In the race to dominate the industrial landscape, digital tools aren’t optional—but key for survival. Industrial Transformation Leaders have already given the workforce toolbox an extreme makeover and achieved far superior results compared to Followers.
LNS Research has long proven that Connected Frontline Workforce (CFW) applications unlock a whole new level of support for the shop floor. This blog explains how Industrial Transformation Leaders can empower employees to improve their work by combining emerging technologies, such as AI and Advanced Industrial Analytics (AIA), to build a fully engaged frontline workforce.
The Rapid Adoption of Connected Frontline Workforce Initiatives
In 2023, 54% of manufacturers implemented or were piloting Connected Frontline Workforce (CFW) initiatives to catalyze continuous improvement efforts (Figure 1). Compared to 2020, nearly 50% of manufacturers with no plans to implement have since begun to budget and/or pilot CFW initiatives. With almost 80% of Industrial Transformation Leaders having already implemented and/or piloting CFW initiatives, Global Heads of Operations facing rising costs across operations are reevaluating CFW initiatives to transform frontline operations.%20Initiative%20Adoption-1.png?width=522&height=401&name=Connected%20Frontline%20Workforce%20(CFW)%20Initiative%20Adoption-1.png)
Figure 1: CFW Adoption has significantly increased since 2020
when nearly 30% of manufacturers had no plans for an initiative
Manufacturing budgets are tight, and only the best business cases are funded. The biggest challenge manufacturing leaders face is defining a strategy that can secure buy-in from the C-suite, the frontlines, and IT. LNS Research sees integrating CFW and Operational Excellence (OpEx) initiatives to “complete the last mile” as a key enabler.
Catalyze Continuous Improvement with Frontline Engagement
Manufacturers have long promoted continuous improvement as a relentless pursuit of excellence. While the efforts are meant to drive innovation, reduce costs, and increase customer satisfaction, many newer employees who haven’t grown up in this culture struggle to survive in a tumultuous, fast-changing operating environment. Unfortunately, the capacity for continuous improvement efforts often plays second or third fiddle when processes or cost structures are unstable (Figure 2).%20Program%20Drivers.png?width=629&height=312&name=Top%20Industrial%20Transformation%20(IX)%20Program%20Drivers.png)
Figure 2: Cost pressures can often prevent manufacturers from
executing the initiatives that are proven to deliver long-term value
While continuous improvement efforts are a proven means to reduce costs and variability and improve profitability, practices need to be adapted for a newer workforce whose tenure will likely be closer to three years than 30. Industrial Transformation Leaders are shifting the focus of continuous improvement toward an OpEx approach that holistically enhances processes, products, and services to eliminate waste, increase efficiency, and ensure high quality. This approach encourages a culture of constant evaluation and refinement rather than simply seeking areas to reduce costs or “trim the fat.”
Manufacturers can significantly catalyze continuous improvement efforts by engaging employees at all levels. CFW applications can be a core enabler to Operational Excellence through the use of robust analytics capabilities, allowing for real-time monitoring and feedback to ensure improvement opportunities are data-driven and impactful.
Modernizing Continuous Improvement by Integrating AI, Analytics, & CFW Applications
Historically, continuous improvement methodologies rely on structured processes and employee engagement to identify and implement incremental improvements. As many are looking to revive ongoing continuous improvement efforts, the adoption of Advanced Industrial Analytics (AIA) has revolutionized manufacturing with deeper insights and more precise control over operations.
With the newer workforce craving, and even demanding, emerging technologies in the workplace, most find CFW applications are being readily adopted across the frontline and significantly improving the employee experience. Industrial Transformation Leaders have proven that CFW applications are critical for leveraging AI and AIA for better, faster front-line decision-making to drive dramatic continuous improvement results across OEE, COGS, overall corporate revenue, and more (Figure 3).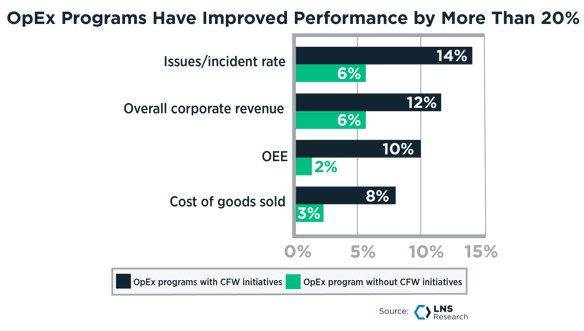
Figure 3: Manufacturers' OpEx programs with implemented CFW initiatives
dramatically outperform those without CFW initiatives
With many manufacturers having earmarked funds for AI investments, there is no better time to integrate AI, Analytics, and CFW initiatives to create a business case that aligns drivers from the top down and bottom up. By creating a frontline toolbox of technologies that include CFW solutions, Analytics, and AI, manufacturers can rapidly gain adoption of modernized continuous improvement efforts.
How Manufacturing Leaders Can Achieve Dramatic Results
Most manufacturers profess a “bottoms-up” frontline focus, but few policy and procedure-based systems reach the shop floor workers and empower them to improve their work. The aftereffects of significant labor shortages and supply chain disruptions from COVID require manufacturers to adapt faster as newer, less experienced employees fill roles traditionally occupied by those with more tenure. Where we see the biggest bang for the buck is deploying AI and Advanced Industrial Analytics to the frontline through user-persona-specific CFW applications to drastically improve the results of Future of Industrial Work (FOIW) and Operational Excellence (OpEx) initiatives.%20Applications.png?width=727&height=450&name=2025%20Connected%20Frontline%20Workforce%20(CFW)%20Applications.png)
The good news is that Industrial Transformation Leaders are breathing new life into continuous improvement efforts and unlocking significant operational improvements by integrating advanced analytics, AI, and CFW applications with OpEx. To achieve the same improvements and better prepare the workforce for future advancements, manufacturers must follow these proven best practices:
-
-
-
Develop a holistic CFW strategy for the Future of Industrial Work. Poorly implemented CFW technology results in costly wasted resources, failure to unlock business value, and loss of competitive advantage in the marketplace. Focus on digitally enabling the workforce rather than executing a technology-centric strategy, which is significantly more likely to fail.
-
Deploy pre-built persona-first use cases offered by CFW platforms where it makes sense. Manufacturers always think their problem is unique and special, requiring a customized solution. In some cases, that may be very true. However, many CFW solutions offer pre-built use cases that enable frontline workers to use low-code/no-code technology to create custom tools and quickly accelerate the return on investment.
-
Simplify and streamline existing management systems with AI and Advanced Industrial Analytics. Don’t just focus on digitizing what’s already been created on the frontlines. Help employees automate non-value-added work by leveraging the power of AIA to identify the biggest pain points to tackle.
-
Scale AIA efforts to support the frontline workforce better. Which is preferred, connected workers or a connected workforce? Don’t ignore those on the frontlines of supporting the frontlines. Supervisors, unit managers, engineers, and many more have the most direct impact on those actually running operations. Establish feedback mechanisms to allow for constant evaluation and refinement of improvement initiatives. Embedding feedback loops within CFW applications can help ensure that newer techniques remain relevant and impactful.
-
Ensure Operational Excellence programs are fully engaging with the frontline workforce. Ensure frontline employees receive regular training to help them stay updated on the latest continuous improvement techniques and technologies. More importantly, it offers opportunities to practice these skills with newer OpEx tools.
Industrial Transformation Leaders recognize that these efforts are part of the bigger Future of Industrial Work roadmap, which aims to drive meaningful improvements across the board.
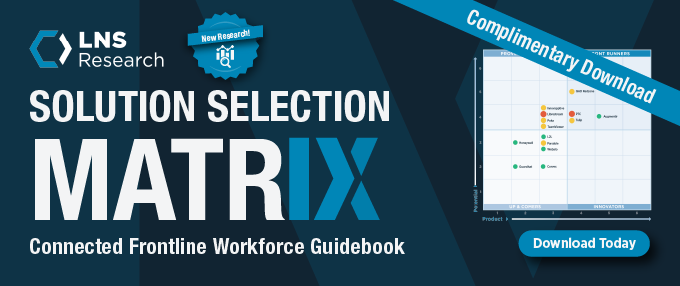