The Manufacturing Leadership Council (MLC) recently celebrated its 20th year of Rethink, its annual executive event that recognizes companies that are accelerating digital transformation. But before the big dance, or gala in this case, the event provided ample opportunity for manufacturers to exchange ideas and strategies through guest speakers, panel discussions, and networking breaks. Many focused on upskilling and training the workforce, engaging younger workers, and promoting diversity and inclusion across manufacturing.
Industrial leaders are facing significant skills gaps with newer, less experienced workers, rising material costs, and increased supply chain complexity. Discussions at
the event centered on digital transformation initiatives, adopting new technologies like artificial intelligence (AI) and advanced industrial analytics (AIA), and their impact on manufacturing operations, supply chains, and the workforce.
Those who attended in person (or virtually) walked away with more than a few new ideas on how to approach digital transformation. In this blog, I’ll highlight the key insights I heard at Rethink 2024, all of which focused on enabling manufacturers to navigate today’s turbulent waters and prepare for what’s ahead.
The Future of Manufacturing
This year, LNS Research had the honor of participating in a panel discussion on the industry’s past, present, and future. Manufacturing has undergone profound changes over the years, with significant workforce changes, the rapid pace of change, and the need to enable growth in the sector. The adoption of industrial automation and newer digital equipment has transformed factory floors, leading to more efficient and precise operations.
This shift enabled manufacturers to significantly decrease the number of bodies needed for production. In the U.S. alone, the number of manufacturing employees saw a 35% decline from 1979 (19.6 million) to 2019 (12.8 million). Without the need to always backfill employees who leave, the workforce matured and gained an incredible amount of institutional knowledge.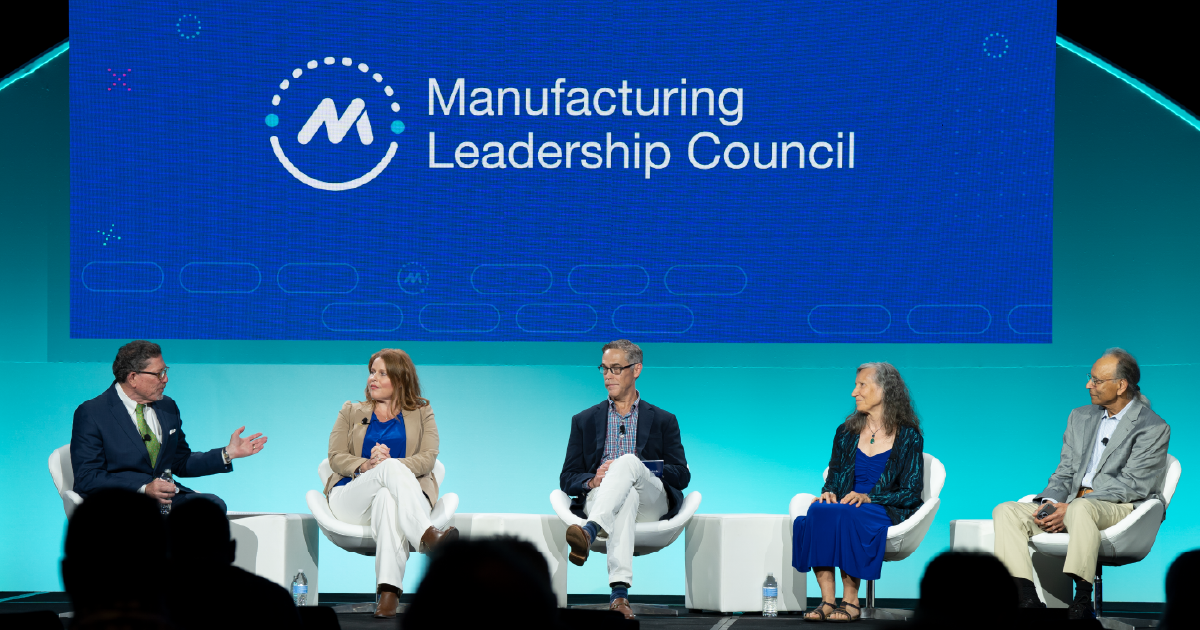
2024 MLC Rethink:
The Journey to Digital Manufacturing: Past, Present, and Future Panel Discussion
Fast forward to today and the ravaging effects of “The Great Goodbye.” We see a wealth of subject matter expertise concentrated in a shrinking pool of senior employees. Many find themselves unprepared for the number of new employees joining the ranks daily. Some have already recognized that the future of manufacturing will require new leadership styles, operating models, and approaches to deploying digital technologies to remain competitive.
Changing Employee Expectations
Today’s employees have different expectations compared to previous generations. They seek roles that offer meaningful work and opportunities to gain valuable and transferable skills, particularly in digital technologies. Over the next few years, the challenge will be to embrace the newer generations’ learning styles or risk losing the operational knowledge needed to maintain production.
This year’s Rethink highlighted the importance of partnerships between companies, agencies, and organizations to overcome challenges while driving innovation. While effective and engaging training is critical, the leadership approach is quickly becoming the lynchpin of a future-proof workforce (Figure 1). Employees are demanding more autonomy than ever, with the trend only expected to increase.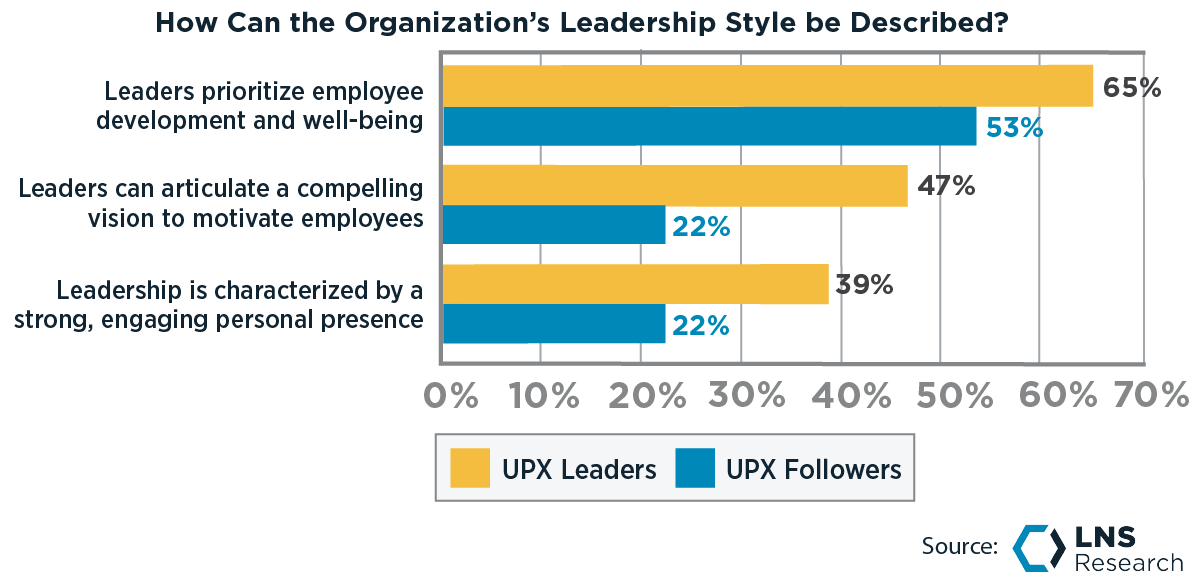
Figure 1: Industrial Operations Leaders, who typically have a differentiated leadership approach, have improved uptime, defect rates, and throughput by 30%+ compared to the 12% achieved by most Followers.
Some manufacturers have started to create newer operating models and better training for company leadership. Assessing professional skills has become an essential part of the equation when selecting leaders. Ultimately, employers must demonstrate genuine care for their employees, which can only be achieved with servant leadership practices.
A Future-proof Approach to Manufacturing Challenges
The new burning platform is the loss of institutional knowledge. Coupled with a shift in employee priorities toward life/work balance, efforts must focus on creating the total employee experience. Reoccurring themes at MLC support the LNS Research approach to future-proofing operations. Here’s how manufacturing leaders can better prepare for tomorrow:
-
-
-
Executives must develop comprehensive workforce development programs executed at the strategic level when defining a strategic vision for Operations 2030. Empowered employees and digital tools to capture and transfer knowledge from experienced workers to new hires are critical for more reliable and agile operations. The LNS Research Future of Industrial Work (FOIW) framework provides a roadmap for those beginning their journey.
-
Chief Operating Officers (COOs) must recognize that workforce initiatives can no longer be a side hustle but a critical element of the overall industrial strategy. Manufacturers will need to evolve their operating models to support the growing footprint of operations as newer, less experienced employees join the workforce. There’s an emerging trend of dedicated roles focused on improving workforce development and the overall employee experience.
-
Employees at every level must feel empowered to simplify processes and be supported by a modern operational architecture that seamlessly connects digital solutions. This approach eliminates non-value-added work, improves efficiency, and enables advanced analytics to unlock business value across the value chain while creating a more attractive work environment for the younger, tech-savvy generation of workers. LNS Research’s coverage of Unified Performance Excellence (UPX) and IX Reference Architecture has enabled members to accelerate digital transformation efforts and achieve real business value.
-
Cross-functional teams must be strongly aligned to strategic objectives and create business cases focused on desired outcomes. Standing up Virtual Operations Centers supports the subject matter experts on the frontlines and enhances decision-making across the organization. Metrics and balanced scorecards can help leaders stay aligned, prioritize limited resources, and recognize where adjustments must be made.
In Conclusion
The 20th anniversary of MLC’s Rethink conference underscored the importance of adapting to the evolving manufacturing landscape. Emerging technology has great potential, but true value comes from a strong foundation of people and process best practices. Push technology capabilities over solution selection by focusing on “why” and “how” rather than “what” (e.g., AI/ML, CFW Applications, Digital Twins, AR/VR).
Embracing digital transformation and fostering a culture of continuous learning will be key to sustaining growth and competitiveness in the years to come. Addressing the challenges of a retiring workforce, embracing the opportunities a newer generation of workers brings, and ensuring strategic initiatives focus on equipping employees with the necessary tools to succeed can better enable manufacturers to navigate today’s turbulent waters and emerge stronger. Nobody’s saying it’s easy, but that’s why you get paid the big bucks.
Join us in Boston this October for The Industrial Transformation Event to network with transformation leaders across the industry to accelerate your journey.
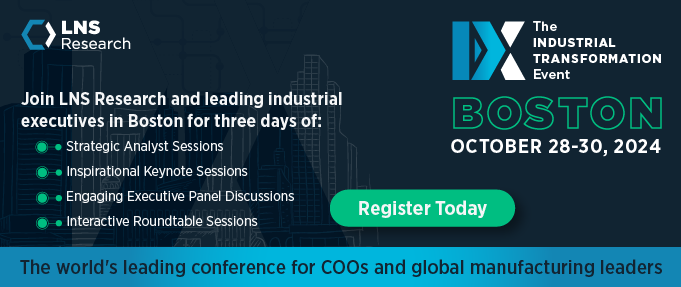