s not providing as much value as it should.
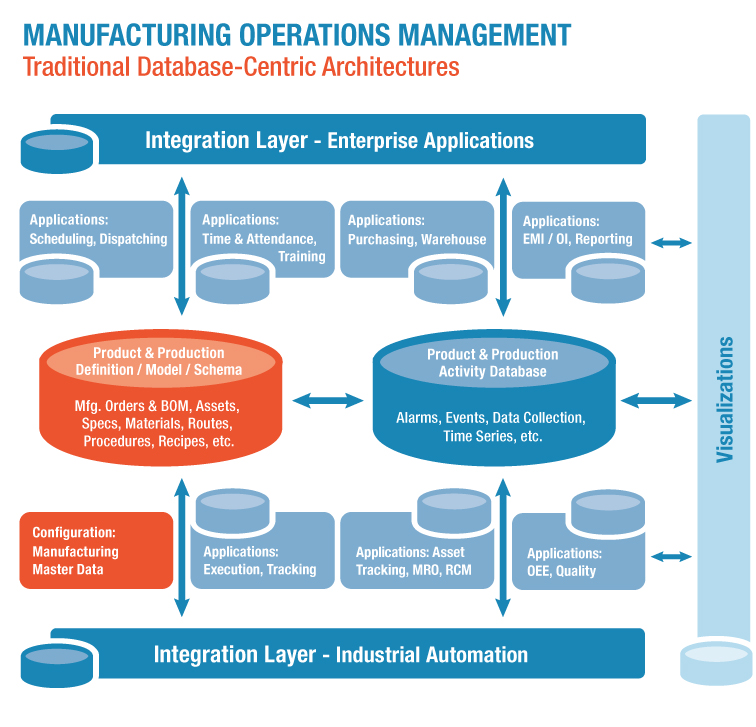
With disparate database-centric applications to collect data, visualize performance, manage business processes, and provide analytics for continuous improvement, the above scenario is common in today’s manufacturing environment. It is because of architectures such as this that many companies face challenges with achieving global visibility.
Next-Generation Manufacturing Software Platforms
Today’s leading manufacturing software vendors are transforming manufacturing data into a vital resource for personnel on the shop floor up through the executive suite. With open standards-based collaboration and integration capabilities, these platform-based solutions are enabling organizations to break down the traditional silos associated with manufacturing IT and deploy highly modular and scalable functionalities.
The elements of standardization and centralization included in MOM software platforms are central to simplifying the achievement of global visibility. Below is an image of what LNS Research believes is the not-too-distant vision of what manufacturing software platforms will look like.
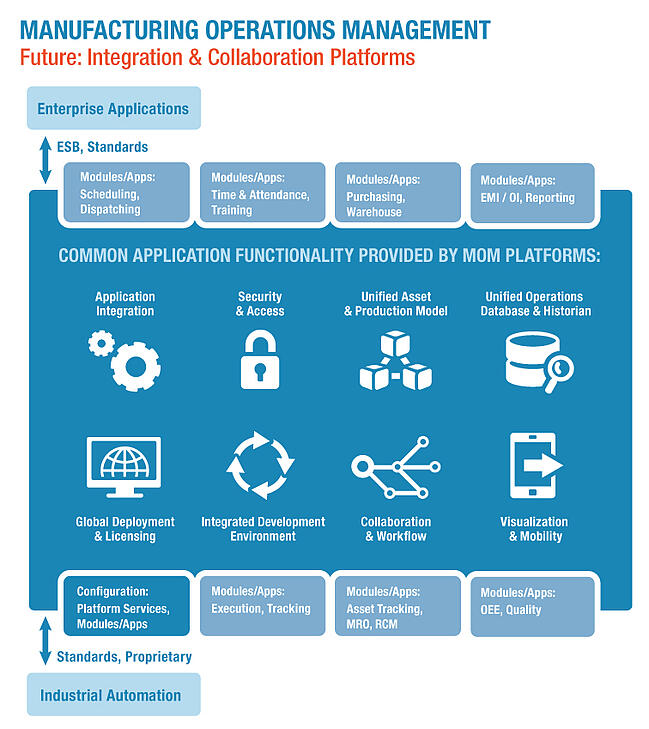
In contrast to the traditional manufacturing IT approach, the future doesn’t require multiple monolithic applications and the resulting clutter of different integration, data collection, and visualization tools. With this approach, the platform typically provides automated data collection, analytics and dashboards, and interoperability with other systems and application functions such as manufacturing execution (MES) and enterprise quality management (EQMS).
Achieving Global Visibility on a Common Platform
As we've written about previously, harmonizing business systems with next-generation manufacturing technology will continue to become less of an innovative strategy and more of an industry standard. Manufacturing organizations churn out massive amounts of data every day, and having the ability to easily deploy consistent instances of solutions like manufacturing execution and quality management, with that data rolling up throughout the enterprise, is emerging as a main focus for manufacturers around the globe. It's important for managing real-time manufacturing non-conformances, as well as for enterprise-wide continuous improvement intiatives.
With the number of connected devices poised to grow rapidly in the next decade, overcoming the challenges of volume, velocity, and variety associated with big data will be significantly facilitated with a more structured and rationalized IT manufacturing software architecture in place. Executives at market-leading companies are already thinking about not only how their current manufacturing software platform can deliver actionable intelligence, but also how it will perform amid the impending big data revolution.
Those are just some of our thoughts on global visibilty in manufacturing. Feel free to share your own below or tweet them to us @LNSResearch. To learn more about this topic, read our recent report Driving Global Visibility and Analytics in Manufacturing.