Or is it the other way round? Both batch execution systems (BES) and manufacturing operations management (MOM) systems have been defined by mature Instrument Society of America (ISA) standards. Below we will discuss the voracity of this claim as it demonstrates an interesting dynamic in the market for automation and supervisory control in today’s batch processing industries
Defining Industries
Many vendors of manufacturing hardware and software talk about the “process industry” without specifying more. This leads to a great deal of confusion. In regards to my background, it makes me think of the process industries as petroleum refining, bulk chemicals, all the way down to fine chemicals, and limited industries; such as pharmaceutical active ingredient manufacture. Those who come from a discrete manufacturing regime think of food & beverage (F&B), pharmaceuticals, and many consumer goods as process industries. In studying batch processing, we will keep things simple and use the term “Batch industries” to cover the F&B, consumer goods, pharmaceuticals, and similar industries where part of the manufacturing process is carried out in batch reactors. These reactors produce a quantity (a batch) of intermediate product at a time. Other parts of the process are likely to be more discrete and must be integrated with the batch processes to deliver final packaged product.
What is So Special about Batch Processes?
It is easy to say nothing, but that would be a bit terse. Batch processes could be seen as an irritating block to a perfectly good discrete workflow. However, when you look in more detail at the discrete workflow, you can use batch processing techniques to handle much of it. If we look at a typical pharmaceutical tablet making process, it becomes almost classically batch oriented from start to finish.
The key part to making a tablet is the active ingredient. That will often be made batch by batch. The raw materials are weighed and dispensed automatically into the batch reactor under control of the batch recipe system, and then the batch is processed with little or no human intervention. At the end the batch is delivered into containers, and all batch historical data is included with the electronic batch record (EBR) for that product. The final product is made by weighing and dispensing active and other ingredients required to make the pills, and is passed through a semi-continuous process of tablet making. It is then packed, labelled and serialized, again batch by batch.
When we study the process above, it is clear that batch execution is the main key to correct manufacturing of our tablet. It is information that is critical to knowing what was done. Batch execution processes use information from the recipe and the process in order to run correctly. But it is the information collected as each phase of the batch runs that defines the EBR and hence the perceived and demonstrable compliance of the batch. In today’s regulated environment, batch systems will be validated quite separately from EBR systems and perhaps MOM solutions, as well. In future posts we will look into more detail about the integrated solution, and where this is likely to go as operational technology is modernized and influenced by the Internet of Things (IoT) thinking.
Standards Are There to be Used
We introduced above the ISA-88 and ISA-95 standards for batch and MOM respectively. We also mentioned that vendors make bold claims about their use of these standards. Both standards define hierarchies of hardware and or functionality intended to make understanding and implementing systems easier. The Batch standard is particularly useful as it defines hardware from enterprise down to processing units, and then maps hierarchical batch recipes onto that hardware model. Almost all batch systems implemented at PLC level and below follow this method. It allows for a lot of reuse of low level recipe phases from one recipe to another, and easy to understand recipe structures.
Vendors of MOM systems have not, on the whole, been quite as detailed in following the ISA-95 standard. The standard describes a multi-level hierarchy from plant equipment at level zero to enterprise governance at level five. Lever three is the MOM layer and the functions, such as production execution, quality management, plant scheduling, and data tracking are all described in the standard as are interfaces between these functions. However, most MOM systems today are monolithic and encompass some or all level three function in a single solution. They do, to a greater or lesser extent, implement standard interfaces between level three and four, but that is difficult to standardize completely as there are so many level four systems with which to communicate. As IoT technology and standards emerge, we expect this situation to change quite rapidly as individual functionality.
Do the ISA Standards Have a Future?
Absolutely! A huge amount of work has been done by ISA and related organizations to define batch and manufacturing execution systems in a way that is easy to understand. The standards enable manufacturers to have a baseline from which to start their journeys in both fields. The details of the standards, especially when interfacing between different levels, have helped many implementation efforts.
It is clear that, at least in MOM, the rigid hierarchy and interfaces defined in the standard will gradually be replaced by IIoT based platforms and architectures. We expect much of the ISA breakdown of functionality to remain similar while possibly going further into smaller functional blocks, but that is some way off. The success of the ISA88 batch standard will continue – one could argue that ISA-88 is the rich uncle rather than the poor relation of ISA-95; The richness provided by the physical, process and procedural models of batch execution will continue to be of great benefit even if control strategies change somewhat as the factory floor becomes ever more connected.
Gain a year of free access to new research in our IoT Research Library by completing a survey.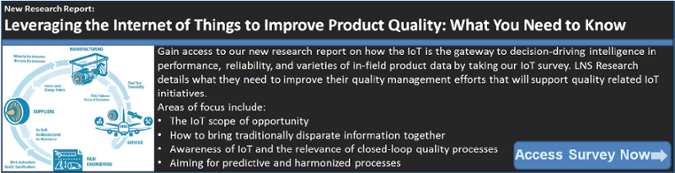