The Industrial Internet of Things (IIoT) is clearly one of the most talked about topics in manufacturing. Smart Connected Devices, Smart Connected Assets, and Smart Connected Operations have featured prominently in recent research. At LNS Research we fully support the value of the IIoT and the way the convergence of Smart Connected Assets is going to change manufacturing over the remainder of this decade.
We have frequently pointed out that some of the most substantial value case stories around IIoT have been related to using smart connected assets to improve Asset Performance Management (APM) by reducing downtime, improve reliability, or reduce energy consumption. In virtually every magazine, on nearly every webinar, and at every user group meeting or vendor conference we attend the IIoT is high on the agenda with the monetary value of adopting smart connected assets in the context of APM as both a keynote topic as well as a common session theme or an article in a magazine as part of the ongoing hype associated with IIoT.
Despite the Hype Around the IIoT APM Still Can Derive APM Value from Offline Analysis Tools
Just as on the shop floor, APM is somewhat slow to adopt IIoT despite the number one objective being to improve operational performance, a key IIoT benefit. The majority of APM practitioners that have adopted preventive (PM) or predictive (PdM) maintenance practices are using offline tools like lubricant analysis and handheld vibration monitors as part of their program. And they can demonstrate real value from those programs.
The fact that offline tools are still a key building block in companies' APM programs illustrated their value. Many futurists argue that IIoT driven systems can drastically reduce or even eliminate these generally manually intensive procedures but the question is, “should they”?
Analogy to Healthcare
Anyone familiar with our medical care systems realizes that there is a mix of real-time and batch offline technologies utilized in patient care. Watch any medical show, especially the ER scenes, and you'll see the patient is hooked up to monitors that provide blood pressure, pulse, heartbeat, and oxygen levels in real time, yet the doctors invariably call for someone to draw blood or another fluid and get it to the lab for analysis. With all the hi-tech equipment, why are they always waiting on lab results?
From some recent personal experience I have witnessed first-hand the draws for the lab while still connected to a bunch of real-time machines monitoring seemingly dozens of other variables like pulse, heartbeat, and breathing. Part of the issue is that the measurements made by the lab have no readily available real-time sensor that could even measure a variable like clotting time. In other cases the value being measured in the lab is such a slow changing variable--like vitamin level--that a real-time measurement, while feasible, is not economically justified.
So to it is with our plant assets. Oil contaminant levels are such a measurement. While some lubricant values such as temperature, viscosity, or transparency could be measured in real-time dissolved metal is far more difficult to measure. Hence the value of batch sampled lubricant analysis in the lab. You can tell a lot more about the wear by doing spectroscopic analysis of the lubricant offline. You could perform online analysis but the cost for each piece of machinery would be prohibitive, so lab analysis remains the current practice. The same is true with vibration monitoring; for highly critical machinery real-time online monitoring may be justified but for much of the support and ancillary equipment handheld data collection on a periodic basis may be enough, particularly where the machinery would not be prone to rapid catastrophic failure.
Over Time the IIoT May Drive Towards More Real-Time Measurements
Except where there is no viable in-line real-time sensing technology in existence, the IIoT is going to drive the costs of real-time sensing continually downward, so that many things done via offline lab test today may in the future be accomplished in real-time sensors. In the meantime lab based maintenance diagnostic tools still have a valuable role to play in APM.
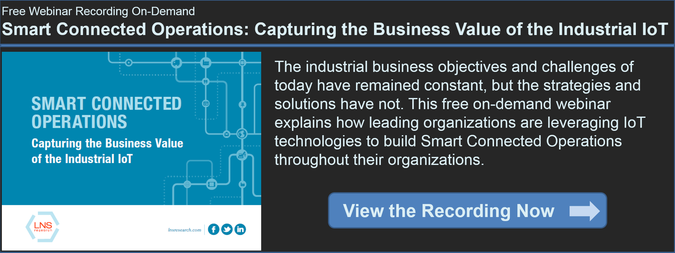