In our recent webinar and ebook on jumpstarting digital transformation with manufacturing operations management (MOM) systems, we introduced the idea of moving towards a Digital Twin in the digital journey. Although the term "Digital Twin" emerged some 15 years ago, it's only now that computing power and simulation technology is sufficient to allow us to deploy Digital Twin solutions.
Level-Set on Digital Twin
There are many definitions of Digital Twin but most simply it is a virtual model of something – in the world of industry usually a combination of product, process, and service. In discrete manufacturing, the Digital Twin can be of the product itself and also how it's made and how it interacts with its environment.
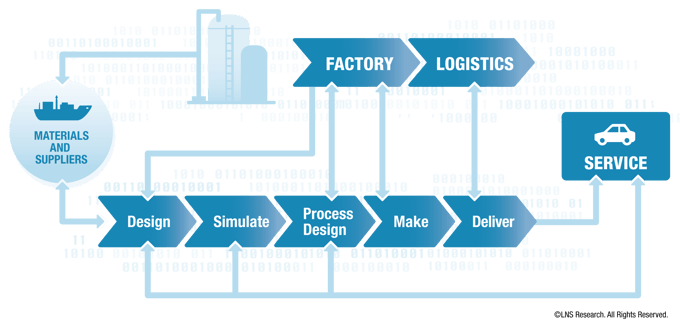
Another example could be airport infrastructure. Consider all the systems in an airport – all of them have to work together to bring passengers to and from planes safely, along with their luggage, duty-free purchases, and umpteen other constraints. A Digital Twin of an airport can simulate interactions between people, equipment, and the environment to allow airport staff to simulate issues such as breakdowns to constantly improve flow and customer experience. The ability to predict or anticipate potential issues or planning maintenance allows far less disruption. The scale and detail of the Digital Twin are only limited by reality – although a perfect Digital Twin of something as complex as an airport is going to take a while to create.
Is Digital Twin Right for You?
As companies set goals for Digital Transformation, it is worth contemplating how a Digital Twin will fit into the long-term enterprise and operational architecture. Rather than building lots of apps at the outset, a better strategy might be to start with a simplified virtual model of the environment to test apps in a virtual world before applying them to the real product or process. Once the model exists, trying new ideas and running complex analytics becomes a natural way of developing new functionality with low risk.
Companies can use a Digital Twin in many ways. During development, engineers can run mathematical and physics-based models on the twin to ascertain expected behavior. On the flip side, they can apply historical data from the product or process retrospectively to conduct analytics and what-if scenarios for behavior in unusual circumstances. The opportunities to add value to a product are almost limitless.
LNS Research will be studying many aspects of the Digital Twin over the coming months. From complex discrete, through automotive, life sciences and all the way to large continuous processes, we envision a great future for digital twins. Indeed, one can imagine a future where the product contains its own Digital Twin so a consumer could diagnose problems. Alternatively, a manufacturer could collect data from products in or after use to analyze performance expectations against actual. Ultimately, the twin could self-optimize to reflect upgrades, maintenance, and environmental changes. Imagine a Turing test for Digital Twin - Can you tell whether you are communicating with the real product or the twin?
All companies planning Digital Transformation should also consider how they can incorporate a Digital Twin into part or all the lifecycle of the product or process. We are quite sure that it will provide payback many times over.