An unfortunate reality in many quality management strategies is the lack of harmony in IT decisions across the enterprise. In the 2012-2013 LNS Research Quality Management Survey, 47% of executives said that a top challenge was having too many disparate quality systems and data sources. As a result, a roadblock to success that most large and distributed companies experience resides in the mountains of unstandardized quality process data that’s never fully leveraged.
Although the use of quality management software has improved the quality of products and processes for organizations large and small, the survey data shows that decisions have been made for quite some time without a long-term vision that supports a globally unified IT architecture. An integrated IT architecture isn’t only necessary for optimizing your ROI on a quality software implementation, it’s also critical for creating a closed loop environment that enables communication and collaboration on quality issues.
In this post, let’s discuss what exactly closed loop quality is and how a globally integrated IT architecture can support it, and highlight several real-life examples of closed loop quality processes.
What is Closed Loop Quality Management?
Closed loop quality management is the concept of creating feedback loops between different functional areas along the value chain. Modern technologies such as Enterprise Quality Management Software (EQMS) are helping organizations to do this by creating a unified information management system that centralizes, streamlines, and standardizes quality processes and data across the enterprise.
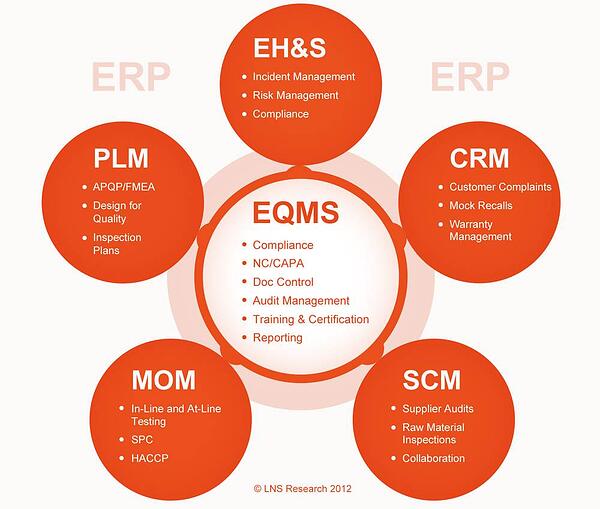
With previously unavailable communication and collaboration capabilities, EQMS processes and functionalities are changing the game for many large and distributed companies. These processes include:
- Non-Conformances/Corrective and Preventive Action
- Document Control
- Compliance/Audit Management
- Supplier Quality Management
- Risk Management
- Statistical Process Control
- Failure Mode and Effects Analysis
- Complaint Handling
- Advanced Product Quality Planning
- Environment, Health, and Safety
- Hazard Analysis & Critical Control Points
- Production Part Approval Process
3 Examples of Closed Loop Quality Processes
Companies have invested large amounts of capital and time in developing a strong set of business process capabilities across the value chain. Although quality may mean different things to different functional areas, it is important to know that data from one stage of the value chain can have a major impact on quality in another.
As a product flows downstream from design through manufacturing and service, organizations should create quality feedback loops to improve processes originating at earlier stages in the value chain. Below, I'll share three examples of how processes can be integrated with one another on a common platform. Market leaders are using the resulting feedback loops between these processes to drive improvements in business performance.
1. Customer Complaint Management and FMEA/CAPA
The earlier a quality issue can be caught, the less of a negative impact it will ultimately have on long-term profitability and brand reputation. In stages of the value chain beyond product development and engineering processes, it is common for nonconformances and quality deviations to emerge. One way EQMS can help to close the quality loop on the design process is by creating a line of communication between customer complaint management and engineering. This can be greatly beneficial to processes such as FMEA and corrective and preventive actions procedures for identifying failure modes and root causes, respectively.
2. Statistical Process Control, Traceability, and Supplier Quality Management
During the manufacturing process, it is typical for companies to use some type of process control methods. Many leading organizations are leveraging SPC software to monitor manufacturing processes for variations. These variations may be identified on the shop floor and then analyzed in conjunction with global traceability and containment as well as supplier quality management capabilities. In many cases, a robust EQMS solution can facilitate the discovery process for and origin of the material causing the variation.
3. Corrective and Preventive Actions and Risk Management
Without the use of EQMS’s automation capabilities, the investigation and resolution processes for CAPA can be a challenge for a large organization. For these companies, it is typical for there to be many outstanding corrective actions. EQMS can help to close the loop on these processes by integrating CAPA with risk management and introduce elements of prioritization and criticality. In this respect, an organization can have a better understanding of enterprise risk while streamlining the resolution of the most pressing root causes of nonconformances.
Closing the Loop with a Unified Information Management System
The LNS Research 2012-2013 Quality Management Survey asked executives several questions that support the case for a globally integrated quality architecture that supports closed loop quality management. By pairing up two of these questions – the first pertaining to the status of closed loop processes and the second overall equipment effectiveness performance – we can see the impact closed loop quality adoption has on OEE performance.
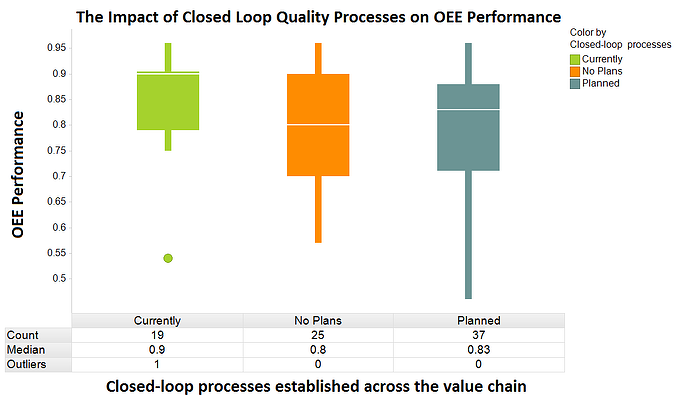
As illustrated in the box plot above, companies that currently have closed loop processes in place across design, manufacturing, and supplier activities perform better in OEE. These companies have a median OEE of 90%, in comparison to 80% and 83% for companies that have no plans and plans for closed loop processes, respectively. What really stands out, though, is the limited variation in OEE performance experienced by companies that have adopted closed loop processes. The performance distribution in the box plot for these organizations is considerably less erratic, likely due to the consistent and accurate information provided by closed loop processes.
Similar to the data points above, other metrics such as the cost of quality and first pass yield are impacted by the ability to deliver closed loop quality processes. To effectively improve the quality of products and processes across the value chain, closed loop quality management should be a key area for investment. Executives considering adding strength to their quality management portfolio should assess current quality capabilities and IT architecture in relation what is available in EQMS solutions today. In many cases, adding several EQMS solutions can open up portals for communication and collaboration that have never been available.
To learn more about this topic, read LNS Research's newest report, Closed Loop Quality: Connecting Engineering, Manufacturing, and Quality.
You might also be interested in:
Enterprise Quality Management Software Solution Selection Guide
Top Integration Points for Enterprise Quality Management Software
Top 3 Strategies for Selecting an EQMS Solution