Information Sharing with and in Industrial Operations
Throughout the years, we have seen many terms used to describe the software used in industrial operations. Some of these terms have been quite technical, such as “Industrial Internet of Things” (IIoT)"; some have been functional, such as “Manufacturing Execution Systems” (MES) and “Asset Performance Management (APM)"; and yet others have been all-encompassing, like “Manufacturing Operations Management (MOM)." While these terms remain useful, evolving needs demand a new perspective on this software category.
It’s natural to ask, “Why do we need another definition for this space? Aren’t there enough?” The answers to these questions are:
✅ Things have changed
✅ Yes, there is a lot
What Has Changed?
The first observation is that the world of industrial operations software has changed from technology-focused to business-outcome-focused. As we have documented in LNS Research’s work on Productivity Pathfinders (companies that achieve extraordinary productivity growth) and Industrial Operations Strategy, how you run your operations can significantly affect overall business performance.
Here are the big drivers:
-
-
-
Unique production processes and unique products matter
-
Supply chains that collaborate beat supply chains that compete.
-
Your culture and internal organization will influence your outcome.
-
Delivered quality is a core element of success and an enabler for efficient operations.
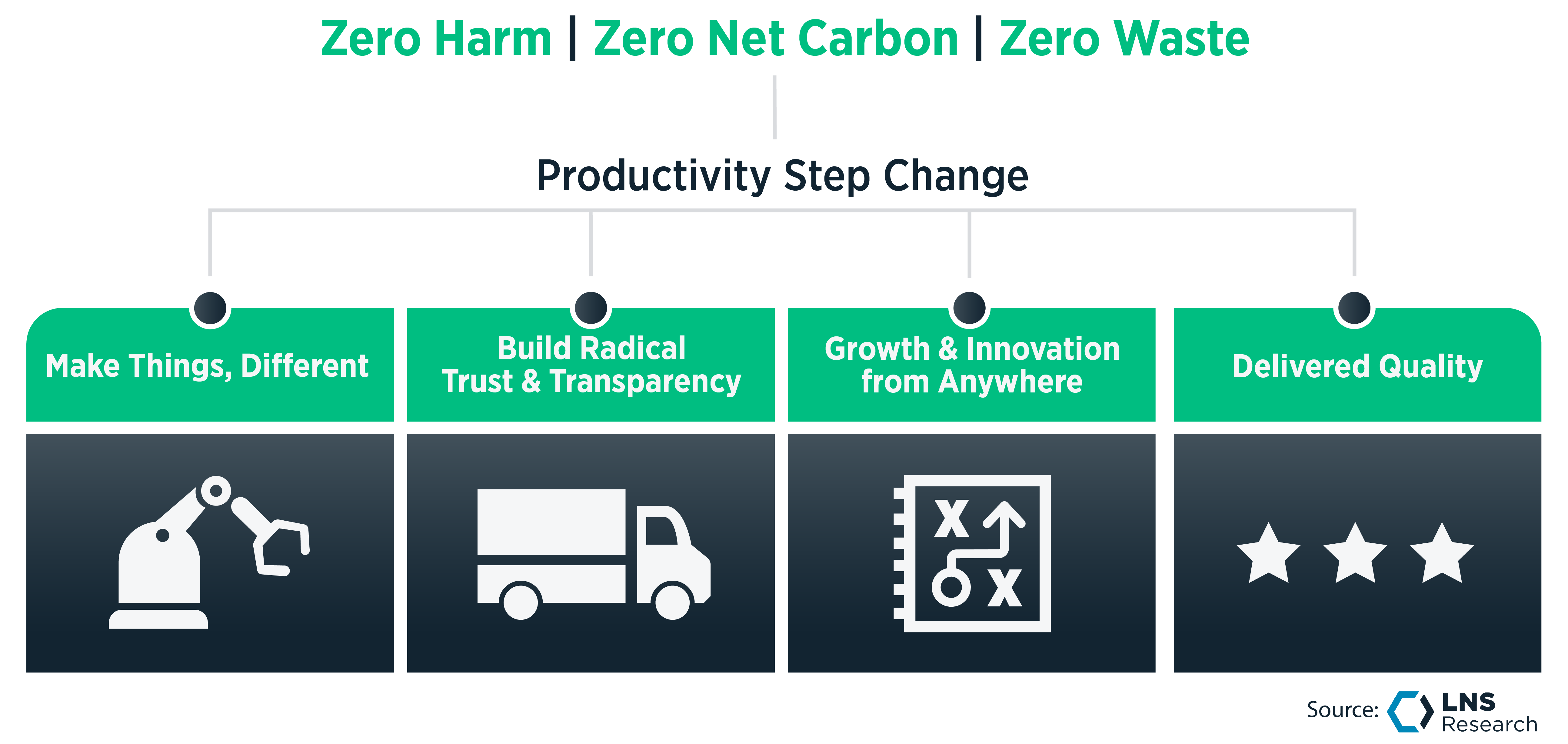
Figure 1: The critical elements for Industrial Operations success
The reality is that industrial operations need software that can support these drivers if they want a strong business outcome.
LNS’ research shows that Industrial Operations Leaders have a 36% higher operating margin, 34% higher throughput, 32% higher capacity utilization, and 22% higher uptime than Followers. Improving these metrics can lead to a substantial ROI if the investment costs are managed appropriately.
The core finding from this research is that operations need to improve their information sharing internally, with the right personas, across the organization, and across the supply chain. We need an Intelligent Supply Network.
What Has Not Changed?
A key finding in our discussions with industrial companies is the need for an approach that does not require ripping out and replacing existing software applications and other technologies.
Most companies cannot afford the disruption and cost associated with replacing all their applications at once. The issue is not just the license cost (which now can be annualized through a subscription) or the engineering cost of reconfiguring the applications; it is also the operational impact of changing all the processes implemented in the software.
Industrial software is analogous to the brain and nervous system of your body; there is no way we would allow anyone to rip and replace our nervous system just because we need surgery on the hand.
Our research shows that industrial companies are fatigued by the endless integration and customization efforts of some of the software applications created during the last decade. They are searching for a solution with:
-
-
-
Industry-relevant integrated applications
-
Flexibility to meet the uniqueness and innovation needs of each production plant
-
Openness to co-exist with multiple types, vendors, and generations of software and hardware
-
A data layer that enables cross-application collaboration
These elements, combined with the reduction of experience across the workforce, which has reduced safety, quality, and productivity, are forcing the industry to think differently.
The Intelligent Supply Network
The solution combines an Industrial Operations Strategy that prioritizes business outcomes with an Intelligent Supply Network, enabling the implementation of such a strategy.
An Intelligent Supply Network is
a set of future-proof technologies that,
when deployed in an information-sharing architecture,
enables a successful implementation of
a company’s Industrial Operations Strategy
across all its production plants
We don’t expect that there will be a software product called Intelligent Supply Network (ISN) that you can buy or subscribe to. As the definition says, it is a set of technologies, not a single technology or product.
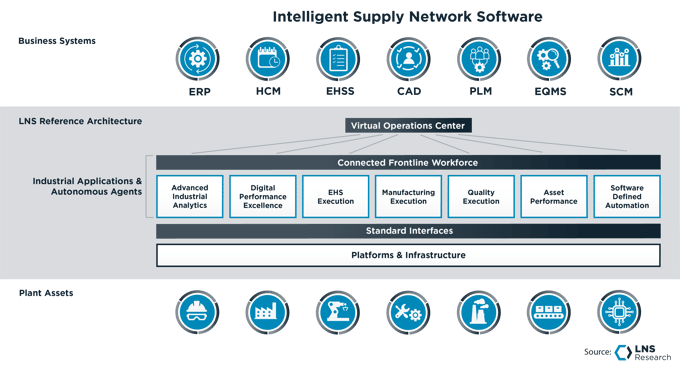
Figure 2: The Intelligent Supply Network Architecture
Industrial software does not exist in isolation; it needs to share information with the rest of the organization, but there are challenges:
-
-
-
It is connected to plant-level assets, which have longer life cycles than the software and unique operational characteristics and maintenance needs.
-
It is connected to business systems that implement rigorous, long-term processes and provide horizontal integration across the supply chain.
-
Internally, it needs to integrate the applications (Advanced Industrial Analytics, Digital Performance Excellence, EHS Execution, Manufacturing Execution, Quality Execution, APM, and Software Defined Automation) and autonomous agents that consume and produce information.
-
It needs to serve multiple user personas that perform critical tasks in the value chains.
We must use open standards and enable communication between personas, systems, and modules to achieve this.
We need an architecture that fits today's and tomorrow's workforces. A Connected Frontline Workforce (CFW) is the foundation for effective interaction with the people working in the plants. The Virtual Operations Center connects local and remote subject matter experts to the whole operations network, allowing them to use their knowledge widely.
The Intelligent Supply Network is improving information flow across two main value streams by leveraging open IT and OT communication standards, the product lifecycle (from Ideation to End-of-life) and operations (from raw material to delivered product), so that we can empower and share the use of the scarce resources that are within the envelope of control. This will unify IT and OT systems and reward software vendors offering open Application Programming Interfaces (APIs).
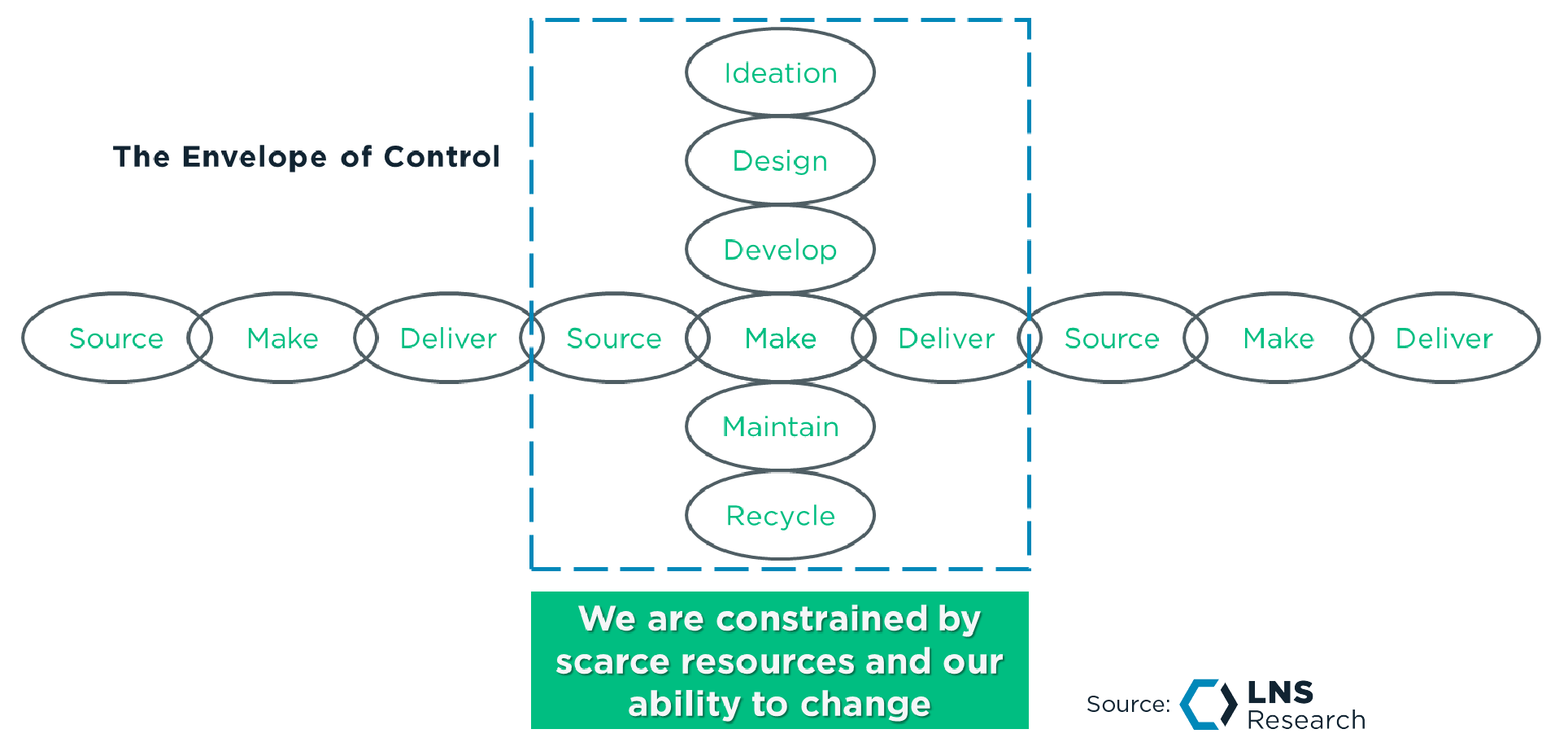
Figure 3: The need for information flow across value streams
While there is an overlap between the Intelligent Supply Network and previous approaches, such as MOM and IIoT, the differences stem from business drivers that reshape communication structures and the need to adapt to workforce changes.
You Are the COO; What Should You Do?
Given the constraints of time and resources, focusing on priorities is essential:
-
-
-
Establish your Industrial Operations Strategy: Whether you already have one or need to create one, the Industrial Operations Strategy is the key building block to align operations with the business. You may be efficient without it, but you won’t be effective as you are likely to spend time on the wrong thing.
-
Map out your key personas and use cases: Remember that access to skilled personnel will likely be one of your most important constraints. You need to keep this in mind so that you can create an intelligent supply network that empowers people to be more effective.
-
Collaborate with your CIO to align resources to business needs: Communicate the need to strengthen operations’ strategic role within the organization and the importance of having a strong Intelligent Supply Network as an enabler of effective information flow. Strive for effective resource usage to achieve the business objectives.
-
Review the LNS Research Reference Architecture to learn from best practices: While it may feel lonely where you are, you are not the first COO to face this battle. Take the opportunity to learn what works and what does not.
-
Build an information architecture that creates a path from today to the future: With the strategic business objectives as your destination and the current state as your starting point, you need to design an architecture that provides a path into the future without causing disruption during the transition.
-
Watch for LNS Research’s upcoming executive brief on this topic: We have a lot more details to share; watch for a deeper dive into Intelligent Supply Chains in our members' library.
I'm hopeful this blog post has highlighted the need to transition to an Intelligent Supply Network to achieve your business objectives and strengthen the strategic impact of industrial operations. We are looking forward to seeing how you progress on your journey.
