Until recently, manufacturing operations management (MOM) software and Industrial Internet of Things (IIoT) platforms were two distinct solutions serving different purposes and providing separate capabilities. That’s no longer the case. MOM software vendors today embed several IIoT capabilities that enable the applications to run at any level in the operational structure. This new degree of connectivity, together with smart connected devices and inexpensive sensors have enabled manufacturers to replace older, monolithic MOM solutions with IIoT-based MOM applications in the plant.
In his research on the “seven lives of MOM,” LNS Research Principal Analyst Andrew Hughes explained that as companies get access to more data through inexpensive sensors and modern devices, industrial organizations should define new rules of play. The fourth industrial revolution changed the game where manufacturing software is concerned, and industrial executives need to educate themselves on newer guidelines that affect their options and choices when it comes to MOM applications in today’s IIoT world.
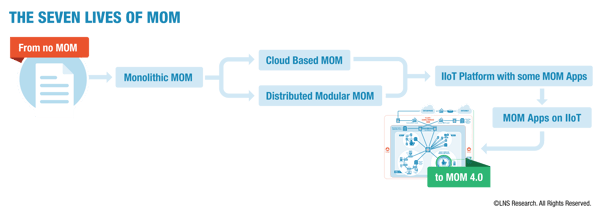
New Standards, New Data Connections, New Ways of Using ISA-95
The way we use ISA-95 in control design changes as new standards emerge, and with new data connections. Consider this: most industrial devices now come labeled “smart,” and we expect them to capture a variety of data. Add to that inexpensive sensors capturing more data still. Ultimately, companies will need to come up with new ways to connect this massive amount of data suddenly available to them. Industrial organizations that have started an Industrial Transformation initiative will face many scenarios where enterprise systems like ERP need data from the smart devices on the shop floor, and MOM/MES applications require access to enterprise data, or sometimes even data from outside the enterprise.
Most manufacturers already use the ISA-95 enterprise architecture framework to design their software systems or when selecting new ones. ISA-95 is continuously developed to remain relevant, and it will remain a useful tool as engineers define control hierarchy.
However, as new IIoT and smart connected operations and assets emerge, companies will need a less hierarchical and more peer-to-peer model that enables next-generation systems to communicate with widespread systems, and to automate high-volume data collection.
Cloud-to-Edge Computing Makes Analytics Omnipresent
An ever-increasing number of MOM solutions offer capabilities to collect, store, and perform analytics on data – all in the Cloud. These advancements have led to a significant improvement in data backup, redundancy, and accuracy, and accessibility; data stored in the Cloud can be accessible at any level throughout the organization. However, a good number of cautious manufacturers remain skeptical about storing manufacturing data (particularly control data) outside on-premise SCADA and MES systems. Software vendors are aware of this skepticism and have put cyber-security at the top of their agenda. Working with third-party cloud providers who are ahead of the curve will certainly help make data storing, processing, and analyzing more secure. Cloud computing thus offers numerous ways to connect data that was originally sitting on disparate systems, and enables manufacturers to reap industrial transformation fruits.
That does not mean cloud is the way forward in all cases; the time to send data up to and down from the Cloud might be relatively slow for some use cases where the business needs real-time insight. On-premise data centers, both at enterprise and plant level provide computing power where it is needed to avoid latency, availability, security and other issues. Edge devices take this a step further and perform real-time analytics all the way down within the device itself. Taking the time to plan and establish an Operational Architecture that supports Cloud-to-Edge computing will help the industrial organization enable analytics at multiple levels throughout the organization, and thus give the company a leg up towards Operational Excellence.
2-for-1 Tech: Robust Mobile Devices Attract Next Gen Workforce, Enable Industrial Transformation
The latest research says that by 2019, Generation Z will make up 32% of the earth’s population, edging out millennials at 31.5%. Gen Z individuals were born in the 21st century and grew up in a digital world. This generation and the younger set of millennials have always had everything at their fingertips – starting with robust mobile devices equipped with high-speed wireless Internet. As these individuals replace previous generations in manufacturing jobs, they won’t’ be comfortable working in plants that have decade-old PCs still running Windows XP.
Manufacturing companies must take steps to digitalize plants and provide a suitable workplace for the younger generation. Manual paper-based calculations or hundreds of spreadsheets sitting on SharePoint sites will certainly discourage and frustrate Gen Z; it will also prevent the organization from nurturing a digital workforce culture. Together these gaps will hinder Industrial Transformation.
Decentralized Control Paves the Way for IIoT-Based MOM
The manufacturing world has for many years revolved around enterprise-centric systems with a centralized mode of control based on a structured hierarchy. Today’s industrial revolution enables data collection, processing, and analysis from limitless numbers, sources, and types of systems, devices, sensors, including unstructured data (audio, video, image, geospatial) from outside the enterprise. IIoT applications that cash in on this abundance of data catapult manufacturers toward a highly collaborative organization. LNS Research believes that it will do so much more; that the application-based MOM culture will really take manufacturing to the next level when the business invites third parties into the game.
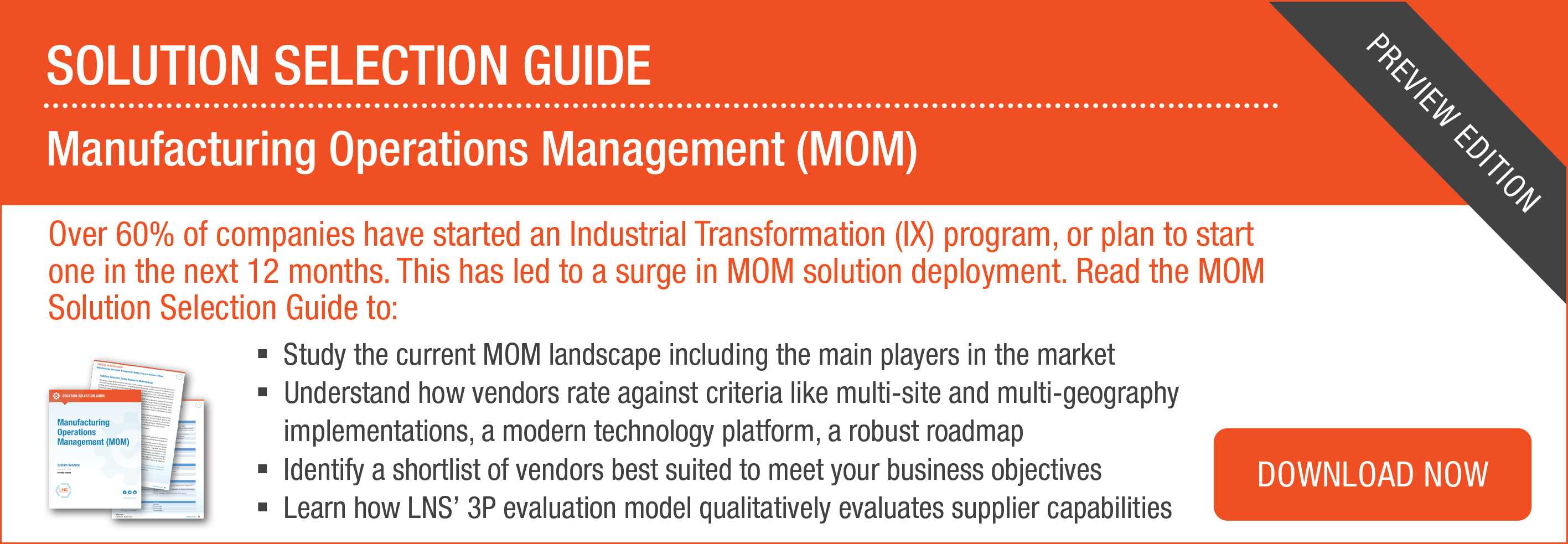