We’ve been writing a lot about the benefits of increasing communication and collaboration by breaking down traditional functional barriers in manufacturing. When searching for the solution to a problem, collective knowledge is almost always the better choice. Manufacturing software and IT advancements are highlighting the fact that compartmentalizing information, or keeping it in what many refer to as silos, is inefficient and often results in sub-optimal decisions.
Quality, for instance, is a great example of how a single process is often monitored by many disparate management systems across the value chain. Companies understand that quality is important, but areas such as engineering, manufacturing, and the global supply network manage it differently. However, when integrated correctly, it can be a powerful tool. One area that we believe it can make a particular impact in is Product Lifecycle Management (PLM). By measuring quality at the conception of an idea, issues can be assessed and resolved through the product's life until disposal.
In this blog, we'll discuss the importance of quality in the manufacturing process and also begin our discussion of PLM-centric quality management.
Why is Quality Important?
Because the quality of an organization’s products has various effects on productivity, cost, compliance, and safety as well as a multitude of other areas, quality is a pervasive issue and should be watched vigilantly. Nonconformances that directly touch consumers can manifest as changes in reputation, legal issues, and backlash on increased prices. As each of these issues can have grave consequences, especially for the cost of quality, we will start our discussion of why quality is important here.
Mentioned in prior blog posts, the cost of quality is an equation with two variables: the cost of good quality and the cost of poor quality. Lacking communication and feedback in different phases of product design, production, and post-production has adverse effects on both the cost of good quality and the cost of poor quality. For example, a siloed customer complaint, which could have helped to fix a persisting nonconformance in design, may have a drastic impact on reputation, pricing, productivity, safety, and compliance down the road. Because these quality issues can surface in many ways, the earlier we begin monitoring the cost of quality, the more accurately we can estimate and control it during a product's life.
Combining PLM and Quality
The issue of managing systems or single processes in silos is nothing new. Many different types of software have targeted this problem, perhaps none more successfully than PLM. It helps companies better manage workflows and product data at each stage of product development, delivery, service, and end-of-life processes. Understood as both a technology and methodology, PLM is designed to connect multiple disciplines of engineering as well as with the broader value chain.
As we continually advocate for collaboration in manufacturing, LNS Research believes that PLM is a strong focal point for managing quality within both single processes and acorss the enterprise. In our next blog, we'll inspect how PLM and quality can be used together to drive business performance.
If you would like to read more on the topic of quality management, please click the button below to become a part of our community and gain access to our Quality Management Systems Research Library.
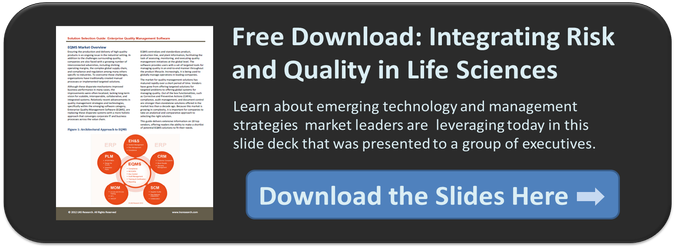