In Part 1 of this series we gave a detailed explanation of how LNS Research thinks the OEE Formula is best applied to a given asset or production line to both maximize local production efficiency as well as overall supply chain performance. In Part 2 we will go through a fictional example to start applying real numbers to all the OEE Formula terms mentioned previously. Hopefully this will help answer any questions you may have to using our OEE formula in your own plant.
Applying the OEE Formula
To start let's review the complete OEE Formula. Remember, overall equipment effectivess should be thought of as a composite metric that measures a particular assets uptime, production efficiency, and quality. It is best represented as below:
OEE = Availability x Efficiency x Quality
Now let's jump into each term starting with Availability. Based on the LNS Research OEE definition, availability is a measure of how often a particular asset is is running when there is a customer order or safety stock level that requires fulfillment. Based on this understanding we have the following formula:
Availability = Asset Uptime / Asset Scheduled Production Time
Now with this formula established, we can look at some numbers. In our fictional company, let's look at yesterday's performance on Work Center 1, WC1 for short, as our example. WC1 only makes one product, WidgetA, and there is currently a customer backlog for 1000 for WidgetA. WC1 can produce a theoretical maximum of 10 WidgetA/hour based on engineering's best estimate. This means WC1 has been at capacity for the past 24 hours and we will use 24 hours as our Asset Scheduled Production Time. For Asset Uptime we should look at how long WC1 was running. Unfortunately, it wasn't as good a day as we had hoped for. We had a scheduled .5 hours of down time for cleaning, another .5 hours for preventive maintenance, and another .5 hours of start and stop down time for filler head jams. This totaled 1.5 hours of down time or 22.5 hours of uptime. Plugging this into the formula we get:
Avialabiltiy = 22.5 / 24 = .9375
Now let's look at efficiency. As we discussed in the last post, efficiency is a measure of how well an asset is performing while it is operational. Based on this understanding we get the following formula:
Efficiency = Total amount of product produced / (Time asset was available * Theoretical maximum production rate of asset)
We already mentioned that WC1 has a theoretical maximum of 10 WidgetA/hour production rate. Fortunately for us, when we were running yesterday the operators were doing a good job and got the production rate very close to the theoretical maximum. For yesterday's production run, WC1 produced 220 WidgetA. Plugging this into the efficiency formula, we find the following:
Efficiency = 220 / (22.5 *10) = .9778
Now let's look at quality. As discussed previously, quality in the LNS Research version of the OEE Formula, can be understood as the percentage of product produced the first time to quality specification. Based on this understanding we get the following formula:
Quality = Total products achieving quality specifications first time / Total products produced
Unfortunately, it looks like WC1 operators may have been sacrificing quality while trying to make up for last downtime with WC1 running so close to its theoretical maximum. There were a lot of errors that required product to be funneled to a rework line and other product that was sent straight to scrap. When the day was over, of the 220 WidgetA that were produced, only 190 hit quality specifications the first time. Plugging this into the formula we find the following:
Quality = 190 / 220 = .8636
Not very good on the quality side. But if we put this all together in the complete OEE Formula, we find it wasn't a very bad day.
OEE = .9375 * .9778 * .8636 = .7916 = 79%
What Does this OEE Example Mean?
Obviously this was a very simplistic example but even in such a simple example it becomes clear that the OEE Formula can be used to tell a story. In the above example, it looks like operators tried to make up for lost down time by pushing WC1 to the brink of capacity and ended up taking a quality hit. Although it wasn't World Class performance, 79% OEE is still a decent run for many industries.
If you would like to read more on the topic of quality management, please click the button below to become a part of our community and gain access to our Quality Management Systems Research Library. 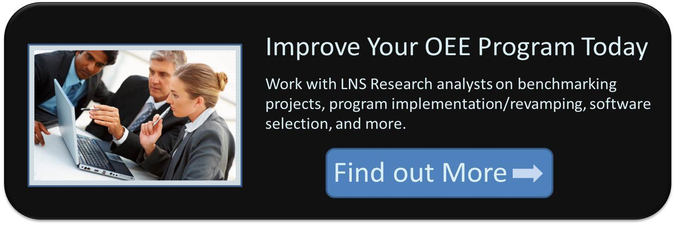