As business thinking has advanced and great leaps have been made in the digitization of manufacturing, quality has not kept up or transitioned to becoming a business partner. Instead, quality has dug in on the compliance approach as THE way to protect brand reputation. The evidence is mountainous against this strategy.
According to Statista data, recalls are on the rise. In 2023, the US had the highest recall year in over five years, and 2024 is shaping up to be worse than 2023 (Figure 1).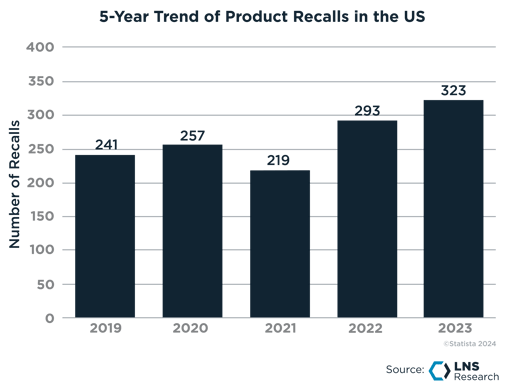
Figure 1: Recalls Highest in Over 5 Years
Boeing, Toyota, Airbus engine supplier Safran, Tesla, and JM Smucker are all companies that have experienced a significant recall or failure of their products sometime in the last five years. All are certified to various industry-specific quality standards: Boeing and Safran to AS9100, Toyota and Tesla to IATF 16949, and JM Smucker to GFSI, among others.
Compliance with these standards has not prevented these companies from having escapes to the marketplace. Compliance with quality standards is an expected requirement of doing business in manufacturing today, yet escapes and recalls are higher than ever before. Compliance is necessary but insufficient.
Virtually all manufacturers today are experiencing significant pressures to do more with less.
These challenges weigh heavily on manufacturing companies' daily planning and prioritization efforts. Adding a visible quality challenge to these might be a tipping point for a business. A case in point is Boeing. The company has been much written about and discussed in the media lately due to various quality issues over the last few years and currently. In its most recent quarterly report, Boeing reported a revenue loss of $6 billion compared to the same quarter of 2023! This is a steep price to pay for losing focus on the customer.
How did we get here? A Short History of Quality
The genesis of the quality profession is a story of war. During World War II, many manufacturers were redirected to making materials for the war effort. Failures were high; nothing was standard. This was the era in which "dud" was added to the lexicon as a descriptor for ammunition that didn’t fire or explode.
A move gathered steam to develop and adopt standards everyone could abide by to produce interchangeable components. Today, thousands of different standards and requirement sets cover virtually every aspect of any type of manufacturing, including quality.
As these standards proliferated and became expected. A specialist category grew to implement processes against these standards. These quality standards have always been focused on the customer but in a more esoteric sense. It is important to note here that these standards and processes were responsive to the environment that existed in manufacturing, namely an Industry 2.0 or 3.0 level of sophistication, where:
-
-
-
Data was scarce and expensive to generate
-
Machines were analog or primitive digital (Think Computer-Numeric-Control, CNC)
-
Workers worked for the same company in the same roles for 20-30 years
-
Training and development of expertise was through experience over time
-
Assets remained in service for decades
This was also the era of the advent of statistical process control and Westinghouse rules, which predicted future performance based on scant data about past performance and established guardrails to give more advanced warnings of an impending issue.
This is precisely where quality has been stuck for 50 years.
Why your traditional approach to quality is failing you
-
Over-indexing on Compliance
Traditional quality approaches to compliance are based on the “sampling” behavior that was an outgrowth of the Industry 3.0 era of manufacturing. Decisions were made based on the behavior of the sample data extrapolated across the population. The presence of “big data” in manufacturing has not shifted the methods that quality has stuck with for nearly 80 years.
As a result, quality has clung to traditional approaches and largely embraced software only if it helps make the quality function more efficient.
Our latest research on Embedded Quality found that Chief Quality Officers are over 80% more likely to prioritize compliance over their brand reputation protection (Figure 2).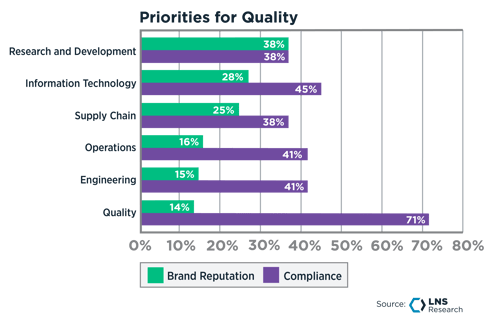
Figure 2: Quality Over-Indexes on Compliance
Let’s get one thing straight: compliance is not going away. It is an expected aspect of manufacturing worldwide today and shows no signs of abating soon. However, it is important to recognize its limitations and put them in proper perspective. Compliance is, at best, a snapshot of manufacturers' macro-level processes for designing and delivering products to customers.
Compliance is not a guarantor of Delivered Quality.
It is essential to recalibrate how the quality function can, in the modern age of manufacturing, enhance delivered quality outcomes to the customer while still maintaining compliance with requirements.
-
Good vs. Best Business Cases and limited within-function scope
The current reality in manufacturing is that business cases that would have passed c-suite approval 3-5 years ago no longer pass muster and are being rejected or put on the shelf for later.
Today's economic climate means business cases that include significant elements of “soft” cost savings are being viewed skeptically, even though evidence suggests these costs can be high, as in the Boeing example above.
An Embedded Quality business case that only includes the efficiency of the quality function is 52% less likely to gain C-suite approval (Figure 3).
Bold moves are needed to achieve significant results.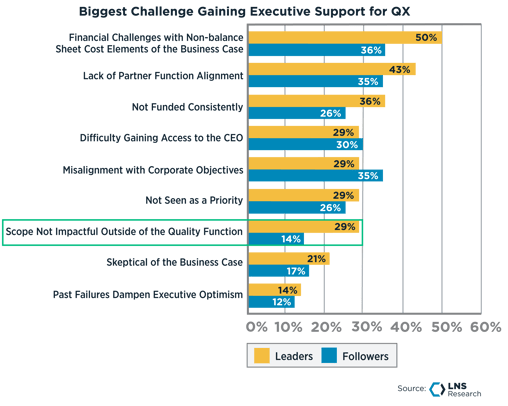
Figure 3: Within-Quality Scopes Don't Gain Approval
-
Misalignment with other transformations already in flight - the Goldilocks problem
Transformation is like trying to rebuild an airplane while flying it. Synchronization and collaboration are essential to keeping the aircraft in the air. Our Embedded Quality research shows evidence of the push-pull effect between transformation initiatives, with 47% of companies surveyed reporting that Embedded Quality transformation impacts overall momentum by either being too far ahead or behind companion initiatives. Collaboration and partnership are essential to moving forward in concert.
-
An unearned license to transform
Our research shows that 86% of Embedded Quality transformations are led from outside of the quality function. Quality leaders have not pivoted to Delivered Quality outcomes as the driving force behind quality transformation. They have yet to earn the trust of value-chain partners and C-suite to own their transformations (Figure 4). As a result, quality transformations led from outside the quality function are primarily focused on reducing the cost of the quality function through efficiency gains.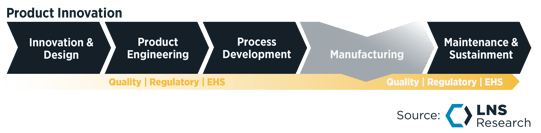
Figure 4: Value-chain Focus Earns Trust
Embedded Quality Leaders who focus on Delivered Quality are over twice as likely to lead their own quality transformations.
Focus on Delivered Quality and Customer Outcomes
Companies aspiring to grow need an advantage. In our research on Embedded Quality, we found that Delivered Quality was the primary path to competitive advantage in the market. Delivered Quality is in the eye of the customer, defined and recognized by the customer as they use your product. There are many descriptors of delivered quality. Among them are:
-
-
-
On-Time Delivery
-
Functionality
-
Reliability
-
Value
-
Consistency
Delivered Quality is the North Star of an Embedded Quality Transformation (Figure 5).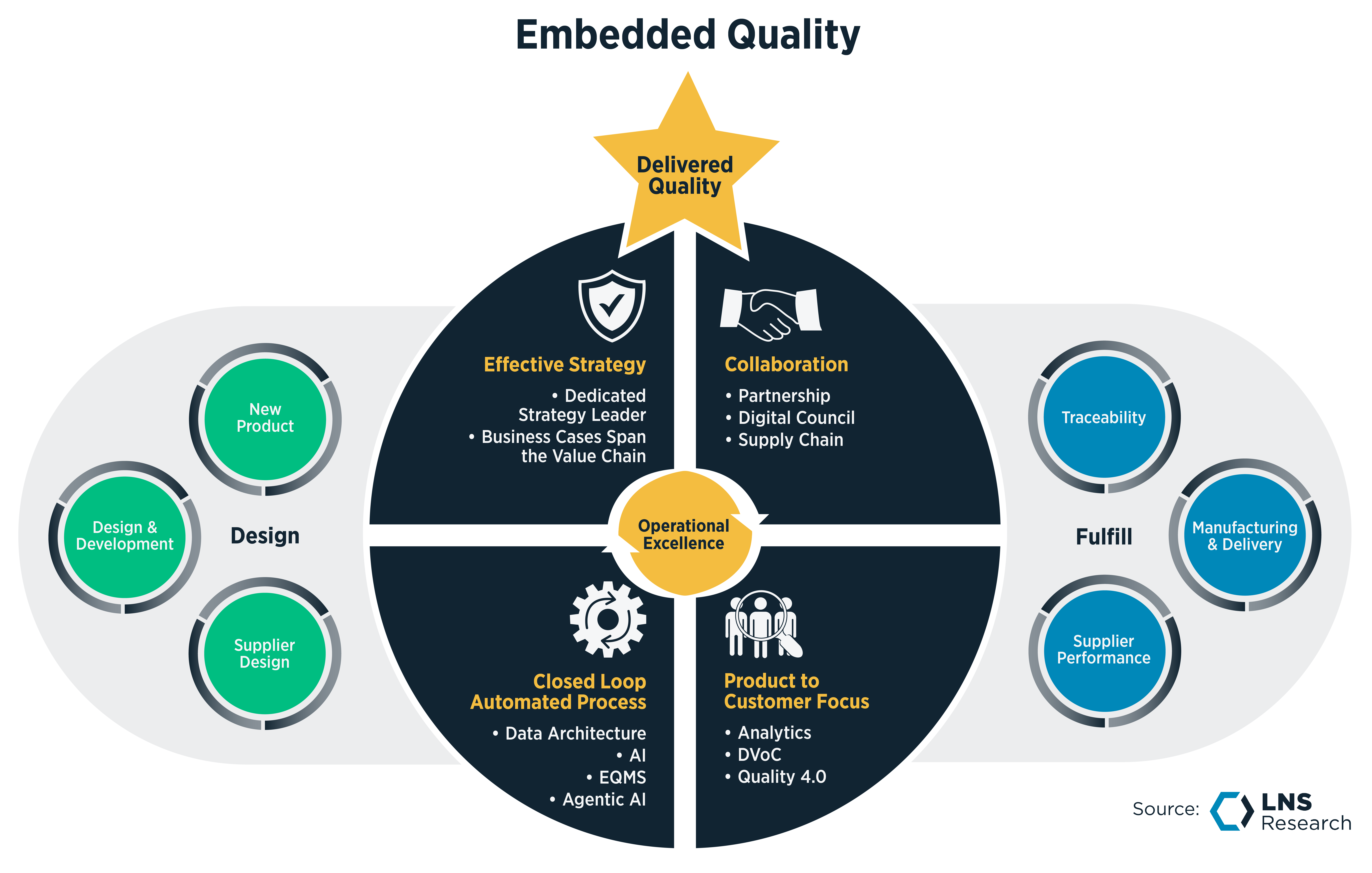
Figure 5: Embedded Quality Framework
A value chain focus for the quality function is familiar but has, up to now, been directed toward compliance activities.
This new research shows an uptick in those reporting significant business results from their efforts around Embedded Quality, up 6% since 2021 to 24%.
This still leaves the vast majority, over 75%, trying and failing to transform quality successfully. They are still lost in the compliance wilderness and have not come to grips with the fact that compliance is necessary but not sufficient to earn their license to positively impact not only quality’s status within the company but also the company’s overall competitive advantage.
Recommendations for Chief Quality Officers
- Delivered quality is the North Star
Quality the customer can see and feel is a competitive advantage and the guiding principle of an Embedded Quality Transformation.
- Enhance positive culture with an effective quality strategy
An effective quality strategy builds from efficiency to collaboration and influence across the value chain, embeds quality practices, and implements data-based decision-making across the value chain.
- Deliver the promise of Quality 4.0 by tying the value chain together
Engage and align with industrial transformation initiatives already in flight. Build a quality data architecture that spans the value chain.
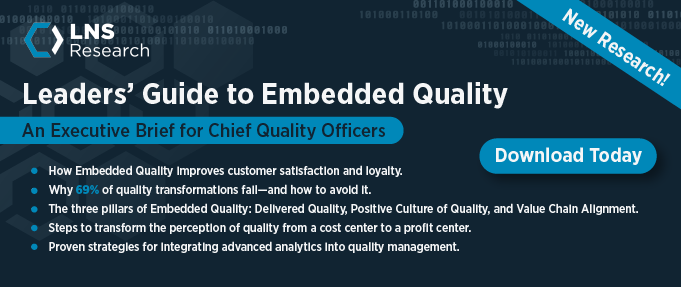