While not a new thing, risk management is increasingly embedded into aspects of environment, health and safety (EHS) performance, as well as all other aspects of corporate performance, including manufacturing operations, asset performance, quality management, and supply chain management among others.
From Deepwater Horizon to the Dhaka, Bangladesh, factory collapse, a number of recent, high-profile examples of risk management gone wrong have helped underscore the role of effective risk management.
Yet, from a plant manager’s perspective, risk can often come across as an abstract, top-management priority that doesn’t clearly relate to their roles or the boots on the ground they are responsible for. And that’s understandable. The day-to-day concerns of managing plant personnel, keeping them safe, and preventing potentially large-scale environmental crises can weigh heavily on the minds of those responsible for general operations. However, every identified chink in the armour of an effective EHS performance management program represents an opportunity for systematic improvement within the plant and across the enterprise.
In this article we’ll explore four things every plant manager ought to know about the often over-convoluted realm of operational risk management.
1. Risk is All Around You
Risk is pervasive in operations and ignorance doesn’t change this fact. The most obvious and effective place to identify and mitigate risk is right on the plant floor. When we look at the causes of large-scale disasters, employee injuries or deaths, or environmental crises, they are generally attributable to something that occurred (or was ignored) on the plant floor.
When an adverse event occurs, it can typically be traced back to a very specific event that occurred in a specific location at a specific time. Whether it was an underperforming asset that was poorly monitored, a fall hazard that wasn’t properly identified, or a piece of heavy equipment that had under-maintained machine guarding, analyses of adverse events almost always point to a specific concern that arose on the plant floor.
So while the precepts of risk management can seem nebulous, know that the causes related to risk management gone wrong are always very concrete. In your company, risk management, broadly, may fall under the purview of a specific executive champion but these executives don’t understand the details of operations and associated risk factors. The solution, as a plant manager, is to take ownership of maintaining and using an effective risk register.
2. Operational Risk and Enterprise Risk Need a Symbiotic Relationship
We often talk about Operational Risk Management and Enterprise Risk Management as if they are isolated management frameworks. This might cultivate the perception that they are, but nothing could be further from the truth. Instead, they are simply two different levels of granularity into evaluating risk, and though they occur at different levels of organizational management, they ought to work with one another in a feedback-oriented, continuous improvement loop.
The right enterprise risk register will take a localized risk-based issue—for example, a faulty asset or repeat behavioral concern—and then record and classify that issue, and apply corrective measures at the plant level, of course, but then go beyond by taking the ‘shape’ of that issue and extending it across similar sites across the enterprise.
For example, if one plant in Boston has identified repeat machine guarding issues within that particular site, the Identify-Assess-Control-Monitor and Respond ORM process applied at that site ought to then be extended to similar sites in Houston, Detroit, Beijing, and beyond. This is a very proactive way of applying risk lessons learned across the enterprise, instead of keeping them holed up at one site. That approach may serve the site well, while serving the operation poorly. Plant managers need the tools to both push local risk scenarios from their plant out across the enterprise and also pull risk data into their own plant.
3. The ‘Smallest’ Risk can Become the Biggest Organizational Disaster
It is tempting to think that our localized risks, should they manifest into adverse events, will not necessarily be crippling for the organization at large. But we need not look further than the biggest Gulf of Mexico oil rig disaster or the recent Bangladesh textile factory collapse to know one isolated (and arguably preventable) event can upset stock prices, cause enormous brand damage, and result in vast fees, fines and reparation expenses.
As plant managers, it can be easy to believe the daily risks and concerns we encounter are ours alone, and that’s understandable. But know that, however unique our individual operations are, the general pursuits, processes, and problems we encounter are realized to some extent (albeit in subtly different ways) across all of the plants across our global enterprise.
In operations, the only way to eliminate bias or assumptions that we may have about our operations is to systematically quantify and prioritize the risks in the risk register and maintain this process over time.
4. Effective Operational Risk Management Equals Improved Profitability
To put it lightly, adverse events are, well, expensive. To varying degrees, of course. A moderate, local occupational health and safety claim—that’s one thing. An undermaintained asset that causes an explosion that results in leaks, injuries, and death—that’s quite another.
The impacts of one adverse event can be orders of magnitude higher than those of another, smaller adverse event. And the lifecycle costs of dealing with minor adverse events are already sizeable, and they multiply accordingly for large-scale events.
The right risk management program will tie actual and possible adverse events to bottom-line costs, from a clear dollars perspective. Just as risk management can be nebulous at best to some plant managers and frontline personnel, the value in risk management done right can escape even the most thoughtful of business executives. When risk—operational and enterprise—is linked effectively to dollars, those that hold the purse strings tend to open their eyes.
Of course, all risk management activities are fruitless if in the end no action is taken. Once risks have been catalogued, quantified, and prioritized, resources must be assigned to mitigate the risk factors and eliminate future adverse events.
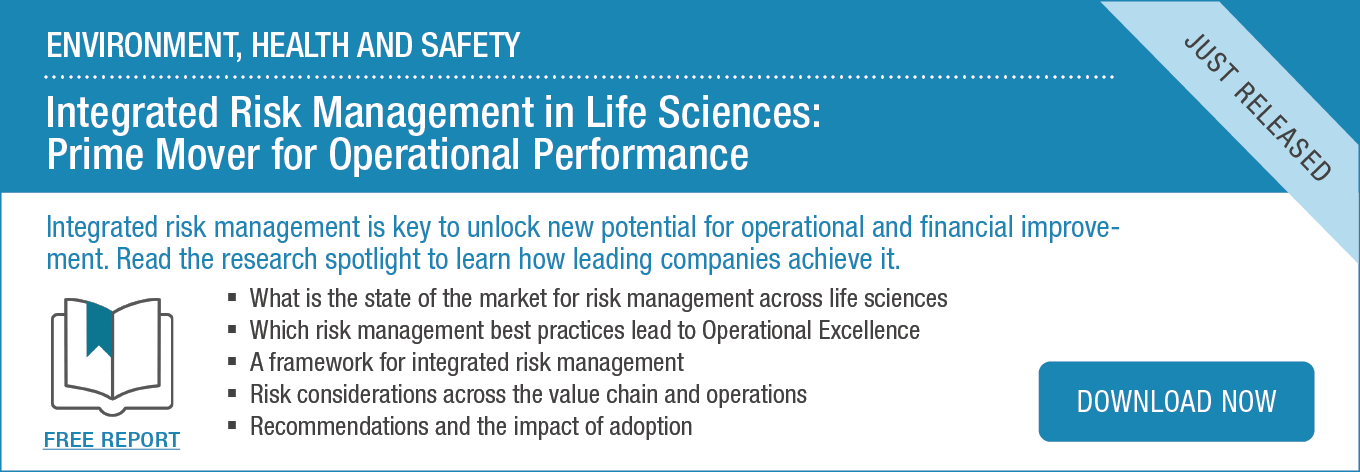