Manufacturing operations leaders continue to battle declining performance across safety, quality, productivity, and other critical key indicators that have circled the drain. Years of effort have resulted in significant challenges to protect the gains achieved through Industrial Transformation (IX) efforts. The good news is that some companies have accepted newer challenges and opportunities as catalysts to redefine the operating model.
This blog will explore how Industrial Transformation Leaders redefine the operating model to empower employees, address operations challenges, and improve KPIs. Many are including newer digital tools in the strategy to empower the workforce with the information needed to encourage innovation and improve safety, quality, and productivity.
The Degrading Base Case
Manufacturers have long expected a massive exodus of experienced personnel, with many relying on the capabilities in place to withstand this change. Unfortunately, LNS Research has found dramatic workforce changes have significantly impacted manufacturing operations. And while there is no longer a shortage of workers, the experience level across the workforce is far from what it used to be.
Leaders who believe that the same level of investment and support given to a team of 30-year veterans will get the same result as today’s environment of three-year veterans is sadly mistaken. Unfortunately, many have focused so intently on cost-cutting that blind spots hid the cracks that began to surface.
The foundation expected to withstand the exodus of experienced personnel is crumbling, affecting safety, quality, and productivity. Thinking about innovation and growth is hard when it’s a struggle to survive the year (or day). Manufacturers must recognize that the key to overcoming the degrading base case isn’t always investing in new technologies but protecting the foundational capabilities built over the years.
Industrial Transformation Leaders recognize the need to preserve and create value. Using Connected Frontline Workforce (CFW) initiatives, they focus on leadership, strategy, and culture to drive differentiated performance.
Connected Frontline Workforce
The challenges of managing a business often include balancing multiple stakeholders and competing priorities. Leaders can often be so focused on transformation efforts that the company invests heavily in newer advanced technology and less in maintaining vital operational functions. Many have found that prioritizing value creation primarily through technology deployments has become a disadvantage to the organization as highly experienced frontline employees leave, taking their experience, technical expertise, and leadership capabilities.
A business model focused solely on cost savings has yet to significantly improve safety, quality, and productivity KPIs. Implementing management systems that align functions and simplify processes can support employees and enable technology to scale across the enterprise. CFW initiatives can help build robust knowledge management systems by ensuring valuable information and critical insights are available when needed to maintain flexibility in a rapidly evolving business environment.
IX Leaders have focused on more agile systems and processes across manufacturing to ensure the organization can adapt swiftly to supply chain fluctuation and changing workforce dynamics. To achieve that, many have improved transparency and collaboration across the organization with newer CFW applications. Instead of making everything visible to everyone all the time, the priority for Leaders has been to provide the right information, at the right time, to the right person to reduce the time to productivity of new employees.
Empowered Team Leads
A newer, less experienced workforce requires newer approaches to support frontline workers in making better, faster decisions. The loss of 20+-year veterans will create a void where processes and technology are critical to empower the people in place. It’s not about how much data and sources the worker is connected to but how information is circulated to and from employees.
Manufacturers must develop solutions that can assess conditions throughout the operational management system, intuitively connect the dots to achieve a given outcome, and prioritize the tasks that must be performed to maintain operations. Industrial Transformation Leaders have found the key to greater flexibility and creating empowered team leads across operations is by creating a multi-directional flow of:
An empowered workforce enhances situational awareness and enables employees to identify risks and opportunities better. While many companies have leveraged innovation and moved from a labor-intensive workforce to one that can be more focused on value-creation activities, shifting to a holistic Future of Industrial Work (FOIW) strategy has been most critical to meeting the needs of the changing workforce and the fast pace of change.
Improving the KPIs that Matter
Newer techniques, advanced technology, and the arrival of automation have significantly changed the manufacturing frontline and are essential to achieving a competitive advantage. Manufacturers firmly focused on building a toolbox for employee safety, health, and support see significant improvements across EHS and operational performance. CFW applications provide the actionable insights needed to reduce unplanned events, enabling employees to focus more on finding innovative new ways of working, adding value, and improving product quality and productivity.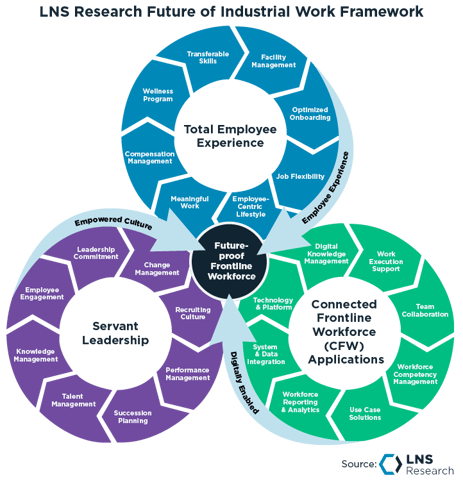
Manufacturers can significantly improve communication and collaboration and create more leaders at all organizational levels by focusing on these key enablers:
-
Create a leadership culture that prioritizes meeting the needs of the employees. The workforce does not generally need someone to reiterate profitability and productivity as key business metrics. Leaders should be focused on communicating where changes have created safer, more enjoyable work with fewer roadblocks to success to breed innovation and a culture of continuous improvement.
-
Promote a questioning attitude that continuously improves management system complexity. Procedures and work processes should enable the workforce, not an impediment constraining actions and activities. Evaluate each for the level of complexity and the desired outcome, making the changes necessary to ensure employees see the value procedures and processes are meant to provide.
-
Invest in digital tools that go beyond putting paper on glass. There is no real value in swapping out a clipboard for a tablet or some other device. Ensure the organization is committed to deploying tools that consistently reduce the cognitive load needed for tasks to create a future that enables employees more time to focus on value-added activities.
Increasing the circulation of accurate and timely information to, from, and among frontline workers significantly improves safety, quality, and productivity performance across operations. CFW solutions continue to develop innovative new uses for digital technologies, such as AI, AR/VR, and computer vision, to extend the functionality of conventional mobile applications. For more information on the functionality of CFW applications, refer to the LNS Research CFW Solution Selection Matrix (SSM) Guidebook.
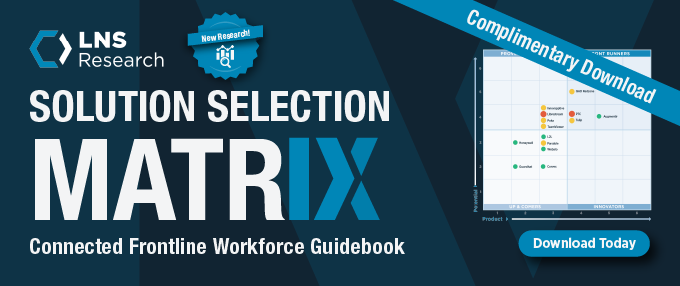