In our recent eBook introducing research on the factory of the future (FoF), we show that the factory itself will be a hotbed of innovation and a key provider of vital information to help drive Industrial Transformation (IX). The three pillars of IX—people, process and technology—are all vital to success, but today we discuss the pillar that is probably the most important factor that will determine whether the FoF will deliver its promise or not: people.
There are many aspects of IX that affect people, from leadership to those working in the plant. Leadership is key to every IX program; the first test you should do for your own program is to estimate the commitment and involvement of top management. Who is the official sponsor? Has funding been approved for initial pilots and recruitment? Who turns up to steering committee meetings? Are there steering committee meetings? What mentions of your IX program are there outside the enterprise (In annual reports for example)? If you cannot answer these questions satisfactorily, IX effort probably needs to be re-focused before you move on.
When top level leadership and sponsorship is in place, the next key for FoF is to build a team that can work with the wider IX (and perhaps even enterprise-wide digital transformation) team to research, define and build the first of our factories of the future. Early interaction between IT, OT and business needs to ensure everyone is using the same language. It is inevitable that past experience will mean that everyone takes a slightly different viewpoint on how a FoF should be managed and how the technology will support it.
Data is a Starting Point
One of the key touch points between factory of the future (FoF) and the rest of the digitised enterprise is data. FoF is a major generator and consumer of data to and from many sources and much factory data will be used in the enterprise as businesses are transformed. Defining a data architecture that everyone can work with is a key early stage task in any Industrial Transformation (IX) program. Discussing the architecture is way beyond this post, but it is an example of the need to have the same understanding about technology. A good example is “edge storage” that is a level of storage somewhere between the pure cloud and smart devices on the shop floor. An IT professional may see edge as everything in the plant while a pump maker might see the edge at the interface to his pumps. Everything above the edge can migrate to the cloud but edge computing is required in the plant. Getting an understanding of what that means is critical for a proper understanding between the FoF and IX technical leads and users.
No one role from IT and OT can hope to be able to define a complete data architecture as the scope of systems that will communicate is enormous. What is required for the IX team and its FoF subsidiary is to provide an environment for the changing workforce.
Changing Workforce
Probably the most talked about aspect of people in IX is the changing workforce. It is coincidental that the baby boomers are ending their careers just at the point of enormous technological change, and it certainly adds a level of difficulty to the implementation of FoF. Automation and other newer technologies will mean the loss of some mundane jobs. However, the opportunities to change how we run our factories can be enhanced by a new workforce, digital natives, with a totally different set of capabilities, expectations and desires.
The connected worker will be one of the main contributors to increased agility, productivity and quality in the FoF, bringing together traditional factory technology with modern mobile devices, augmented reality, wearable technology and many other new factory-based technology. By demonstrating their commitment to new technology, manufacturers will demonstrate to their potential employees that they are an interesting place to work. Candidates will be able to see for themselves that factory jobs are no longer filled by “blue collar” workers, but will be places where you can have influence, develop your own ideas through systems such as no code app configurators, and generally be much more valuable contributors to success. The idea that frontline workers are somehow less valuable and less smart than others in the enterprise will finally be put to rest.
The Factory of the Future is an exciting part of the wider Industrial Transformation (IX) program that is so vital to future success of most manufacturers. The best part of it is that everyone should be involved—from C-level through IX leadership to the factory based connected worker.
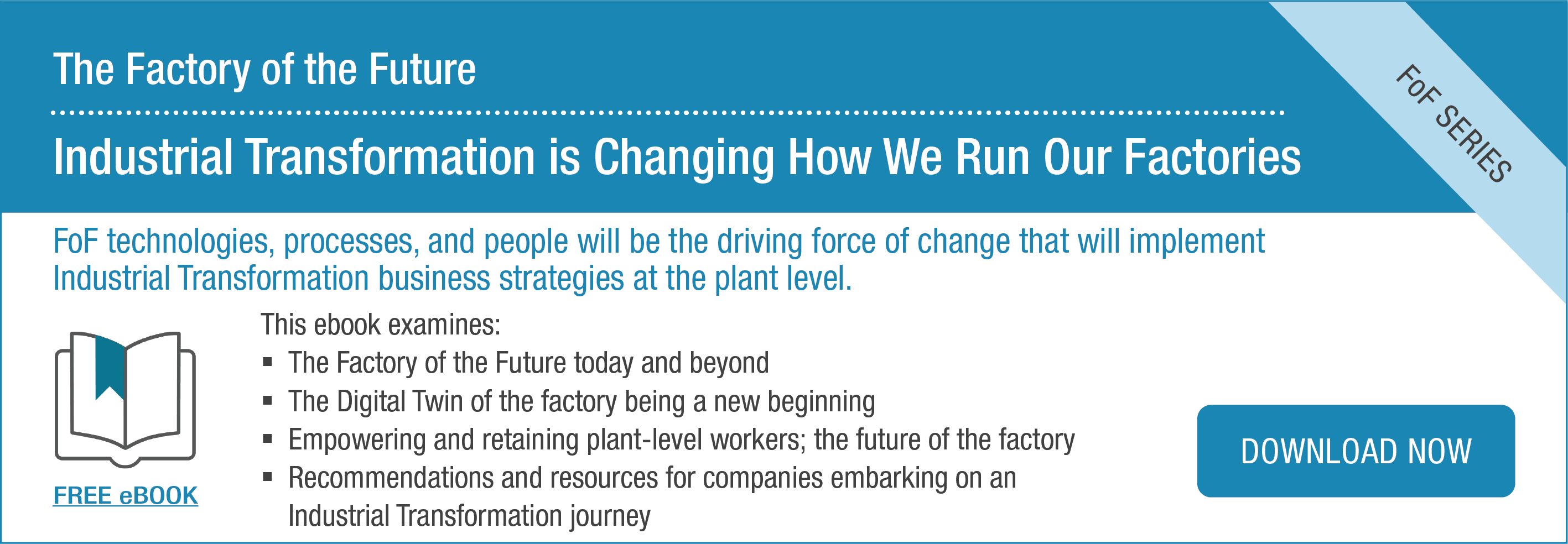