EMI or Enterprise Manufacturing Intelligence software appears to be hitting its stride across a wide range of manufacturing industries, due to the need for increased real-time visibility of cohesive manufacturing and business performance-related information. Additionally, advanced, yet simpler-to-use analytics technologies, are becoming a more pervasive component of EMI and other manufacturing business solutions.
But the key questions are 1) What are the business results that manufacturing/production companies are achieving utilizing these software capabilities? And 2) What should you and your company be doing in regard to the opportunities presented by these technologies? In this post, I’d like to explore these two questions/topics a bit.
Understanding EMI Software
If you're not familiar with what EMI software is and what it does, we’ve written a number of blog posts and research reports on the topic in the past. As a good introduction, I suggest this blog article: "How EMI Software Has Changed Manufacturing Operations," and this eBook research report: Getting Started with EMI. And if you would like more background on the associated analytics technologies, I suggest this blog article: "Will Analytics Power The Next Wave Of Manufacturing Performance?"
The Real Business Results and Where They Are Coming From
One of the core capabilities delivered by EMI software is operational and business performance dashboards that provide timely information to different users and roles. And 61% of companies in the LNS Research Manufacturing Operations Management (MOM) survey of over 550 professionals indicated that their companies either currently have EMI dashboards or are planning to install them in the next year.
Since one of the key functionalities of EMI software is to contextualize information from multiple data sources, embedded analytics technologies are often used to accomplish this. Sometimes these analytics are very simple and enable basic calculations for a mash-up of different data points into a single information visualization on a dashboard.
In other cases, more sophisticated analytics techniques and technologies are becoming more commonplace as part of both EMI and Business Intelligence (BI) software solutions. The same MOM survey showed that 32% of companies will be deploying more sophisticated analytics/intelligence like Big Data analytics to mine data and uncover new manufacturing and business insights over the next year, up from 17% currently.
LNS Research has uncovered significant correlations between EMI software solution use and manufacturing performance metric improvements. The joint LNS Research and MESA ‘Metrics That Matter’ survey uncovered a significant difference in average annual improvements in the costs of producing a unit of goods. Current users of EMI software recorded 24.1% average annual improvements in Total Cost per Unit Excluding Materials versus the 13.1% overall improvement of all respondents. This relationship stands to reason, as the timely visibility of operational and financial performance information is likely supporting more rapid and precise decision making that is needed to achieve these additional product cost improvements.
As shown in the box plot, the LNS Research MOM survey uncovered the fact that companies that have implemented EMI software solutions are experiencing 7.2% higher OEE performance than those who have not. The average OEE for those who have EMI solutions in place was 74, versus 69 for those who do not.
This relationship also stands to reason, since we have seen many real-world examples whereby the consistent calculation and visibility of OEE metrics is enabling engineering, manufacturing and maintenance teams to continuously monitor and incrementally improve OEE.
What Should My Company Be Doing In Regard To This?
Given the maturity of the technology, documented end-user case studies, and results of quantifiable research from LNS Research and MESA, we can confidently state that EMI software solutions and associated analytics are now well-proven to play a crucial role in bringing together real-time performance information to assist in significant operational and financial metrics improvements.
We suggest that if you have yet to deploy EMI software, then you should rapidly get underway with doing so. The eBook research report Getting Started with EMI provides a great step-by-step guide for taking this journey.
Since our research also showed that the use of analytics and Big Data analytics is almost doubling over the next year, it is also a good time to start experimenting with the associated use of Big Data analytics.
Last but not least, in order to best achieve your manufacturing performance improvement objectives, it is imperative that you not only focus on these supporting new technologies, it’s important to also align your organization’s key resources: people and processes, along with your technology strategy.
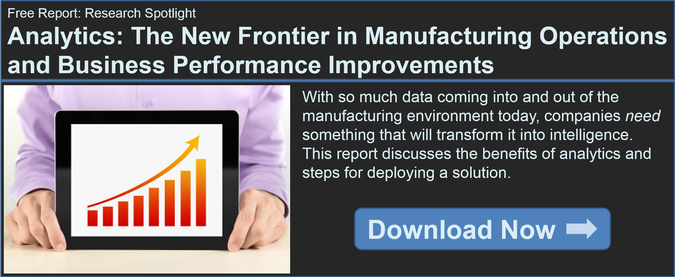