Supplier Quality Management (SQM) has been important in certain industries for decades, and increasingly important across most industries. However, SQM automation rates remain stubbornly low, with just 23% of respondents in LNS Research’s Quality Management survey stating that they’ve automated SQM with software (for more information, read this). Likewise, SQM best practices are implemented by just 24% of respondents.
Click here to speak with Dan
This persistent low adoption is a surprise. Quality executives have identified SQM as a short term improvement area for years, and 21% of survey respondents indicate that lack of visibility into supplier quality is a top challenge preventing them from meeting strategic quality objectives.
Implementing SQM Best Practices Results in Reduced Supplier Defect Rates
In an effort to move the needle on SQM Adoption, we’ve used the LNS Research Quality Management survey data to compare companies that have implemented SQM best practices with those that haven’t. The survey identifies people, process, and technology adoption, as well as Quality metrics from more than 700 quality executives. For this post, we used the survey data to correlate implementation of supplier-focused best practices with performance in Supplier Defect Rate (SDR), a good measure of supplier performance.
The result of this analysis provides Quality Executives with a tool to prioritize SQM best practice implementations. It also clearly identifies the impact of implementing SQM best practices.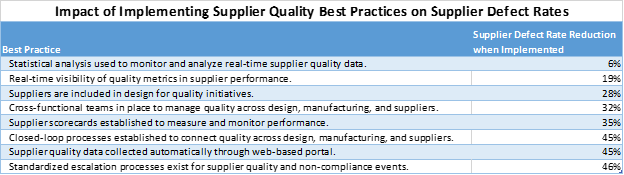
The chart above shows the reduction in SDR reported by respondents who have implemented a best practice versus those that have not implemented. For instance, companies that have implemented “Standardized escalation processes exist for supplier quality and non-compliance events” have a Supplier Defect Rate that is 46% lower than those that haven’t.
Takeaways for Quality Leaders
The graph above provides some excellent insights into the impact of specific best practices on Supplier Defect Rate. We can also extract some broader insights as well:
SQM Best Practices Improve SDR Performance
It’s clear that implementation of SQM best practices universally results in substantial SDR reduction. Comparing your company’s current SQM best practices against the chart above can identify opportunities for improvement as well as prioritization of best practices.
Deploy “Core” SQM Best Practices First
If your organization has yet to embark on the journey to mature SQM, start with core SQM best practices such as “Standardized escalation processes exist for supplier quality and non-compliance events”, “Supplier quality data collected automatically through a web-based portal”, and “Supplier scorecards established to measure and monitor performance.”
These practices are widely supported by commercial SQM technology, and cover processes such as deviations/waivers, non-conformances, Supplier Correction Action Reports (SCARs), audits, and scorecards; as well as other industry-specific SQM processes, such as Production Part Approval Process (PPAP). Another factor, possibly more important for a fledgling SQM program, is that these practices can be tackled with a smaller set of internal functions (e.g. Quality, Supply Chain, & Purchasing).
The chart above clearly indicates that this “walk-then-run” approach will result in measurable improvements in Supplier Defect Rate.
Improved Communication & Visibility Between Suppliers & Internal Stakeholders Drive Success For All
All of the best practices improve communication, visibility and collaboration between suppliers and internal stakeholders. All best practices result in reduced Supplier Defect Rates, which has many extended benefits for the customer, including lower cost of poor quality, higher Overall Equipment Effectiveness (OEE), and higher on time delivery.
It also has a similar impact for the supplier, through reduced rework, failure analysis, etc.
Extend Processes and Teams to Include Suppliers
Extending closed loop processes, cross functional teams and design for quality efforts to include suppliers results in substantial benefits. However, this work can be challenging as it involves multiple internal stakeholders, and is strongly influenced by historical customer-supplier relationships and culture.
At one end of the spectrum, there is the Japanese approach of Keiretsu, where customers and suppliers have extremely tight and codependent relationships on each product, as well as at a corporate level. These relationships last decades, and both sides work together to generate continuous improvement.
On the other end, there are adversarial - but still connected – customer and supplier relationships. Information is exchanged, but there may be the threat of intellectual property infringement or theft, co-opetition, nationalism, etc.
Quality Leaders Should Build or Update Their SQM Plan
SQM Best practices have a clear impact on core Supplier performance metrics, which should impact prioritization of SQM as a whole. Additionally, the recommendations from this post should be an input to SQM implementation plans.
Quality leaders, access the On-Demand webcast now! This webcast provides senior leaders with best practices for building a business case around quality and the foundational framework needed to gain executive commitment.
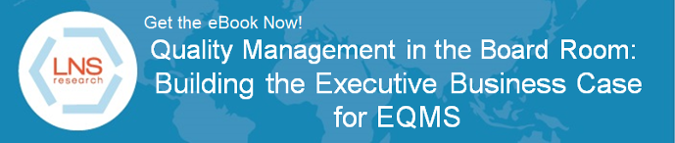