Asset performance management (APM) has many aspects beyond just the real-time elements associated with condition-based maintenance (CBM) and reliability-centered maintenance (RCM).
When discussing APM, people often focus on the “P” or performance aspects, and think about how well an in-place production asset is performing. However, to really take a holistic view sometimes you need to focus on the “A” in APM, and look at all of the components that make up a production asset, including the spares and repair parts.
The challenge many manufacturers face, though, is that they have production assets that have evolved over time and their maintenance, repair, and overhaul (MRO) inventory is not aligned with the actual asset base itself.
What Is Dead Inventory?
Inventory management for most manufacturing companies is focused around a combination of raw materials, work-in-process (WIP), and finished goods. Manufacturers try to optimize the inventory in several ways.
For raw materials, they want to have enough in stock so that they can maintain production volumes in the face of fluctuating demand, but not so much as to have capital tied up, especially if the raw material is perishable. Lean practices dictate that you have as little WIP as possible to maintain smooth flow in a pull type environment, and ideally you produce to demand so you have minimal finished goods inventory.
However, in asset-intensive businesses and in the maintenance operations of traditional manufacturing, MRO inventory management takes on a whole different flavor. When downtime is especially costly, the last thing a business needs is to have production halted while waiting for spare parts for repairs due to failures. At the same time there is the need to perform periodic maintenance, either preventive or predictive, which consumes MRO materials as well. Since many of the production assets are complex systems, repair and rebuild parts are common.
Most original equipment manufacturers (OEMs) recommend a certain minimum level of spare parts based on equipment design, performance criteria, and past experience. When installing new equipment most companies adopt the OEMs’ recommendations as a starting point, then adjust upwards if experience shows those levels are not adequate. Rarely do they adjust downwards.
During the course of the life of the plant, it is not uncommon for equipment to be replaced or upgraded, particularly as new technology displaces old. In certain areas like control systems as well as others, planned obsolescence also plays into the equation as OEMs try to phase out older equipment that may be expensive or difficult to support, forcing investments in newer generation equipment. This creates an environment where the level of spare parts in inventory may become seriously mismatched with the footprint of the installed equipment.
In the worst case, a firm may be holding spare parts for equipment they no longer even own. In the typical case they are probably maintaining spares levels based on the original footprint instead of what exists today. This excess spare parts inventory is dead inventory; that is--it is inventory that will likely never be used and so it sits on a shelf not only taking up space but also tying up dollars. It also creates complexity in that it expands the spare parts catalog, making data reconciliation more difficult and parts management more complex.
Bringing Life to Dead Inventory
When firms decide to get rid of dead inventory, the most common approach is simply to write it off and dispose of it as waste. In some cases it may be sold as scrap for minimal value. This approach misses out on a chance to recoup some of the hidden value in the dead inventory. What is one company's dead inventory may in fact constitute another company’s vital spares. Not all firms refresh technology at the same pace. When an OEM stops making spare parts for certain equipment, the value of new-old-stock (NOS) parts can actually increase if demand is high enough. Recovering the value from dead MRO inventory is a several step process.
First, a company needs to ascertain what is the appropriate level of spares inventory to maintain. This means a thorough inventory of spare parts--where they are used and when they were last used needs to be recorded. Then a risk assessment needs to be performed to determine what failure to maintain a spare might cost in downtime and lost production. Obviously, if the spares are no longer even relevant, the risk is probably nothing, but if there's still some equipment that might use the spares that risk needs to be assessed and alternatives, such as upgrade or replacement evaluated as well. Once an item is determined to be surplus its value needs to be determined.
While it's possible to use tools like eBay or other commercial marketplaces to try and sell MRO spares, it's not generally the best approach. One problem using generalist sites is that nomenclature and part numbers can vary widely, so potential buyers may not actually be able to find what you are selling. Another is that these sites often are not well-integrated with traditional business procurement applications. A better approach is to utilize a specialist site that focuses on dead MRO inventory disposal. There are sites that cater to mechanical parts, electrical and control components, and consumable materials. By choosing one of these specialist sites you're most likely to achieve maximum value for your dead inventory as well as having a seamless transaction.
Likewise, if you have aging equipment that for which you have difficulty sourcing spares, you might consider leveraging one of these specialist marketplaces as well. Dead MRO inventory doesn’t have to be a drag on operational excellence. With proper management, it can generate cash that can be leveraged in your maintenance operations and provide capacity for additional, more critical spares. It is definitely worth the effort to go through a dead inventory elimination process, particularly if your enterprise is pursuing lean as this clearly is a perfect 5S exercise.
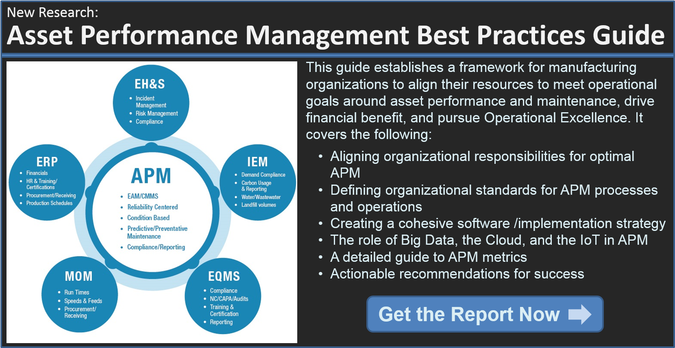