You would be hard-pressed to find a manufacturing operations professional today that doesn’t have the impact of new technologies on their mind. And with good reason—Manufacturing Operations Management (MOM) software, particularly the newest-generation offerings are having a marked effect on production—through things like improved data and analytics, better visibility by role, increased automation and integration with other enterprise IT—and consequently, helping companies better visualize and achieve goals and respond to operational and business challenges.
But with the excitement around IT advancements we can sometimes forget more foundational and time-tested foundations of success. These are people and culture related, of course. While IT plays a key role in sustaining operational success, ultimately, decision-making is still a human responsibility, leaving leadership and employees in the critical roles they have always inhabited. In this post, we’ll discuss the importance of leadership and employee engagement in achieving Operational Excellence goals and give a step-by-step guide for success.
Top Operational Challenges: Still People Related
Before getting into the specifics of building well-led, engaged teams, let’s take a quick look at what some of the top operational challenges are that companies face today. According to LNS Research’s 2013-2014 MOM survey, the top challenge is still breaking down silos of organizations and departments to foster collaboration—at 26% of responses. At 25%, the next highest challenge is in extracting the required data and information out of the many disparate systems and database across plants and the enterprise. IT is key in enabling this capability, but effective governance, involvement, processes and communication are also needed—both in getting initiatives off the ground, and making effective use of the data once it’s available.
In aligning people, processes, and technology resources, experience has shown LNS Research that people and leadership issues are an area that should be addressed as a first priority. Once effectively attended to, the effects ripple outward, facilitating the ability to build deeper organizational capabilities that use proven process methodologies to make continuous improvements. This must all be taken into consideration before software solutions can effectively sustain and improve results.
Organizing for Maximized Employee Engagement
Before a well-oiled and engaged team can carry out continuous improvement initiatives, the direction of the company must be conceived, established, and communicated to the workforce. A key component of this is achieving employee buy-in. As boots on the ground carrying out physical tasks and decisions, they need to understand and believe that any change in the standard operating procedure is going to be worth their efforts. In gaining this buy-in, there are a number of key aspects leadership needs to convey to win the support of the workforce, including:
- Accountability
- Openness to employee input
- An emphasis on the importance of the initiative, so it is not seen as “flavor of the month”
- Active engagement
- Patience
- Assistance and mentorship
- Incentivization
Strategically, one of the industry best practices that LNS Research sees for achieving these goals is to undertake a strategic decomposition/goal alignment process, which involves the following steps:
1.) Understand and Articulate Strategy: Have a clear and universally understood manufacturing strategy that is in support of the corporate business strategy
2.) Translate Strategy into Specific Goals: Turn that strategy into specific goals for business groups and associated supply chains, as well as plants, units, and production lines
3.) Map Goals and Specific Measures for Success: Use a cross-functional team to map each detailed translation across the enterprise
4.) Determine Key Performance Indicators: Develop a set of manufacturing KPIs to measure progress toward your goals
5.) Establish Communication Procedures for KPIs: Make sure the right information is getting to the right people in a timely manner
6.) Set Processes for How to Act on KPI Information: Determine best practices for individuals from the shop to top floor to interact with KPIs
7.) Match Performance Incentives to Aligned Goals: Reinforce the effectiveness of measuring KPIs by incentivizing progress
Depending on organizational resources and maturity, some companies are able to undertake these cultural initiatives autonomously, and some find third-party help beneficial in building these leadership and employee engagement foundations.
Achieving Operational Excellence Results
The steps outlined above should of course be buttressed by regular communication to aid in transition, and are optimized with the introduction of supporting software technology. The research data shows that having process and software capabilities built upon a foundation of well-formed teams has a significant effect on achieving operational goals. As the chart below shows, companies with all of these capabilities in place are between 1.6 and 2.7 times more capable of achieving their production management goals.
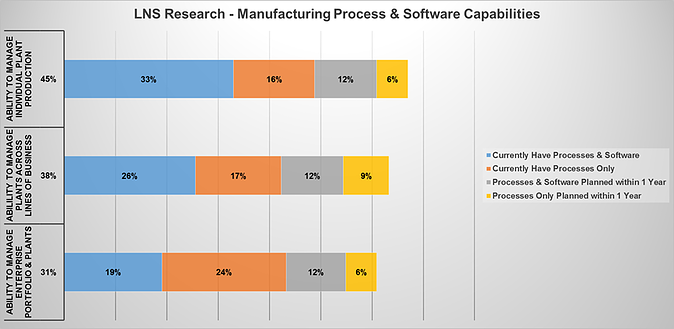
Get Your Leadership and Employee Engagement Initiatives on Track
To learn much more about effective leadership and employee engagement strategies to organize your successful Operational Excellence journey, register for the free LNS Research webinar “Leadership and Employee Engagement to Drive Operational Excellence” on September 23 at 10:00 am EST.
LNS Research Principal Advisor Mark Davidson will present key findings from a benchmark study of over 500 global manufacturing executives to provide insight to challenges and strategies organizations are facing today. Additionally, a case study of a European petrochemical company’s Operational Excellence journey will be presented to illustrate the success of these methods by experts at DuPont Sustainable Solutions.