On October 3rd, LNS Research conducted its first Manufacturing Operations Roundtable on the subject of Smart Manufacturing. Besides our gracious host, Alcoa/Arconic, attendees included executives from Magna, Cargill, USG, Lexmark, Praxair, and Eaton. The day-long event started off with LNS Research setting the stage about Smart Manufacturing and what it is, and insight on where we saw the industry pursuing initiatives and success related to Smart Manufacturing today.
Click here to speak to Dan
Three of the participants presented case studies about their initiatives and journey towards Smart manufacturing. Interspersed with each short presentation was significant dialog so participants could explore issues in-depth as they might apply to their businesses. At the end of the day the participants took away their insights and learnings; but from the LNS Research perspective, five key learnings surfaced.
Smart Manufacturing is as Much About People as it is Technology
Smart Manufacturing may start out as a technology discussion, but quickly people issues become part of the dialog. Part of the impetus to pursue Digital Transformation stem from issues related to work-force generational shifts that are beginning to occur. Three key people related discussions that companies need to consider when looking at Smart Manufacturing are:
- How to capture or replicate knowledge that is retiring
- How to reduce the dependence on increasingly expensive labor, or how to reduce exposure of people to hazardous environments
- How to make the workplace more attractive and engaging to the digital natives that are entering the workforce today
Discrete or Process – Smart Manufacturing is Viewed as Essential to Long-Term Viability
Regardless of manufacturing style, Smart Manufacturing is viewed by most organizations as something they need to start dealing with. The number of companies that don’t somewhat understand the technologies associated with Digital Transformation are rapidly declining, according to data LNS has collected. Attendees at the event obviously were interested in Smart Manufacturing given it was the focus, but discussions validated it is a trend all of them see in their particular industries.
Operations is at Heart of Smart Manufacturing
While LNS sees the traditional hierarchical model of manufacturing operations shifting to a more networked approach, it is clear that at the heart of Smart Manufacturing the functionality associated with Manufacturing Execution System (MES) or Manufacturing Operations Management (MOM) applications today, is critical to the functional profile of a Smart Manufacturing deployment. Investment in a comprehensive MES or MOM solution may change going from monolithic to a more distributed model in the future, but companies today that seem to be best positioned to begin the Smart Manufacturing evolution are those that have standardized on a common MES backbone. It allows them to understand better and compare their various units’ performance, balance production, maintain genealogy and replicate successful continuous improvement initiatives across the company.
Analytics & Modeling Provide Significant Value
Whether it is to support reliability through Predictive Maintenance (PdM), better forecast quality, reduce energy consumption, or to optimize production volumes, analytics is going to be critical to the success of Smart Manufacturing initiatives. Most of the pilot projects or proof-of-concept projects all included some analytics and dash-boarding elements. This is consistent with LNS research’s survey results as well. The use of analytics to improve reliability remains the top driver for Smart Manufacturing investment today, although there is the recognition that complete business transformation is the potential end game. The ability to use Smart Manufacturing to transition from selling capital to selling capacity is still a ways off for most businesses, but analytics is a core competency companies must develop to succeed. The one mitigating factor could be machine learning. Given there is likely to be a shortage of skilled process experts with analytics skills or data scientists with adequate process understanding, machine learning capabilities could prove to be a way to overcome that hurdle.
Pilots Provide Proof Points and Build Confidence
Participants in the roundtable all validated the fact that the best way to gain buy-in for Smart Manufacturing is to build upon small successes. The ability to experiment, test, and validate is critical. Even though much of the technology behind Smart Manufacturing may seem to be old-hat, the reality is the way it is connected, and the information is used is changing. Additionally, as many of the more transformative tools, such as Big Data Analytics, are still rapidly evolving pilots given the opportunity to compare tools, vendors, and even approaches to the solutions. Several of the participants are members of the Smart Manufacturing Leadership Coalition and the SMLC pilot projects are proving to be a good way to spread both risk and learning among a larger community.
Bringing Smart Manufacturing Full-Circle
Interestingly, but in reality not all that surprising, all of these elements tie together. Pilot projects give organizations a chance to gain buy-in from the people on the shop floor as they can see firsthand how Smart Manufacturing will allow them to do their job better. Ultimately, analytics will become ingrained in MES and MOM functionality as an element of process optimization. What discrete manufacturers have developed as approaches to fulfilling small lot size orders profitably will translate to process industries seeking to break out of commodity markets using Smart Manufacturing. Likewise, process industries’ flow manufacturing style is influencing the way discrete manufacturers view production. So, what this LNS Manufacturing Operations Executive Council Roundtable validated is that business needs to take a systems engineering approach to Digital Transformation if they are to succeed in the pursuit of Smart Manufacturing.
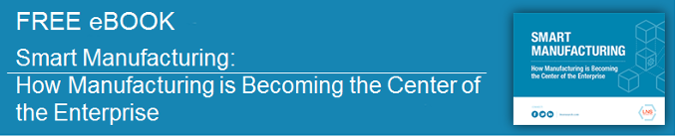