As organizations look to improve their maintenance effectiveness, many have taken the step of identifying critical production assets and collecting actual operational data such as run times and cycle counts on those assets. Often this is done automatically by linking to the programmable logic controller (PLC) or similar level one control element. In other cases, a process data historian or MES or MOM application may link to the process automation equipment and will then serve as the bridge to move that data into the APM environment.
Where neither of these options is available, companies usually fall back to manual data entry but are more likely to not even pursue collecting usage-based data if they can’t get it automatically. But for those organizations that are using usage-based data to help them perform maintenance more effectively, they need to understand the limitations that the approach has as well as the implications it may have as the organization pursues other approaches to asset performance management (APM).
Preventative Maintenance is Periodic Maintenance
Preventative maintenance (PM) is often the first step an organization takes as it seeks to move away from reactive or break-fix maintenance approaches. A classic example of PM is the recommendation you change the batteries in your smoke detector roughly every six months, usually whenever you make the shift to or from daylight savings time. The alternative would be to only change the batteries when the detector fails, however, there is high risk in that approach since most detectors just stop working without any indication that they have stopped.
In an industrial world, PM activities usually revolve around tasks such as inspections, lubrication, filter changes or adjustments such as belt tensioning or bearing preloading. When done at specific time intervals we refer to this as time or calendar-based PM. However, the period or interval does not have to be time-based. Another interval can serve as the period. An example might be changing the oil on your car every 7,500 miles.
In the industrial sector, the periods are usually determined by either run-time or start-stop cycle counts. We refer to this as usage-based PM and the distinct advantage of the approach is that it avoids over-maintenance of assets that are lightly used and accelerates maintenance on assets that are used more intensely than the OEM may have assumed when setting a recommended time-based maintenance interval.
Conditional PM is Not Condition-Based Maintenance
A typical situation that is common in our personal lives is the oil change interval for our cars. Almost every manufacturer specifies an oil change interval not of just 7,500 miles but rather 7,500 miles or 6 months--whichever comes first. They do this because a vehicle driven only short distances every day may never warm up enough to fully drive moisture out of the oil, causing it to deteriorate much sooner than the vehicle will accumulate the mileage. Also, oil that just sits idle can deteriorate as well.
Similar situations exist in industrial environments where lubricants are involved--belts may deteriorate due to exposure not just usage, corrosion may occur or other environmental factors may cause wear and tear on equipment. This either-or approach to setting PM intervals is really conditional PM--that is either condition, time, or usage can determine the PM interval. Users need to understand, though, that conditional PM is not condition-based maintenance.
We sometimes hear our clients refer to this usage-based PM approach as their CBM program. We encourage them to be cautious using this terminology. If management believes that a conditional PM program is CBM, they may expect the types of results that CBM typically delivers in improving reliability and lowering maintenance costs. CBM is predictive maintenance (PdM), and PdM typically delivers more substantial results than PM.
That is not to say some assets can’t benefit from PM. In fact many do and with some cost savings. But the magnitude of those savings and the improvements in reliability are generally not as significant as can be achieved with true CBM in a PdM program. By not referring to conditional PM as CBM or PdM, you will not be setting yourself up for unrealistic expectations.
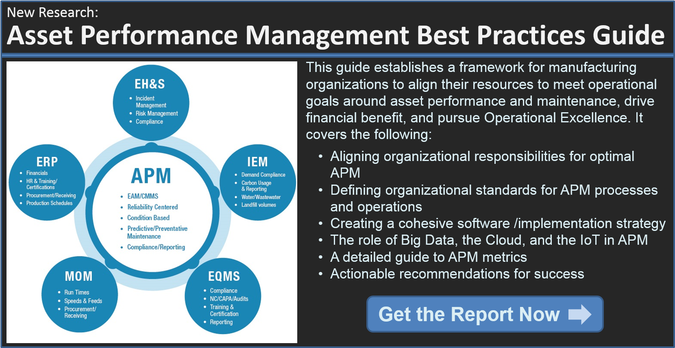