The current buzz-term “Big Data” may be slightly misleading in the strictest sense. The concept is nothing new. Most manufacturers are quite accustomed to having “big,” some might say huge, amounts of data flowing throughout their organizations, but have historically lacked the context that gives that data actionable meaning—giving birth to the oft used phrase, “data rich, but information poor.”
And that’s where the emerging technological capability we refer to as Big Data is coming into play. The potential for previously unknown correlations to be discovered, for informational silos to be demolished, is accelerating. While perhaps data didn’t exactly lie to us before, it’s going to be compelled to tell us many more truths in the future.
But this technological Big Data concept is still both nascent and broad enough that nobody is entirely sure how it will play out in manufacturing, although the possibilities are overarching and potentially transformative.
In moving this conversation forward around Big Data, as well as other emerging trends like mobility, cloud technology, and how to implement metrics programs that drive the most manufacturing performance improvement, LNS Research teamed up with MESA International to create the 2013-2014 ‘Metrics that Matter’ survey. With over 200 responses to date, the survey aims to identify the ways leading manufacturers are approaching these and other manufacturing technologies and initiatives. In this post, we’ll share some early analysis of Big Data trends and attitudes among today’s manufacturers.
Big Data in Manufacturing: Big Potential for Operational Benefits
One of the survey questions asked respondents to give their opinion on the ways they feel companies will mine both plant and enterprise Big Data for improving manufacturing performance. Respondents were not limited to one response.
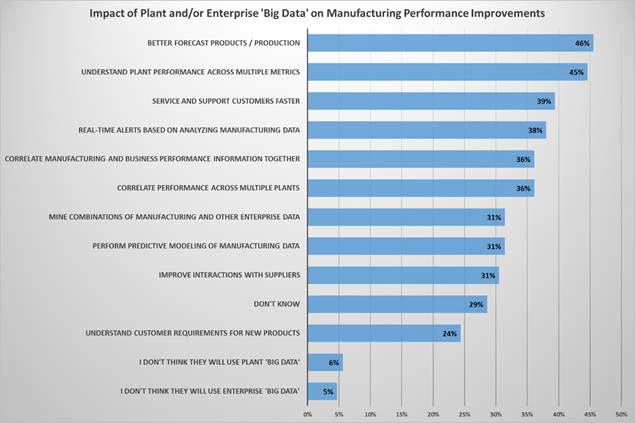
Tweet this chart!
As the largest overall function of a manufacturing company is to ultimately produce products, it’s not surprising that better production/forecasting was the top response from survey respondents, with nearly half choosing this response. Here Big Data could operate in a myriad of ways, including identifying correlations between customer data, scheduling, and maintenance, which would have the potential to identify hidden patterns that could enable greater operational efficiency, better anticipate order lead times, shorten asset/machine downtimes, and make materials purchasing and WIP decisions more effectively.
Other top responses, such as being able to understand plant performance across multiple metrics (45% of responses), servicing and supporting customers faster (39%), and real-time alerts based on analyzing manufacturing data (38%) are in line with some of the important objectives and challenges we’ve heard manufacturers speak about throughout our research, such as finding ways to overcome informational silos/disparate data sources and systems and maintaining/developing a more customer-driven organization.
In echoing these themes, it seems clear from these responses that manufacturers today are poised to take advantage of Big Data analytics to attack their biggest and most important challenges and objectives.
Reinforcing this, it’s also interesting to note that of the top nine responses given, each has a response rate of over 30%. A mere 5-6% felt that Big Data would not have any future use or impact on their manufacturing performance. This is a clear indicator that manufacturers today are viewing Big Data as a transformational, game changing technological capability that’s likely to have broad implications across the organization and enterprise as a whole, and indeed this fits our view of where Big Data is likely to lead.
Learn More about Manufacturing Performance Metrics and Emerging Technologies in April 16th Webcast
As time moves forward and Big Data capabilities evolve in manufacturing applications, we’re sure to see this list of operational benefits follow suit. And manufacturers will forge new operational paths using this technology that will have a ripple effect on other areas of the business, culminating in substantial bottom-line improvements.
But to maximize operational benefits and get the best of any software solution or technological innovation, it’s also important to know which metrics and measurements are really driving the most value, so you can understand which to compare—where to dig for correlations. And in the grand scheme of things, Big Data is one large piece of technological puzzle that includes ERP, PLM, MOM, MES, mobility, cloud technology, and more. Where do these pieces interlock to drive the most operational benefits?
To find out more about these emerging trends and how leading manufacturers are realizing performance improvements with their metrics programs, be sure to stay tuned for more details on the free LNS Research/MESA webcast on April 16th, '2013-2014 Manufacturing Metrics That Really Matter.' It will be moderated by MESA Outreach Director, Julie Fraser, and presented by LNS Research Principal Analyst, Mark Davidson. Attendees will receive a free copy of the ‘Metrics that Matter’ summary report.
In the interim, we invite you to download a free report which covers a range of helpful best practices for Manufacturing Operations Management: