On January 29, 2014, LNS Research and Manufacturing.net hosted a webcast entitled, Accelerating Operational Excellence for Global and Regional Manufacturers. Toward the end of the event, we received a flood of questions from attendees, some of which we weren't able to answer because of time. In this post, I'll address the top 10 questions we were asked.
For those who weren't able to attend the webcast, here's some background information. With support from our research of industry best practices and data from our recent Manufacturing Operations Management (MOM) survey, this webcast highlighted manufacturing professionals' top operational objectives and challenges, discussed the role of people, processes, technology, and metrics in operational excellence, and drilled down into specific benchmark results and recommendations on strategies for the following areas:
If you are interested in listening to a recording of the webcast, it is available here.
Questions & Answers
Given that Operational Excellence for manufacturing industries is a broad topic, as mentioned, we received a number of great questions (too many to address in the live webcast). We'e chosen the top 10 below.
Q: Are you seeing Operational Excellence used as a catch-all term that encompasses all or a combination of manufacturing programs, or is it a specific program unto itself?
A: We’re seeing some of both. Most companies, however, refer to Operational Excellence as their overall set of continuous improvement initiatives to align their people, processes, and technology to increase their business and manufacturing performance. That said, as you can see from our survey, 23% of survey respondents indicated that it was a specific process improvement program unto itself.
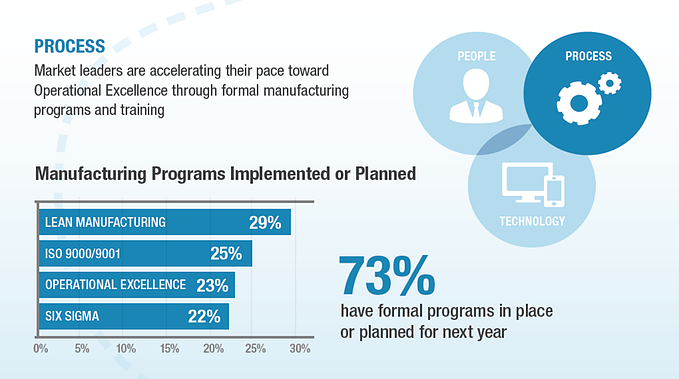
Q: How can we tell if we’ve actually reached Operational Excellence?
A: Operational Excellence targets are typically changing every year for an organization based on changing dynamics of their marketplace, increased demands from customers, more intensive competition, etc. So even if you are a market leader today, companies cannot rest on their quest for Operational Excellence. It’s a continuous journey with new dimensions of excellence and new targets as the journey progresses.
Q: The concept of 'MOM' seems to appear mostly on your site and publications. How widespread is the comprehension of this category? I know of a couple of CI consulting practices that are actually now going after Business Process Management (BPM) instead.
A: MOM - Manufacturing Operations Management - concepts are widely in use in industry by manufacturing companies, solutions vendors, industry standards activities such as ISA-95, MIMOSA, OAGIS, OPC, and industry analysts alike. Business Process Management (BPM) consulting practices typically align well to MOM concepts in that they often look across the entire manufacturing value chain of ‘end-to-end’ Enterprise, MOM, and Industrial Automation processes. BPM consulting is typically focused on simplifying, streamlining and harmonizing business process across entire manufacturing enterprises.
In the LNS Research process model below, we identify some of the key interrelationships between Enterprise/Business processes, Manufacturing Operations Management processes, and Industrial Automation processes. The combination of these three are our definition of ‘end-to-end’ business processes.
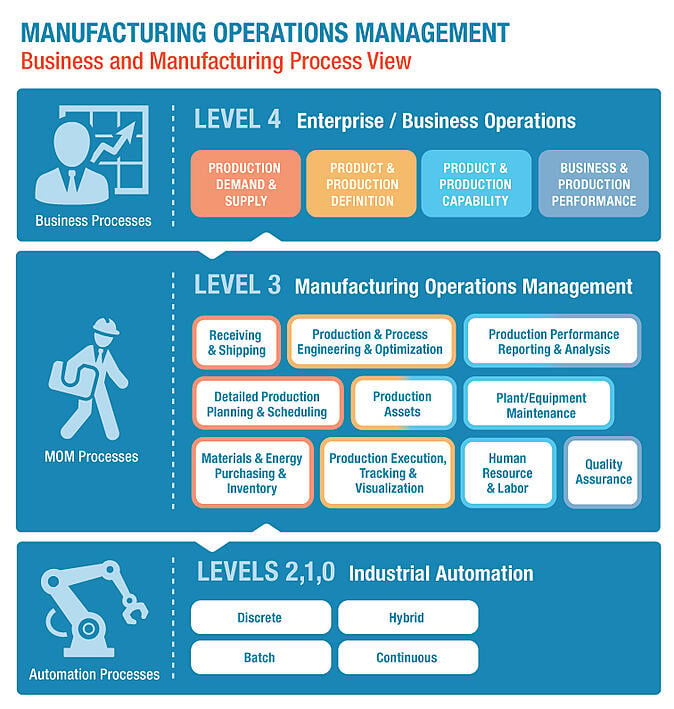
Q: For a majority of the organizations, the KPIs are well established and every year they are improved, so how do you say your process is improved?
A: This may sound obvious, but different Key Performance Indicators (KPIs) are used to measure different things. Some KPIs are direct financial measures such as cost reductions. Others are indicators of how fast or well a process is working, such as New Product Introduction time. Other KPIs are a combination of process effectiveness and quality, such as OEE which accounts for quality, downtime, and production output in a single KPI. For more information on the top 28 KPIs being used in manufacturing, your can check out this blog post.
Q: What is the role of incentives – monetary or in-kind – in Operational Excellence?
A: Incentives can play a key role in helping to drive Operational Excellence. In the webcast, we discussed the importance of goal alignment and deployment across an organization and the need for rewards and incentives. We also discussed how it is important for each employee to have both some shared team goals as well as individual goals. People generally want to succeed and do the right thing, and when their team and individual performances are aligned and rewarded with better pay increases, bonuses, peer and company recognition, extra time off, and so on, this reinforces the value of driving Operational Excellence and makes it very personal. So the awards don’t always have to be financial, they need to be rewarding and gratifying and sometimes made visible to others in the organization.
Q: It sounds like the technology side of the people, process, technology equation is exciting but somewhat in the development mode. For mid-size to smaller manufactures is it wiser to wait until this software and technology solutions are more integrated and stabilized?
A: By speaking about the future impact of rapidly emerging technologies in this space such as Big Data, Cloud and, Mobile, I regret that the impression may have been created that there are not software and technology solutions that are proven and available today for small, medium, and large enterprises alike. Nothing could be further from the truth! Software solutions in the MOM space have evolved over that last 30 years and the top 6 MOM applications that are in use by companies that are effectively managing their production operations are shown in the chart below.
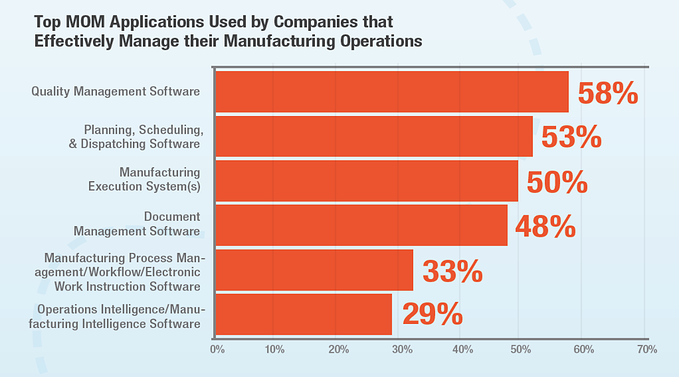
Q: Where do you see practical areas of application for cloud-based MOM solutions? As these are very often critical and even real-time solutions, it seems to be contradictory to cloud approach.
A: We believe that advancements in cloud technology and end-user attitudes have now shifted to a point where adoption rates of MOM cloud technologies are poised to increase significantly, and the data is beginning to reflect this with cloud adoption expected to more than double this year – from 7% to 17%. Information applications that provide data collection, such as enterprise data historians and real-time operations intelligence/manufacturing intelligence applications, are good examples of applications that are practical and available today on the cloud because they don’t impact the systems that manage actual production.
Also, critical manufacturing data can remain within the plant-side systems while using cloud technology to aggregate information to generate reports, calculate manufacturing KPIs, distribute information to mobile users, and other functions. Another example of a mission-critical cloud application is manufacturing ERP. Given that some companies have already embraced the need for ERP to link to manufacturing in order to be able to produce, the next logical extension becomes the acceptance of cloud-based manufacturing ERP. A number of companies have been successfully serving customers with their manufacturing cloud (learn about them in our MOM Solution Selection Guide).
Q: When process and people pillars are not in place, is the technology pillar a waste?
A: Not necessarily a waste, however, technology solutions are likely to be not nearly as effective, if they are not specifically aligned to support the processes and the people doing the work. A better approach is to start by first looking at process improvements and the role of people in those work processes, and then once you have proven out the improvements in a more manual fashion, add technology to systematize, speed, inform, and enhance the situation.
Q: How do you quantify the cost associated with the Operational Excellence journey for budgeting purposes? I understand that this is a very difficult question.
A: This is one of the top challenges that was identified in the MOM survey, with 25% of companies being challenged to create Return On Investment (ROI) justifications for improvement projects. A best practice that we have seen is to start with an area of potentially high impact to the business with a small pilot in order to prove the concepts, and then use the data generated from the pilot to build the business case for scaling up the efforts. Many times, an Operational Excellence journey is a ‘pay as you go’ proposition, whereby each step in the journey needs to generate enough savings, top line growth, or customer satisfaction to fund the next steps. Once a company gets better at their continuous improvement processes and successes, management confidence grows and the ROI justifications will occur much easier. It’s a matter of practice, practice, practice.
Q: I believe the speaker just mentioned a book available on the subject matter of this presentation. Where can I buy this book?
A: LNS Research has created a 29 page eBook that summarizes how to accelerate your Operational Excellence journey, containing research, and best practices. It’s available to anyone who signs up for the webinar. You can actually sign up for a recording of the webinar by following the button below.
For additional Operational Excellence or manufacturing software questions, email Mark at mark.davidson@lnsresearch.com or tweet to him @markymarketing.
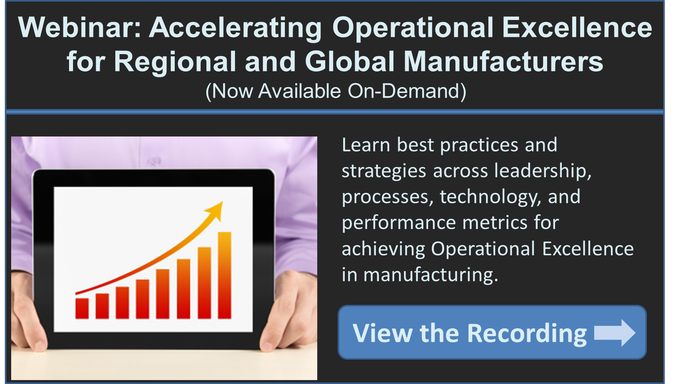