In conjunction with Environmental Leader and Energy Manager Today, yesterday I hosted a webinar entitled "Driving Productivity and Profit with Industrial Energy Management," which presented data and best practices from our IEM research to help attendees understand energy management best practices.
While I had hoped to address more questions live, as is always the case, time prevented me from doing so. In this post we'll answer the top questions from yesterday's event.
At a high level, the webinar discussed the coming changes to global energy and manufacturing industries driven by shifting cost structures around energy, labor, capital, and disruptive technology and innovation paradigms, and how leading companies can best position themselves to face these challenges head-on. I drilled down into several topics, including:
- Driving cultural change across the organization to increase energy awareness
- Managing a portfolio of energy projects to drive optimized business value
- Technology strategies for connecting energy intelligence into manufacturing
- Using energy in preventive and predictive maintenance
Questions & Answers
Q. What kind of risk management tools with respect to energy procurement are available?
A. Energy and manufacturing are inherently risky, with prices subject to volatility and also the variability of actual energy used. Procurement solutions generally have risk modeling and visualization tools to help professionals make the best decisions. Inputs to these models include energy market data, internal data, and demand forecasts.
Q. How does energy procurement drive operations?
A. Before answering this question, I'll start with what we think about when we see energy in the industrial setting. Generally we follow the WAGES definition, which includes Water, Air, Gas, Electricity, and Steam. The procurement of these sources of energy is critical to any operation. Without them, the operation would simply not produce anything. Procuring energy, however, can be a complex task, which is why most modern IEM solutions come with capabilities for risk management, contract management, billing management, peak load management, and demand response.
Q. What kind of dashboards are being used today to improve industrial energy management?
A. There are many different types of dashboards being used today for managing energy. The key to a successful dashboard, is enabling the right automated data collection, presenting that data in a real-time role-based manner, and providing complementary analytical tools for better decision-making.
Q. How much do the five IEM approaches overlap in terms of benefits they provide? To what degree are the benefits cumulative?
A. The 5 approaches mentioned in the webcast--procurement and operations collaboration, balancing peak load shedding with production, procurement data analytics, data collection at the asset level, monitoring and responding to energy events at the asset level--should all be thought of as critical components of a successful energy management initiative.
Q. What are your thoughts on the DOE Superior Energy Performance used in conjunction with ISO 50001?
A. There are many formal programs in existence today supporting energy management, including the two mentioned. Rather than the specific program, most of which are very similar, the critical success factor is how well the company implementing the program takes ownership through building out internal leadership, business process, and supporting technology. For these reasons, LNS recommends that energy management programs should be incorporated into the company's overall operational excellence initiative.
Q. Real-time data and data granularity were mentioned several times. What sort of intervals/granularity are you seeing in your research and experience?
A. It's critical that data granularity and real-time match the need for decision-making and control, which means it will be different in different situations. In a deregulated utilities environment, dynamic pricing may be done in 15 minute increments, which can be considered real-time in this example. In a process automation example, control may be within microseconds, also considered real-time. The key to success is matching the granularity to the needs of the application for improving decision-making, and then making improvements over time as needed.
Q. What are some of the IT solutions that can help companies get the kind of visibility you're talking about? What IT infrastructure do companies need to put in place to make energy management happen?
A. Think of it this way: as energy flows through the organization, data flows back. And there are IEM solutions made for taking that data (often coming from automated data collection technology at the asset level) and contextualizing it with reporting and analytics. It can help you understand energy consumption, and actually drive more efficient use of energy by uncovering areas for improvement. We find that companies taking this step to improve IEM visibility are the ones that make sustainable improvements to energy use and cost over time.
Q. Which KPIs should be commonly used to measure systems' performance?
A. From an energy perspective many companies are measuring overall reduction in energy usage as well as improvements in energy intensity. It is also important to look at this within the context of operations and the supply chain, so many companies are looking at detailed operations metrics, like first pass yield, down time, mean time to failure, as well as higher level metrics like OEE, OTCS, and profitability.
Q. Which new technologies specifically are you referring to for helping with energy management?
A. It's really dependent on which side of IEM you're working with. There's automated data collection technology for energy, and then what we spoke most about yesterday are the next-generation solutions for procurement, use, and reporting. These can be deployed in single instances, but they also be deployed as an enterprise suite of functionality.
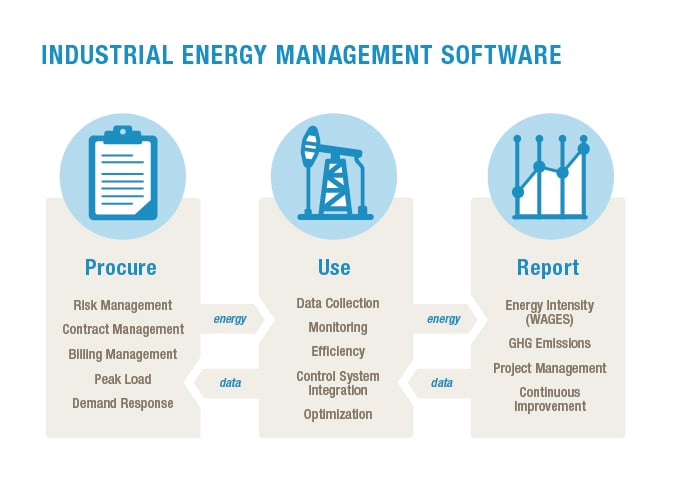
Q. Which industries do you see as most responsive to energy efficiency ideas?
A. Some of the leading industries today making these investments include: food and beverage, consumer packaged goods, automotive, and mining. It is also important to note that many of the process industries have already been focused on these issues for much longer and are probably ahead of the curve compared to the industries mentioned.
Q. Can you provide a few example of how energy management can drive "immediate" improvements versus long-term ones?
A. We often talk about the low-hanging fruit improvements, or those that are simple enough to fix with or without minimal IEM monitoring technology. These may include fixing lighting issues in a warehouse or a leak somewhere in your compressed air system. Low-hanging fruit improvements can be fixed, but they generally cycle back, since lights will inevitably become less efficient and leaks will inevitably happen again.
The longer-term, sustainable improvements are the ones we can gather from next-generation IEM software. Examples may include putting energy on the bill of materials and associating a specific cost to it like any other part or component, or optimizing production with real-time energy costing information.
If you have any additional questions, please feel free to ask them in the comments section below or tweet to me @m_littlefield, and I'll do my best to answer them. Also, if you're interested in viewing these slides, follow the link below.