On Thursday, October 25, LNS Research hosted the webcast, “The Road from Metrics to Analytics for Mid-Sized Manufacturers.” The webcast explored data from the 2018 “Analytics That Matter” survey with a focus on finding metrics used by high-performing companies for financial operations, manufacturing operations, and supply chain management. The webcast also focused on how companies can make a move from metrics to advanced industrial analytics, the best practices for building use cases for analytics, and the importance of an Operational Architecture to support industrial analytics.
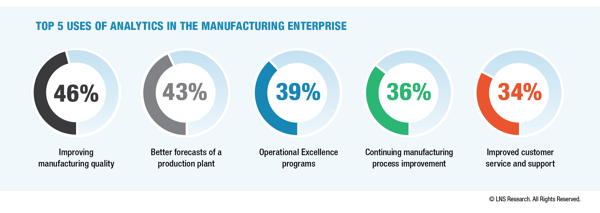
Q1: What systems are people using to track manufacturing metrics and industrial analytics?
A1: Most metric tracking is started manually – data is captured somewhere on the shop floor, entered into a spreadsheet with graphs and is presented to management. However, over the years, there has been a wide range of products introduced to capture data and power metrics reporting, including data historians, enterprise manufacturing intelligence (EMI) systems, and more – in addition to homegrown solutions that tie into a traditional BI (Business Intelligence) tool for great visual presentation of data. More recently, we’ve been seeing advanced analytics solutions that range from “plug and play” remote monitoring to full-blown data science platforms and toolkits that require a data scientist to configure and run.
Remember, the move to analytics doesn’t require a dedicated analytics platform. Take a look at recent releases of manufacturing ERP, MES, and other factory platforms – they’ll surprise you with their analytics capabilities, and you may already have these capabilities in-house.
Q2: Can you explain what you mean by digital technology? Is it specific to Industrial Internet of Things (IIoT) or Industrial Transformation?
A2: In the world of operations technology (OT) – as opposed to IT – there is still a significant presence of analog technology: Andon systems, for example. We talk about digital technology in the OT world specifically to mean software and related tech.
Q3: What is Pilot Purgatory? Moreover, how do we avoid it?
A3: Pilot Purgatory was coined in the industry a few years ago to describe the situation where a company starts a new technology pilot project that never ends - and never scales. At LNS we’ve seen this multiple time: a plant puts a plan in place to solve a specific problem, or in conjunction with a new line or cell installation without building a use case in advance or making any significant changes to their enterprise data model. Not surprisingly, when analytics run on such models, the pilots usually don’t provide meaningful results and meet a dead-end.
There are three steps to avoid purgatory with new pilots:
- Figure out what you’re trying to do. Build a use case and make sure you define what a successful outcome looks like
- Work with whoever is leading your Industrial Transformation initiative/IIoT/Industry 4.0 or factory of the future program, making sure the pilot you’re planning fits into your company’s plan for its future
- Define your data model and work within your agreed-upon Operational Architecture
Q4: Which people or departments are driving these initiatives? (quality, operations, manufacturing, other)
A4: At LNS, we’ve been closely watching the emergence of a hybrid IT-OT role – someone from the manufacturing operations world who is specifically charged with looking at how new and emerging technologies can improve operations, quality, and even product design. At larger companies, there’s usually a cross-functional team to support these goals, and they’re called something like Factory of the Future, or IIoT Roadmap, or Industry 4.0 Planning – or even merely the Advanced Manufacturing Team. These are the teams that we see leading the charge on advanced industrial analytics.
Q5: How do metrics and analytics relate to IIoT and Industrial Transformation?
A5: Metrics are usually part of a Continuous Improvement (CI) initiative, which is a part of an Operational Excellence team. These terms have been around for a while and are not explicitly related to IIoT or Industrial Transformation. However, these internal programs can form the building blocks for successful Industrial Transformation programs. Industrial analytics, on the other hand, requires the use of advanced technologies such as data lakes, M2M communications, smart machines, Edge devices, and other Big Data and industrial technologies. As such, analytics are usually considered an integral component of the Industrial IoT and should be a significant component of Industrial Transformation.