Times have changed. Think of Henry Ford’s Model T, the first affordable automobile. Although high-tech for its day, it was made of rudimentary parts and components. Today, it’s standard for vehicles to have thousands of parts and components sourced from all over the globe, many of which connect to the tens of millions of computer code lines built into internal systems. The complexities are incomparable.
Because modern products have a lot of variables to account for, there are many opportunities for quality defects before, during, and even after production. It’s easy for the costs associated with these defects to spiral out of control, which is why many organizations measure and work to reduce the cost of quality. Some of the most vital variables in the cost of quality metric are internal failure costs like scrap and rework, and this article aims to provide a comprehensive list for you to include in your calculation.
Understanding Internal Failure Costs
Just like it sounds, an internal failure cost takes place internally, or before a product leaves manufacturing. When people talk about the cost of quality, it’s common for them to focus on these costs, as they take place during the production process and are arguably the easiest to quantify. These costs receive a lot of attention because improvements to them directly translate to improvements in the bottom line. The opposite is also true, which is why it's common for managers to use the P&L statement to find these numbers.
A List of Internal Failure Costs You Need to Watch
- Scrap (cost of product that cannot be reworked or reused)
- Scrap disposal (cost of getting rid of product that cannot be reworked or reused)
- Rework (costs of correcting quality issues on existing product)
- Rework inspection (cost of inspecting a product after rework)
- Additional material procurement (cost to replace defective or missing material)
- Variability in product quality (cost of product give-away and mislabeling)
- Downgrading (cost of lower price point of product with quality issue)
- Supplier rework (costs attributed to supplier defects)
Those are some of the most important variables for calculating internal failure costs. If you measure another variable or have experience with measuring the cost of quality, please remember to share your thoughts in the comments section below.
Don't Forget The Opportunity Costs of Quality
If you’ve ever taken an economics class, one of the first things you learn is that there’s no such thing as a free lunch. Opportunity costs, or the gains you miss out on by taking an alternative action, have to be accounted for in every decision. When it comes to quality, while there’s no such thing as a free lunch, there’s also no such thing as a free production delay due to a quality defect. It’s important that when we discuss internal failure costs, we think also about the opportunity costs of quality.
Below is a list of other cost of quality variables, both good and poor, that can be impacted by internal failure costs. While many of these are harder to quantify and are more productivity-focused, it's clear that they need to be minimized.
- Unplanned downtime (cost of unused production time due to quality failures)
- Retesting processes (costs of testing processes after making changes)
- Management time (costs of management reallocating efforts to resolve quality issue)
- Redesigning Hardware (cost of redesigning hardware that is causing defect)
- Redesigning Software (costs of redesigning software after implementation)
- Redesigning products (cost of changes to product after root cause identification)
- Redesigning quality processes (cost of improving corrective and preventive action or FMEA process to improve root cause
- Schedule disruption (cost of rescheduling operational activities)
- Materials shortages (costs of changing production plans due or missing delivery dates due to quality issues)
The Role of Software in the Cost of Poor Quality Equation
Although internal failure costs listed above relate to the cost of poor quality, it’s important to note that there’s more to the cost of quality equation. On the other side, there’s the cost of good quality, or the cost of efforts taken to prevent poor quality from happening in the first place.
Cost of Good Quality = Cost of Poor Quality + Cost of Good Quality
Investments in the cost of good quality may include automating enterprise quality management software (EQMS) functionalities, such as corrective and preventive actions, audit management, or compliance management. It may also include an investment in real-time data collection software such as statistical process control. There is a wide range of potential solutions for improving first-time quality, and more information can be found in LNS’s EQMS Best Practices Guide.
Calculating the Cost of Quality is Complex
Just by skimming over this list, it’s easy to see that measuring the cost of quality can be complex. Internal failure costs are just part of the equation. Our research paper Measuring the Cost of Quality as a Holistic Business Measurement goes into detail on the benefits and challenges you can expect from measuring the metric and provides some tips for acquiring data on these costs across the enterprise.
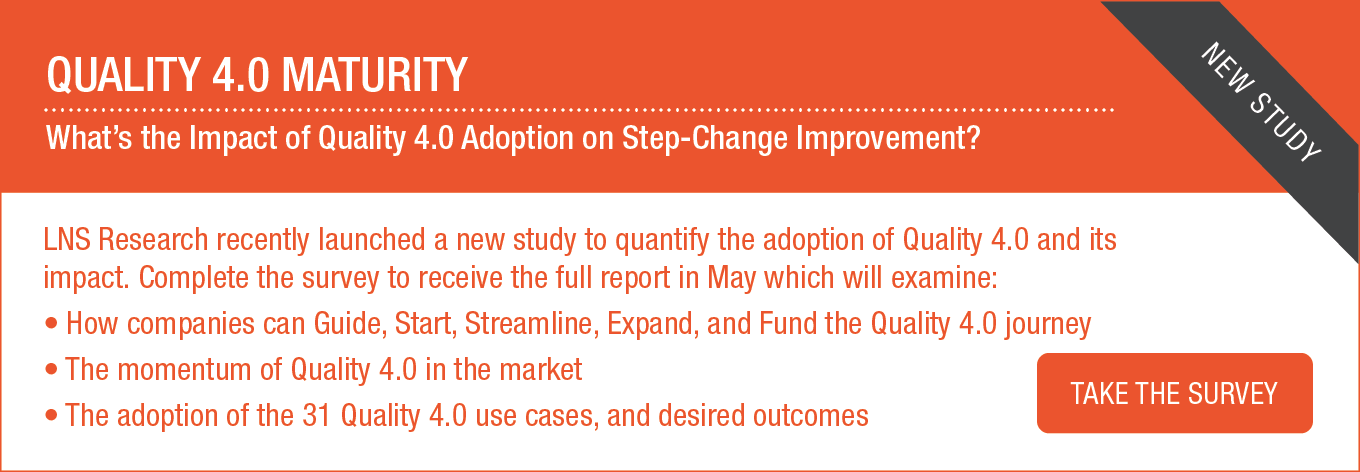