In a manufacturing organization, understanding what’s happening at the plant level is crucial because it’s where the rubber really hits the road. Having visibility into shop-floor operations is important for achieving several company goals, like meeting customer demands, identifying lagging assets, and reducing manufacturing costs.
This may be simple enough if your company only has one manufacturing plant, but what if yours is an organization with facilities dotting the globe? How do you ensure that your assets are performing effectively and efficiently across the enterprise? And how do you make sure your people are armed with the best possible information to perform their jobs?
One way that leading manufacturing organizations have been improving manufacturing operations is through the use of Enterprise Manufacturing Intelligence (EMI)/Operations Intelligence (OI) software, which has been a critical tool in improving operations visibility and facilitating decision-making.
In this post, we’ll take a look at the profound effect that EMI software functionality has had on manufacturing operations since its initial adoption over the past 10 to 15 years, as well as how emerging technological trends will advance its benefits.
The Manufacturing World Before EMI Software
In the last century, plant manufacturing data has been collected at the local level using paper-based methods, making enterprise-level comparisons extremely laborious and time consuming. Any decisions informed by these manual analyses needed to factor in the significant lag time inherent to this process to be effective.
Typically, C-level executives didn’t have visibility into shop-floor level information either. And since each plant or production facility was essentially a silo unto itself, decisions about Manufacturing Operations Management (MOM) functionalities tended to be made at the plant level as well, resulting in many disparate decisions, processes and systems across an enterprise.
The advent of EMI functionality in the early 2000s changed all of this, and rapidly made manual enterprise data comparisons obsolete, in effect transforming manufacturing operations forever.
EMI software functionality enables real-time visibility into plant-level data across disparate sources and provides context on the interrelationships of data that may be less than obvious due to being stored in different equipment, systems, applications, or databases.
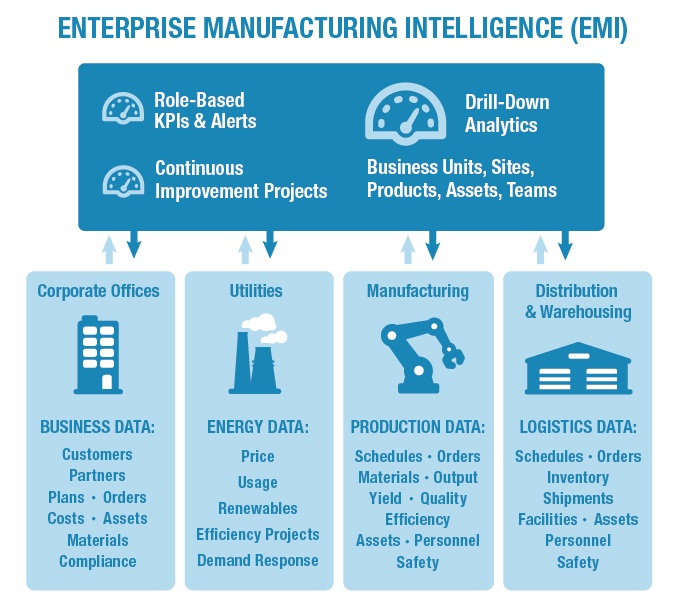
How EMI has Affected Manufacturing Floor Operations and Decision-Making
Since its early millennial inception, EMI software has been a crucial tool organizations have been using to gain immediate and actionable intelligence at the shop-floor, as well as enterprise levels. For the first time, executives were armed with the same data as operators and plant managers. This real-time data visibility across roles and departments has greatly improved decision-making speed and abilities.
EMI software’s ability to integrate and contextualize data from different systems and data sources, and provide real-time actionable data has also been a quantum leap in manufacturing intelligence capabilities across the enterprise compared to the days of manual collection and analysis.
And these benefits still speak to many of the operational challenges manufacturing companies faces today. In our 2013 Manufacturing Operations Management survey, we've asked over 250 manufacturing executives and decision-makers a wide variety of questions that get to the heart of their goals and challenges.
In one question we asked respondents what their top three operational challenges were for meeting manufacturing objectives. As you can see, lack of collaboration (16%) and the existence of disparate systems (14%) and data sources are operational challenges that are top-of-mind among manufacturers today.
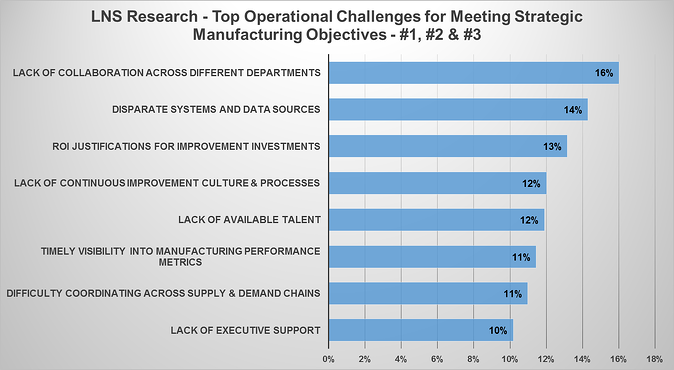
As a pivotal source of shop-floor information, EMI software has an integral role within a manufacturing organization, and some of the larger trends seen in the enterprise software space, including Big Data, Cloud, and Mobile functionalities are proving to have a significant effect on the reach of EMI and its capabilities. Mobile technologies, in particular, are already removing the tether of on-site displays by enabling shop-floor visibility from any mobile device rather than solely on on-site dashboards and displays. This means all job roles can now access real-time shop-floor information and alerts from any location on their device of choice, drastically improving time to response for adverse events and streamlining decision-making abilities.
Cloud/Software as a Service (SaaS) capabilities are also rapidly emerging, and bringing with them the promise of automatic software updates, unlimited capacity upgrades, built-in disaster recovery, and universal remote access capabilities. Understandably, data security is still a prime concern, but vendors are making great strides to address this and other reservations around the cloud.
As Big Data capabilities advance, EMI solutions will be able to mine increasing amounts of data at lightning speed, uncovering previously unknown correlations between systems. The pulse of enterprise operations will be measurable at scope expansive in reach and precision, including unprecedented predictive maintenance capabilities for shop-floor assets, creating the ultimate "smart" shop-floor for manufacturing operations.
LNS Research Performance Management Library
EMI software is just one tool manufacturing companies are leveraging to gain visibility and manage enterprise performance. Effectively managing performance requires optimizing an organization's key resources—people, processes, and technology—to achieve new levels of operational success. To learn more about the technologies and strategies companies are employing to drive operational improvements, read The Pursuit of Performance Excellence.