Manufacturing leaders can’t pay their way out of the unfolding labor crisis. Today’s workforce simply does not respond to higher wages, sign-on bonuses, etc. Many manufacturing leaders are focused on survival, while corporate executives and global stakeholders still expect the organization to deliver on bold sustainability promises.
Significant volatility and disruption in supply and demand have created a laser focus on surviving today’s manufacturing challenges with little bandwidth available to prepare for tomorrow’s needs. Often, manufacturing leaders believe that sustainability comes at the expense of financial performance. Without a substantial shift in mindset, this narrow focus not only risks falling short of meeting the expectations for sustainability improvements but also negatively impacts short-term and long-term profitability.
The net zero goals set at the board level (e.g., zero harm, zero waste, and zero carbon emissions) have many organizations reassessing their existing strategies and refocusing their efforts on enabling more sustainable operations. In this blog, I highlight how transformation leaders are protecting people and the planet better while significantly improving profitability (Figure 1). With LNS Research data showing those focused on improving overall sustainability achieve substantial improvements across revenue, operating margin, and more, there has never been a better time to reexamine the path forward.

Figure 1: Transform Business Performance with a Strategic Focus on Sustainability
Aligning to the Workforce Narrative on Safety
Manufacturers must first see that zero harm is a fundamental component of the firm’s mission and vision, which is then embedded throughout the company's strategy and operating model. LNS Research data shows that organizations with Industrial Transformation (IX) programs driven by the need to improve overall sustainability are more than 30% more likely to increase revenue, decrease the cost of goods sold, and improve operating margins by more than 5% (Figure 2). These companies go beyond the narrative and strongly focus on building the capabilities that realize safer, more productive operations.
The delayed effects of losing frontline leaders and their subsequent experience require that industrial organizations adopt new approaches to reaffirm long-standing commitments to safety and foster a culture among the current workforce. The negative perception of manufacturing as dangerous, dirty, and dull often deters talent from entering the industry. While technology is eliminating human risk from some tasks, there is still a need for newer approaches and techniques to protect those performing manual work.
Figure 2: Safety & Profit Leaders Have Significantly Reduced COGS
Newer generations are much more prone to “green quitting,” where an employee quits due to environmental or ethical concerns. The risk threshold for the workforce today is significantly different than it has been. With manufacturing still being such a labor-intensive industry, there is a critical need to gain a better perception across the next-gen workforce.
Maximizing Profit While Protecting People
Manufacturers continue to face economic uncertainty and a rising level of risk across operations.
Operating budgets for most have already gotten so lean that rising costs across raw materials, labor, and more are likely to increase with the changing pace of operations. A key enabler to real cost reduction is investing in new ways of leading processes and technology, often described as autonomous operations. These new techniques and technology also provide manufacturers with clear benefits in reducing safety concerns and physical work on the frontline.
Manufacturing Leaders should be looking to embed EHS initiatives, such as a Safety Observation program, across Operations and Human Resources to achieve safer, more profitable production. Newer employees entering the workforce come with a different skill level than previously seen. Organizations must first analyze corporate data to identify trends across recordable incidents, serious injuries, and unplanned events to align initiatives against the greatest risks and opportunities.
As this analytical work is done, hopefully through a robust Design of Experiments (DOE) approach, manufacturers will almost certainly learn that more stable and predictable processes, with less manual work or intervention, are inherently safer and more profitable.
Reducing Vulnerability and Building Resiliency
A forward-thinking strategy is imperative for manufacturers to develop the capabilities needed for the future. The World Economic Forum 2023 Future of Jobs Report estimates nearly 55% of manufacturing roles are going unfilled in the US, while almost three in 10 European manufacturers will see production constraints due to a lack of workers. Industrial organizations must focus on these changing workforce dynamics and what is needed to reduce employees' vulnerability.
Driving the organization toward a higher degree of enterprise standardization has enabled many manufacturers to leverage best practices and scale wins across production facilities. For many, prioritizing efforts is often the challenge, given resources are typically limited. What we recommend is assessing the strengths across these three capabilities that manufacturing Leaders are significantly investing in to build more resilient operations (Figure 3):
Figure 3: Resilient Operations Require an Investment in Foundational Capabilities
Industrials must focus on making dramatic improvements in fatalities and preventable fatalities across operations now. As average tenure and time in position decline, there is significantly more risk for injury. I believe it is imperative for manufacturing Leaders to broaden the focus beyond injury and illness rates.
Strategic Next Steps for Manufacturers
What may have worked in the past is failing to meet the needs of the future. Manufacturing Leaders must pivot from our traditional approach to transform both profitability and the protection of people. The drastic improvements across recordable incidents won’t be enough to enable stakeholders' zero harm expectations.
The strategic insights to identify risks and create a competitive advantage include:
-
-
-
Rethink how safety is measured and shift toward preventing serious injuries and fatalities by creating a near-miss program that rewards employees who identify risk. Expand beyond a responsible care mentality to show employees that leadership truly cares with proactive, regularly occurring safety discussions and meetings at every level of the organization.
-
Eliminate the emphasis on “quick wins” and “low-hanging fruit” with a drive toward using a systematic approach to enable the long-term vision for the company. Use cross-functional teams to identify the areas offering the most opportunity and the biggest risk to align resources toward the company’s business objectives.
-
Focus on adopting technology that enables the organization to improve sustainability overall (Figure 4). Initiatives should identify newer approaches, such as a Virtual Operations Center, to provide standardization yet simplify change management, knowledge management, architecture, and analytics for the organization with technology.
Figure 4: Emerging Technologies Being Implemented
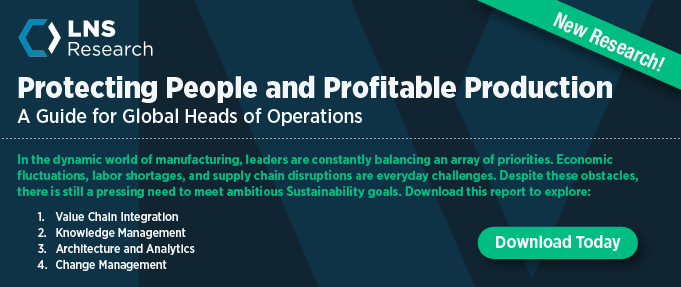