The traditional leadership model simply isn’t adequate for the constantly evolving business world. Industrial organizations recognize that the Future of Industrial Work (FOIW) demands a more inclusive and empowering leadership approach. Global Manufacturing VPs and Chief Operating Officers (COO) are finding servant leadership is emerging as the foundation to enable significantly improved operational performance.
Manufacturing Leaders must build an agile, adaptable workforce ready to face the persistent onslaught of challenges. On average, FOIW Leaders who embrace a servant leadership approach perform nearly 10% better across all KPIs. LNS Research has found that shedding the traditional leadership approach is key to enabling these step change results.
Key Performance Indicators (KPI)
|
FOIW Leaders
|
FOIW Followers
|
FOIW Leaders- Followers
|
First Pass Yield
|
93%
|
74%
|
19%
|
Forecasting accuracy
|
84%
|
70%
|
14%
|
Profit margin
|
70%
|
57%
|
13%
|
Inventory turnover
|
79%
|
66%
|
13%
|
Capacity utilization
|
82%
|
73%
|
9%
|
Table 1: FOIW Leaders are unlocking step change improvements
In this blog, I will unpack how FOIW Leaders are reaching breakthroughs in product design, unlocking significant process optimization, and transforming problem-solving. Organizations can replicate this success by leveraging the actionable insights case studies have uncovered.
Why Traditional Leadership Styles are Failing
The newer generation of workers demands more autonomy and has a very low tolerance for unsafe conditions. Industrials can no longer drag their feet until a big event, whether internal or external, forces change. Recent events have caused detrimental impacts to highlight and underscore the need for manufacturers to shift to a more empowering and inclusive leadership style.
Traditional leadership styles in manufacturing are often more autocratic, with a top-down approach directing work along the way. Shifting to an employee-centric lifecycle is critical to developing a future-proof workforce, transforming performance, and enabling more sustainable operations. FOIW Leaders are leveraging the servant leadership approach to unlock step change operational improvements and better attract, train, and retain employees.
Organizations focused on empowering the workforce are much better positioned to navigate the increased complexities of the business landscape and adapt to changing conditions. Shifting to an employee-centric lifestyle enhances the total employee experience and enables manufacturers to achieve the coveted employer-of-choice status. Shedding failing leadership practices allows manufacturers to reimagine the traditional employee lifecycle and create a culture that prioritizes meeting frontline employees where they are.
Servant Leadership Delivers Business Value
Servant leadership is a philosophy in which the leader’s main purpose is to serve, putting others first and helping them develop and achieve peak performance. Executives who embed servant leadership practices into the organization's culture achieve safer, more productive, and more reliable operations. In addition to improved operational KPIs, FOIW Leaders are 5.5 times more likely to exceed EHS performance and nearly three times more likely to exceed employee recruitment expectations.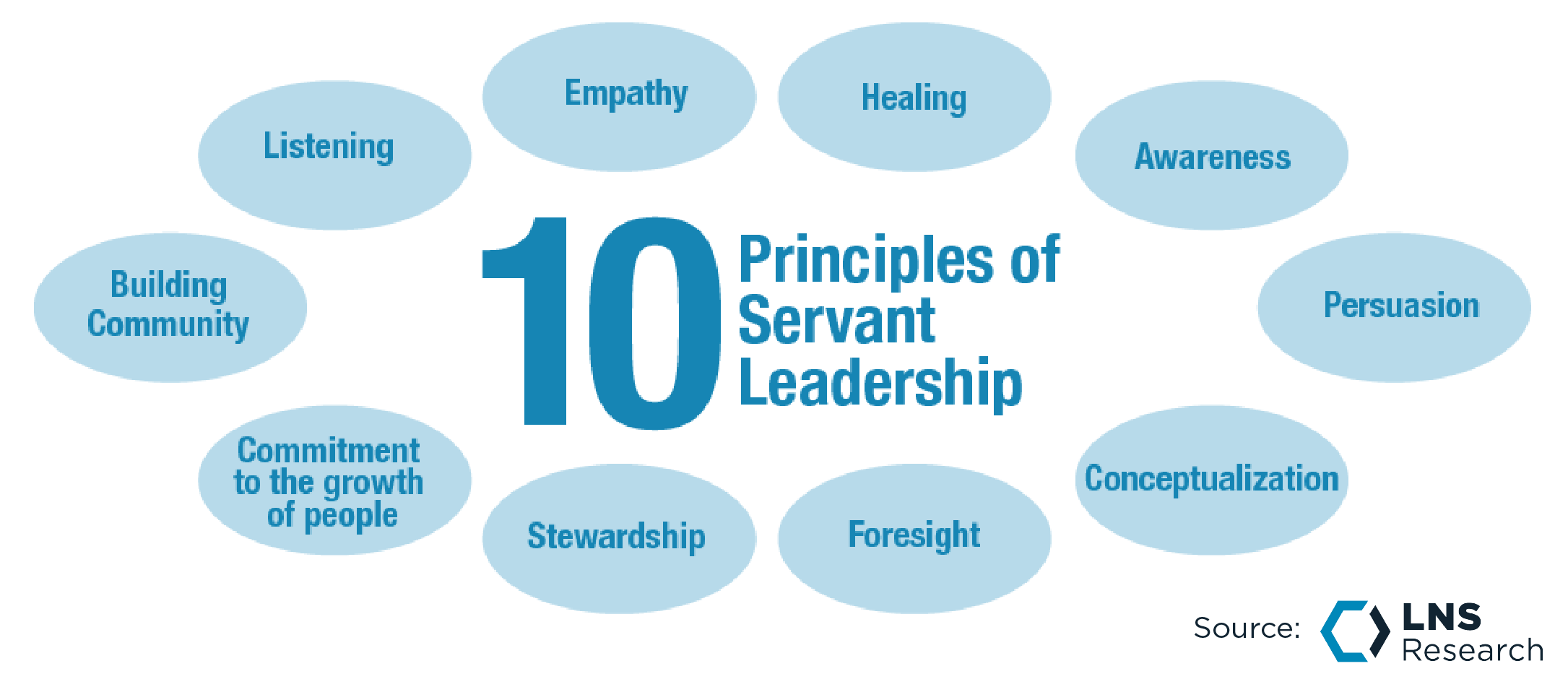
Leaders should see the principles of servant leadership and this approach as a crucial component of their industrial operations strategy. By focusing on creating a psychologically safe work environment to ensure the overall well-being of employees, leaders can reduce unplanned events, better assure compliance, and enhance overall safety performance. To transition from command and control to servant leadership, leaders must consistently reinforce expectations for servant leadership behaviors from the highest levels of leadership and throughout the organization.
Servant leadership is imperative to facilitate transformation across manufacturing organizations and enable the Virtual Operations Center concept. A Virtual Operations Center digitally connects employees to a network of knowledge, expertise, and resources by allowing cross-functional collaboration (e.g., manufacturing, IT, OT, management systems, business teams) from any location to support seamless execution. A culture of support and trust, with the frontline seen as the subject matter experts, ensures employees feel efforts deliver support and career growth rather than just creating another management system to maintain or many more layers of complexity.
Creating an Empowered Workforce with Servant Leadership
Servant leadership is pivotal in creating a manufacturing environment committed to optimizing business processes, implementing new technologies, and quickly responding to market shifts. Supporting the newer generation of workers requires a new operating model that reduces the need to replicate expertise within each manufacturing facility. Manufacturers must recognize that servant leadership practices are critical to ensuring employees see the Virtual Operations Center concept as an enabler to solve problems and support operations rather than exert top-down control.
By embedding servant leadership practices across the organization, manufacturing leaders have significantly enhanced efficiency, effectiveness, employee engagement, and satisfaction. To achieve this same level of success, focus on these best practices:
-
Champion servant leadership from all levels of the organization for the approach to take root and flourish. COOs must actively incorporate principles into the organization's operational framework with a more holistic FOIW strategy. Ensure actions consistently demonstrate respect for all people and an unwavering commitment to empowering others, fostering a culture of safety and trust, and leading by example in all aspects of organizational life.
-
Boost continuous improvement efforts and bolster lean manufacturing principles with servant leadership principles to enable growth and innovation. Moving toward a more autonomous plant can eliminate non-value-added work, improve the employee experience, and allow the organization to embrace change as an opportunity for growth and innovation. Set organizational expectations for leaders to constantly seek feedback, learn from mistakes, and empower employees to contribute to process enhancements to drive collaboration and continuous improvement.
-
Model the actions needed to empower every team member to contribute to their fullest potential and create a culture of support and collaboration. Leaders should roll up their sleeves and actively engage with frontline employees to embed servant leadership practices, a prerequisite for Virtual Operations Centers. A “boots on the ground” approach allows Global Manufacturing VPs and COOs to model behaviors of authenticity and humility in everyday actions.
-
Build the Virtual Operations Center foundation by defining operational architecture and prioritizing human-centric technology. The pressing need is to provide proactive, real-time, on-demand, and flexible process support from virtually anywhere. The LNS Research IX Reference Architecture and today’s more modular and flexible approaches enable manufacturers to move toward more autonomous processes, which are essential for meeting the demands and overcoming the challenges of tomorrow, whatever they may be.
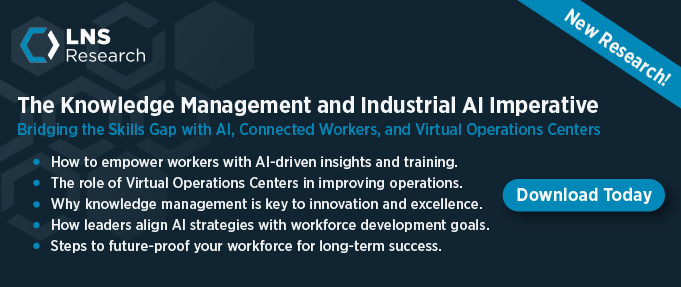