Human Resources have deployed Learning Management Systems at the corporate back office level over the years, this has resulted in Quality becoming disconnected from training activities.
Employee turnover has cost impacts, quality impacts, and productivity impacts in an organization so manufacturing operations have a stake in training and qualification.
Additional gaps have emerged because those corporate systems are not good at managing qualifications for the front-line workforce. The space has become fragmented, with each company entity running its work training its own way and tracking it on spreadsheets.
Worker training and qualification have been hot potato issues for quite a while. Training resides in various parts of a company's organization depending on the company and its culture. There is no clear “owner” for training and qualification processes.
Current State of Play
The labor market is strained by a combination of factors at the moment which is inevitably contributing to the creation of a much larger issue.
-
-
-
“The Great Resignation” or workforce migration to different work experiences.
-
The myth of untold numbers of workers sitting at home and burning through stimulus funds (BLS Statistics show less than 100,000 people nationally have exited the job market and are not looking for work in the last full year of reporting, 2021).
-
Entry into the workforce of “Digital Natives” of the Millennial and more so Gen-Z.
-
This pressure is coupled with statistical full employment.
-
The tension of the possibility of a coming recession.
The employment market is experiencing push-and-pull tensions like no time in the past. 78% of respondents to NAM’s Manufacturers Outlook Survey for the 2nd Quarter of 2022 report that attracting and retaining a quality workforce is a top challenge. The major force at work here is an aging industrial workforce that is rapidly retiring, with valuable skills, experience, and institutional knowledge being lost.
All of these challenges are contributing to a large amount of employee turnover within the manufacturing workforce. However, our research on the Connected Frontline Workforce (CFW) shows that only 22% of respondents are utilizing CFW applications to deliver training to the workforce.
What the Future Holds
All of this is a preamble to the dark cloud on the horizon. The great retirement is the exit of the labor pool of the last of the Baby Boomer and Gen-X generations. This will happen over the next 7-10 years. As of 2021, the industrial labor force was made up of;
-
-
-
Baby Boomer Generation: 25% of the workforce
-
Gen-Xers: 33% of the workforce
-
Millennials: 35% of the workforce
-
Gen-Z: 5% of the workforce
By 2030, Millennials will make up 75% of the workforce as Gen X and the last of the Baby Boomers exit.
Demographically, Millennials and Gen-Z don’t prefer factory work. As a result, the available labor pool for a manufacturer is a subset of a subset of a shrinking population.
Generational turnover is normal and natural. The difference now is Digital Natives. Digital Natives are people who grew up with technology and are very comfortable with it and see the value in utilizing technology to help make their work easier to accomplish.
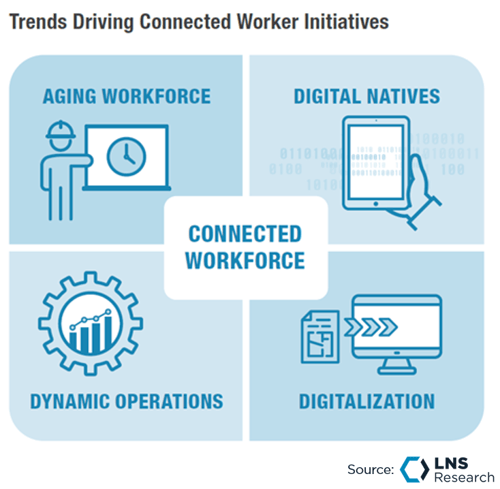
The latest Connected Frontline Workforce research shows that Leaders are doing more than Followers in the areas of Workforce Collaboration and Training (120% and 42% more respectively), and that in-context/micro training use cases are amongst the most favorable on the effort to benefit ratio. These ratios will only become more favorable in the future.
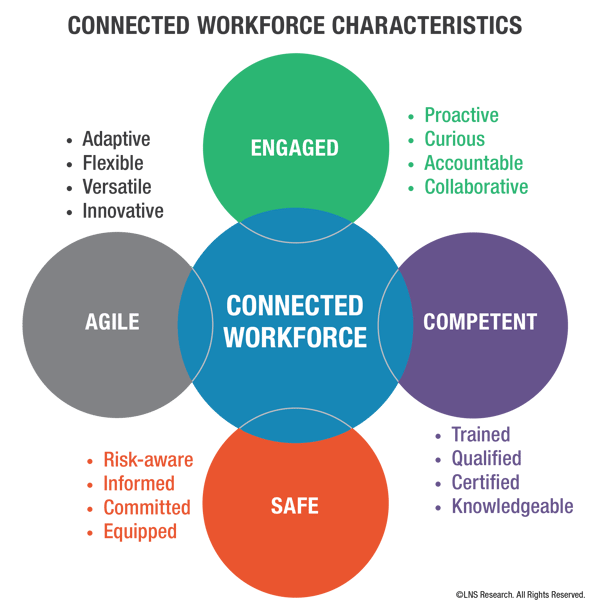
As Gen-Xers and Boomers retire over the next 7-10 years, replacing them with Digital Natives will require new training approaches to bridge the knowledge and skill gap. Currently, we have many “micro-training” platforms deployed in the industry. Training is immediate and geared towards helping the trainee succeed. Enter the opportunity for advanced digital solutions, to do better, i.e. in-context micro-training and integrated into the overall production management system and technology architecture. Our upcoming Future of Industrial Work research will focus on this area as well as ways to become the “Employer of Choice” to cut down on turnover.
How to Bridge the Gap
With fewer expert people in the workforce after 2030, training and qualifying new workers will become more challenging than it is today. AI-driven training and qualification is the solution and the future of training. AI is being applied to a variety of simple to complex problems in industrial settings. Delivering insights about the best way to answer a customer complaint to the best way to run a production line to deliver the best quality, highest productivity, and lowest cost.
Figure 1
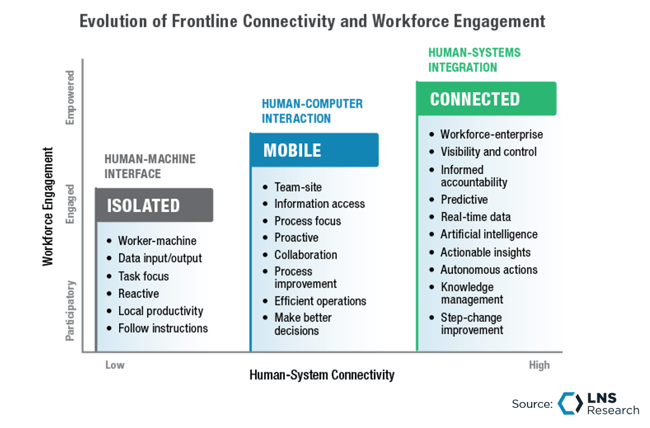
Emerging Connected Frontline Workforce applications incorporate the delivery of micro-training, with IIoT machine connectivity, and Augmented Reality and Virtual Reality capabilities derived from Digital Twins or Natural Language Processing AI. This combination of capabilities is moving closer to the Connected Workforce characteristics defined in Figure 1 above.
The library of insights is being built day by day. It’s a natural next step to turn those insights around and use them as an instruction to teach new personnel the “best” way to perform their job tasks to succeed and to evaluate performance to determine if a person is “qualified” to do a given job.
This AI-driven tracking of qualifications can have real-world implications for day-to-day operations management when AI can identify what work can be done based on who shows up that day and what they are qualified to do.
Recommendations
As the old Chinese proverb says; “The best time to plant a tree is 20 years ago, but the second best time is now.” Knowledge libraries of identified best practices are being filled today from various analytical techniques being applied to large datasets of manufacturing and Quality data.
-
-
- Start experimenting with those best practices now to determine the ideal way to deploy best practices as training prompts and qualification standards through a Connected Frontline Workforce application.
- Leverage the experience and talent of Baby Boomers and Gen-Xers before they walk out the door to populate and validate those AI-Driven routines.

All entries in this Industrial Transformation blog represent the opinions of the authors based on their industry experience and their view of the information collected using the methods described in our Research Integrity. All product and company names are trademarks™ or registered® trademarks of their respective holders. Use of them does not imply any affiliation with or endorsement by them.