On November 13, LNS Research and FDA News hosted a webcast entitled, "A Roadmap for Addressing Quality and Manufacturing Challenges in Life Sciences: Moving Beyond Regulatory Burdens to Enable New Collaborative Models for Growth." As usual, we received more questions during the course of the event than we had time to answer live. In this post, I'll answer some of the top questions that went unaddressed due to time constraints.
For those who were unable to attend the webcast at its original air date, here's a little background on what we covered. Drawing upon our Manufacturing Operations Management (MOM) and Quality Management surveys, as well as industry-specific research, the event focused on best practices for the very demanding challenges life sciences companies face today in meeting compliance initiatives and traceability market demands in the midst of a paradigm shift.
The webcast drilled down on several key aspects of the connection between quality and manufacturing initiatives increasingly necessary for success within life sciences industries. Specifically, it discussed:
- How new FDA regulations, global population trends, and moves toward personalized medicine are placing unprecedented strain on life sciences companies
- Why life sciences is particularly plagued by the "quality as a department" mindset, and the importance of a shift to proactive, rather than reactive, quality management
- How today's MOM and EQMS software applications are enabling life sciences companies to achieve key capabilities of closed-loop quality management and end-to-end product traceability
- Benchmark data and actionable recommendations for success
The full on-demand recording of the event can be found here.
Questions & Answers
Q. Has production asset management entered discussion within the industry?
A. An important convergence for quality and asset management is reliability, warranty management, and design for quality. The roles and algorithms responsible for these areas have a lot of overlap and are beginning to come together, both for vendors and end-users.
Q. Is there any foreseeable tradeoff between having a complete EQMS and maintaining confidentiality of proprietary information?
A. Often the first questions asked of an EQMS vendor are of the ability to provide federated security, connection to Active Directory, or a single sign-on (SSO) mechanism. Any vendor worth consideration has one or more of these options. Having ticked this box, the next question is that of form- and field-level security. This is the key to providing context for an automated process to work across the enterprise while preserving sensitive information for only those authorized to see it. This is synonymous with occupational health and safety (OHS) solutions that track personal information--the so called "privacy case." There is a slight trade-off with regard to safeguarding some less-sensitive information and the concept of true enterprise process harmonization yields significantly more benefit than a potential minimal exposure to information. If you ask most security experts about breaches, they will support the notion that these are people- and not technology-driven.
Q. How would you define success for these life science companies? Is it Quality Assurance or Operational Excellence?
A. Success is a moving target but for most the move from a paper-on-glass manual solution to a harmonized and automated solution and the efficiencies and traceability therein is the first return. achieving this is a huge leap and provides the room to set and achieve the next objective. Connecting stakeholders across the value chain promotes collaboration, and with new-found visibility and control typical QA activities are improved. Strategic objectives can be achieved and visibly demonstrated with a bedded-in EQMS, and though operational excellence means different things to different organizations, the EQMS will provide a mechanism to accelerate goals therein for that journey.
Q. Does having separate best-of-breed systems for PLM, MOM, and EQMS create a nightmare for IT integration? Any recommendations in this regard?
A. We see ERP and PLM providers with excellent EQMS functionality in this space. Often, expanding out from existing platforms is a good option but there is no one-size-fits-all. Regardless of whether an organization elects to deploy a pure-play EQMS or build out, there are integration challenges. The key is to identify the must-have integration points and ensure that there is maturity there from the provider and a Web services or proprietary connector set in place. Individual custom connectors can significantly delay implementation and have the potential to spiral costs.
Q. What kind of validation and verification is required to satisfy regulations to implement EQMS or any ERP? Are there specific things end-users should have in mind?
A. End users must (in life sciences) explore the validation options provided by the EQMS platform very carefully. This is a deep subject and many providers lighten the burden by providing packages to ensure successful validation. There are specifics that, while not demanded in the exact form, are typical in the FDA's vernacular. For example the FDA states "FDA validation guidance sometimes describe user site software validation in terms of installation qualification (IQ), operational qualification (OQ) and performance qualification (PQ)." Most vendors express packages in this way. PQ can be a significant end-user burden.
Typically an EQMS vendor will provide base documentation and support in validation and verification, usually in the form of IQ/OQ packages. Some vendors provide a full service including the test script writing and execution for PQ, but this can and is often completed by the end user. Other basic requirements include functionality like electronic signatures (21CFR:Part11).
The overhead of software validation activity must be appropriately budgeted for in both time and finances. Upgrades are an additional area where the end user must explore the provision of documentation and support from the vendor to eliminate disruption or non-compliance. Validation is an ongoing pursuit with upgrades.
Q. What are the top five elements of QMS you believe should be automated?
A. LNS Research's data tells us that the top five processes currently automated are (in order of adoption);
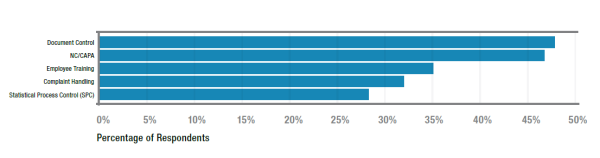
It is anticipated that supplier quality management, risk management, change management and audit management will threaten to break into the top five over the next 12-24 months. It is difficult to paint the list with a priority that is not aligned with the needs and strategic objectives of a specific organization and within the context of their industry, but the top four on this list would likely appear front-of-mind for most.
Q. Any idea on the timeframe to implement an EQMS? I know it depends on many factors such as current state of the QMS, resources, scope and size of enterprise...however, what is your experience?
A. An implementation can range from weeks to many months or longer. There is no simple equation unfortunately, but from an enterprise perspective a module-by-module or process-by-process approach is the one with the best chances of success, with the least risk of going beyond planned implementation timelines. Some vendors are bold enough to guarantee roll-out for an individual module in one month, for example. Others are less bold. Typically, for a multi-module implementation of an EQMS, a large organization should be estimating at least a 5-12 week window per significant module. This is significantly impacted by level of resource and scope, as well as the decision making process in configuration and delivery.
Q. What are the challenges in implementing this type harmonious solution? I can think of cultural changes, integration, cost, ROI, naysayers, etc.
A. All of the challenges listed are valid. A few additional challenges include validation (regulated industries), IT support and maintenance, useability and adoption, continuous improvement of system, and supporting the full suite of processes.