Not surprisingly, in all of LNS Research’s practice areas--Quality, MOM, IEM and EHS--executive commitment is consistently identified as a key to success. Whenever business process management and change is discussed, top-level support always emerges as one of the top three enablers of (or barriers to) success.
Whether it is a Lean transformation or just a general business process improvement project, without top-level support the efforts will stall and benefits, if any, will be short-lived and ultimately the organization will backslide into “business as usual.” Asset Performance Management (APM) is no different. APM is like Quality, Sustainability, or Operational Excellence--as much a business process approach as it is a collection of supporting technologies. As such it too requires executive involvement and support to deliver benefits.
In this post, we'll discuss the role of APM as a business improvement initiative and then dive into three ways executives can influence its success.
APM is a Business Process Improvement Initiative
Unlike enterprise asset management (EAM), condition-based maintenance (CBM), or reliability-centered maintenance (RCM), all of which are associated with not only an approach to their specific area, but specific technology that supports them, APM is primarily a business process approach. EAM, CBM, and RCM are all technologies and methodologies that support and contribute to APM but at its heart APM is about how an organization approaches the ongoing support of the physical assets it utilizes to produce the goods and services it delivers.
Organizations with an APM approach recognize that, as we have said before, healthy assets are the foundation of a healthy business. APM practitioners understand that maintenance of the assets they use in their production processes is critical to not only their production volume but the quality of the products they produce and the energy and other resources they consume to produce them as well.
No single software application or technology can enable an organization to excel at APM. Instead, APM implies a culture where everyone in the enterprise recognizes that successful product delivery requires not only the people but also the actual plant itself to operate as “a well oiled machine.”
Top 3 Areas Where Leaders Influence APM
Like all other BPI initiatives, APM relies on top leadership to establish the culture where the BPI projects can thrive and be successful. With APM there are numerous ways leaders can have either a positive or negative impact on the success. We dive deeper into three of the most important ways leaders can impact the pursuit of APM.
1. Establishing the Right Culture
Leaders set the tone and establish the culture of an organization. To be successful with APM an organization must have a culture where production needs are balanced against asset health. If the culture is one where meeting production volume goals at any cost dominate, it generally follows that asset care becomes secondary and a “run it until it breaks” mentality exists.
Leadership needs to ensure that everyone understands production quality and volumes can only be sustained over the long term if sufficient resources are dedicated to keeping the physical plant operating at peak performance levels. This means that at the minimum a preventative maintenance program is in place and ideally a predictive program based on CBM and RCM principles is established.
2. Making the Right Investments
The second area where leadership impacts APM is in ensuring that the organization has invested in the right tools and training. To be successful with APM people have to have an enhanced skill set. Just being good at fixing broken equipment isn’t enough. Everyone, from operators to maintenance staff, also need to become skilled at using tools that help in predictive analysis.
Diagnostic and statistical analysis skills need to be developed in the organization. In addition, the technology to use these skills also needs to be deployed. Investments in equipment and infrastructure to gain additional insight into operational performance are critical. This ranges from handheld tools like thermo graphic imaging equipment to investment in building out additional measurement capacity via the IoT. This also implies an architecture that supports the integration of information from all relevant sources is deployed. APM cannot succeed without some investment.
3. Rewarding Teams, Not Heroes
As with most BPI initiatives, the biggest cultural change is the recognition that success results from team efforts and that heroic rescues are a sign of failure not an indicator of superior performance. If the mechanic who fixes a critical piece of equipment when it fails unexpectedly is treated like a hero and rewarded, the incentive to ensure unexpected failures don’t occur doesn’t exist.
It is far better to reward the team of operators, maintenance mechanics, and support staff when uptime and reliability goals are met. This can be accomplished by setting pay-for-performance standards that emphasize teamwork and taking a preventive approach rather than a reactive one.
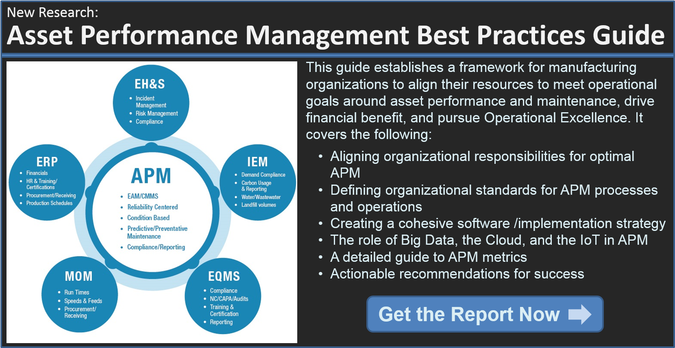