What’s interesting about the current manufacturing environment is the increased weight that executives are putting on collaboration. Not to say that group efforts weren’t a focal point in the past, but it’s being leveraged quite differently today. While developing information and processes has always been important, it wasn’t until the convergence of IT and manufacturing software that market leading organizations began taking it to the next level. A perfect example: Enterprise Bill of Process (eBOP).
With increasingly capable IT infrastructures, the Bill of Process (BOP), a best practices template for production, is becoming a global consideration in Manufacturing Operations Management (MOM) and Product Lifecycle Management (PLM). The resulting eBOP is creating a place for cross-functional teams to share information and collaborate in ways that weren’t possible before.
In this blog, we’ll look into the shift toward process-centric management of workflows across the enterprise. Specifically, we will discuss eBOP, and its similarities to taking a Business Process Management (BPM) approach on the shop floor.
What is a Bill of Process (BOP)?
A product idea is first visualized with an engineering design, followed by the creation of a Bill of Materials (BOM). The BOM is a list of parts and materials needed to make a product, and, without it, manufacturing would be impossible. But the BOM is only part of the product equation. It shows “what” to make, not “how” to manufacture it, leaving the rest up to the BOP.
The BOP is comprised of detailed plans explaining the manufacturing processes for a particular product. Within these plans resides in-depth information on machinery, plant resources, equipment layout, configurations, tools, and instructions. Traditionally, companies with many plants and processes may have only had informal BOPs. If there were any changes, which needed to be communicated to the rest of the enterprise, it was typical for the process to take a long time. The lack of efficiency, scalability, and visibility in this methodology can be seen easily.
Progressive manufacturers are converging IT capabilities with BOP, allowing processes to be communicated and collaborated on at a global level. With eBOP, engineers or line workers, for instance, may develop a way to eliminate a failure mode, then quickly view which plants and products are using the same processes. If decided that this new process should be the best practice, any overlap can not only be communicated, but changed immediately in an eBOP application to avoid further issues.
Examples of PLM vendors with capabilities in this area include eBOP as part of the Siemens PLM Teamcenter platform, Manufacturing Process Management by PTC, and Process Engineer by Dassault Systemes.
Similarities with Business Process Management (BPM)
In departments such as HR, accounting, and finance, BPM has traditionally been used as a way to develop, monitor, and optimize business procsseses at a corporate IT level. Only recently has it been making its way down to the shop floor. Like eBOP, BPM is now used for increasing efficiency with visibility and communication in MOM and PLM. BPM applications give users the opportunity to manage products from the initial idea through well after production. Cross-functional collaboration is used from start to finish, with competencies such as design, modeling, execution, monitoring, and optimization. One major benefit of BPM is that both design and production are coupled in one application, mitigating the costly need to integrate disparate engineering and manufacturing software.
A staple of BPM is the promotion of continuous improvement. Applications allow companies to revisit products and processes to optimize efficiency with analytics. Since the development of BOM and BOP is done on a global platform and then monitored throughout production, users can quickly define and communicate best practices that may affect other plants. Several notable examples of BPM applications in the market today include Sketla by Invensys, FlexNet by Apriso, Proficy Workflow by GE Intelligent Platforms, and Catalyst xM by Savigent.
Collaborative Approaches to MOM and PLM
Both eBOP and BPM are groundbreaking in terms of immediacy in global MOM and PLM collaboration. Since companies are beginning to implement and integrate applications across the enterprise, operational hierarchies, which may have conventionally been viewed as bottlenecks, can now easily be bypassed. These applications offer the ability to make an addition to a process, standardize it for global use, and share it to the network. Other engineers or managers can then further validate or add to these processes at their plants.
The introduction of diverse perspectives into any conversation creates an opportunity for innovation. More often than not, new ideas arise when people with different backgrounds come together to work toward a solution. This concept can be directly translated to the global approach to MOM and PLM. With eBOP and BPM acting as a platform for collaboration, people who normally would never have had the opportunity to communicate ideas are working together. As more and more companies get on board with this approach, LNS Research expects to see continued improvements in operational efficiencies in the coming years.
If you would like to read more on the topic of quality management, please click the button below to become a part of our community and gain access to our Quality Management Systems Research Library.
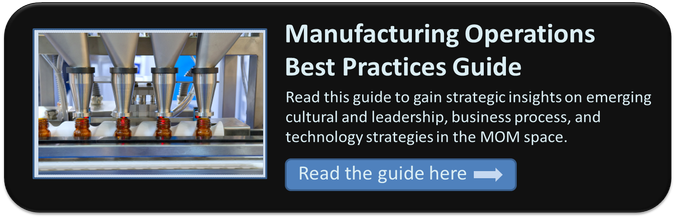