Enterprise Quality Management Software (EQMS) is a solution that touches numerous parts of the value chain—engineering, procurement, manufacturing, supply chain, sales, service and more. Because success for such an implementation depends on delivering both business value and compliance across a broad set of stakeholders, it can be a great challenge for many organizations.
If you are currently responsible for or are planning to implement an EQMS solution in the near future, the list of five steps below will help you avoid pitfalls and ensure success.
Step 1: Clearly Define Objectives – Understand the goals and objectives of the implementation. It is very important that your objectives include both business benefits and compliance or cost avoidance. Specificity is important in defining business benefits. For example, you may measure the Cost of Quality (Cost of Good Quality + Cost of Poor Quality)and want to reduce it by X%, want your scrap rate to be X% or only need X amount of product on hold in the warehouse based on demand and forecasts. With compliance, objectives to tackle should also be delineated up front—CAPA process is broken or regulatory submissions are taking too long. The point is to evaluate and measure the current status, then set future goals. It is also important to understand requirements that are critical for your operations—specific functionality, scalability, interoperability, technology platform, multi-language needs and so on.
Step 2: Bring Together a Cross-Functional Team Sponsored by Executives – The team should be sponsored by a leader in the company such as the VP of Operations, COO, Chief Risk Officer, etc. It should also involve various roles along the value chain, including quality and IT managers, employees from different lines of business, executives and third party experts. Because this is an enterprise level initiative, executive buy-in and support from functional teams are integral for a smooth EQMS implementation.
Step 3: Focus on Speed to Value – Months and, in some cases, years can easily pass for software implementations to be completed. Focus should be around how quickly you can show value through the implementation without impacting long-term objectives. If it’s taking more than a year to get the software running, it’s taking too long. Start with just a single or a few processes or capabilities, build them out and then extend. NC/CAPA or Supplier Quality are great examples of starting points.
Step 4: Take a Risk-Based Approach – Although it’s not always outwardly apparent, everything we do in Quality Management is about reducing risk. SOPs, HACCP, NC/CAPA, GMP—they all reduce risk. Unfortunately, many companies focus on these individual components, but don’t bring them all together for an understanding of the full risk portfolio. By applying the Risk Management Framework—assess, quantify, prioritize, mitigate—the true value of your quality initiative can be understood, even if adverse events never occur. Make sure you build an integrated process for risk management within the EQMS system, tying quality to risk at an enterprise level. This will help break down silos and increase visibility between departments and processes.
Step 5: Calculate ROI – The financial investment and amount of resources used are far too great to not measure the impact your quality management strategy is having on the business. Unfortunately, many companies measure and forecast the benefits of new software prior to its implementation, then lose sight of evaluating if and how well it’s working. It is critical for long-term success to calculate ROI to measure projects relative to expectations. This helps enable continuous improvement and keeps the cycle moving forward.
Adopting available and emerging EQMS technologies isn’t simply a way of modernizing your manufacturing organization, it’s imperative to stay competitive. The advantages, to name only a few, of increased transparency, standardization, heightened data integrity, automated compliance, CAPA procedures and statistical trending tools directly translate to operational efficiencies that affect the bottom line. Following the above steps will facilitate a successful implementation and will help your organization drive operational and business value.
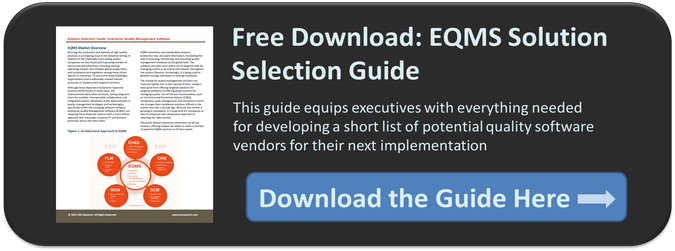
If you would like to read more on the topic of quality management, please click the button below to become a part of our community and gain access to our Quality Management Systems Research Library.