...And Unlock Next-Level Business Value
It’s no longer a question of if you should invest in Connected Frontline Workforce (CFW) initiatives—but how to do it effectively and unlock meaningful business value. Many companies have already shown what’s possible. In fact, LNS Research data reveals that the top 22% of manufacturers — those we call Leaders — are using CFW to drive real impact across their organizations.
Now, manufacturing executives throughout industry are under pressure to replicate that success. While the benefits of CFW are no longer limited to early adopters, too many initiatives still fall short of expectations.
In this blog, I’ll explore why Connected Frontline Worker (CFW) applications are no longer optional — they’re a must-have to achieve meaningful operational impact. I’ll also share key insights to help manufacturing executives sidestep the common pitfalls that have hindered others on their connected workforce journey.
Figure 1: CFW initiatives are needed in manufacturing
The Power of a Persona-based Interface
Leaders have shifted their approach to leveraging digital technologies with CFW initiatives, creating impactful outcomes across the organization, and pulling significantly ahead of Followers who often struggle to get beyond the definitional and pilot phase. More than 50% of Leaders have adopted CFW applications across the enterprise that provide in-context/micro learning, real-time data, and decision support, along with contextualized, tailored content (Figure 2) to enable employees to respond better to changing conditions.
Figure 2: Leaders leverage CFW capabilities to enable
better, faster decision-making across the enterprise
CFW applications are empowering Leaders to protect workers, boost productivity, and break down organizational silos by delivering timely, AI-powered insights tailored to each role and task.
Here are just a few examples of how CFW applications and the power of a persona-based interface are transforming work to drive step change improvements:
- Chief Operations Officers (COOs) & Executive Leadership: AI-driven analytics identify vulnerabilities across the operations network to maximize profitability by reducing risks with standardized content to all sites for best safety, quality, and productivity practices, with opportunities.
- Operations & Plant Managers: Align production with business goals with real-time data, aggregated workforce performance, machine uptime, and quality metrics across multiple plants, which provides insights to adjust production schedules and optimize resource allocation.
- EHS & Quality Control Managers: Mitigate workplace hazards faster and enhance product quality with intuitive tools. These tools enable workers to report safety concerns or defects instantly and analyze trends with AI to identify suggested improvements.
- Shift Supervisors & Team Leaders: Provide automated notices when skills gaps are detected, with prioritized recommendations to quickly reassign tasks in real time to maintain safety and production efficiency.
- Operators, Maintenance Technicians & Reliability Engineers: Become proficient faster with role-specific, interactive training modules that feature AI-powered safety alerts and notifications of process deviations, providing up-to-date guidance instantly at the point of work.
As a proven value enabler, persona-based CFW applications are powerful digital tools for CFW initiatives and are essential for modern manufacturing.
Executing CFW Initiatives that Maximize Business Value
CFW initiatives are strategic enablers for Leaders driving step-change improvements across operations and business metrics. But Leaders aren’t just widely deploying CFW applications across the enterprise — they have taken a new approach to digital transformation and are prioritizing solutions that build leadership capabilities to better support teams across the organization.
As CFW applications evolve with emerging technologies, a clear strategy is essential to execute efficiently and achieve better results, faster. Manufacturers should be mindful of the following to create CFW initiatives that deliver step change improvements:
-
Don’t use CFW initiatives to just solve problems; build new operating systems.
Develop a holistic strategy that builds an operating system to provide proven solutions for engaging, empowering, and elevating employees at any level to excel in the future. COOs who prioritize improved training and development across the entire organization with CFW initiatives as a strategic enabler are accelerating safety and quality improvements across the value chain. Focusing on business growth and workforce development often drives improved adoption and better, faster ROI.
Organizations are moving toward creating new roles at the VP and Director level to execute the workforce development strategy. With manufacturers across industry taking this approach, including Dow and Archer Daniels Midland (ADM), we expect this will be the organizational model necessary for modern manufacturing.
-
Avoid over-indexing on technology with a weak infrastructure. Connectivity gaps, poor data integration, and outdated architectures will prevent even the best CFW applications from delivering a strong ROI. A common pitfall is prioritizing mobile solutions without ensuring a robust infrastructure.
Architecture and infrastructure are critical to ensure a good user experience, which accelerates the adoption and scale of solutions. Operations must partner with IT to ensure pervasive wireless, data governance, and an agile approach is focused on creating seamless solutions. Companies such as Pfizer and The Cooley Group found data and architecture foundational to ensure users have real-time in-context data and information at the point of work to improve productivity.
-
Learn how to separate “Connected Worker” solutions from CFW Applications. Many software providers can help provide digital work instructions, deliver mobile applications, or even digitize operations. Robust CFW applications provide the total package manufacturers need to protect people, improve sustainability performance, and maximize the return on investment.
Invest in LNS Research-defined CFW applications to provide a wide range of use cases beyond checklists and collaboration, mature organizational capabilities with work executive support, training and development, and self-service analytics tools for continuous improvement. Owens Corning and International Paper are examples of companies focused on proven, role-specific, and scalable solutions to improve knowledge management across the manufacturing network to collaboratively drive safety, quality, and reliability improvements.
Recommendations Moving Forward
As digital expectations evolve, manufacturers can no longer treat technology as a differentiator but as a necessity for survival. This shift demands that COOs rethink their approach to CFW initiatives — not just as a digital upgrade, but as a fundamental enabler of workforce effectiveness and business growth. Leaders have widely deployed CFW application capabilities, providing a seamless, persona-based interface to workers across the organization to support safe work execution and enhance decision intelligence to collaboratively drive step-change safety, quality, and productivity improvements.
COOs who will succeed are those investing in persona-based CFW applications to build organizational capabilities that will sustain operational success while reinventing the business model to enhance operational agility for ensuring long-term profitable operations.
Ready to unlock the full potential of CFW initiatives? Benchmark the success of an LNS Research Pathfinder by listening to a 2024 The IX Event keynote from AstraZeneca’s Senior Vice President of Americas Supply Chain, who engaged the workforce in a whole new way to drive measurable results.
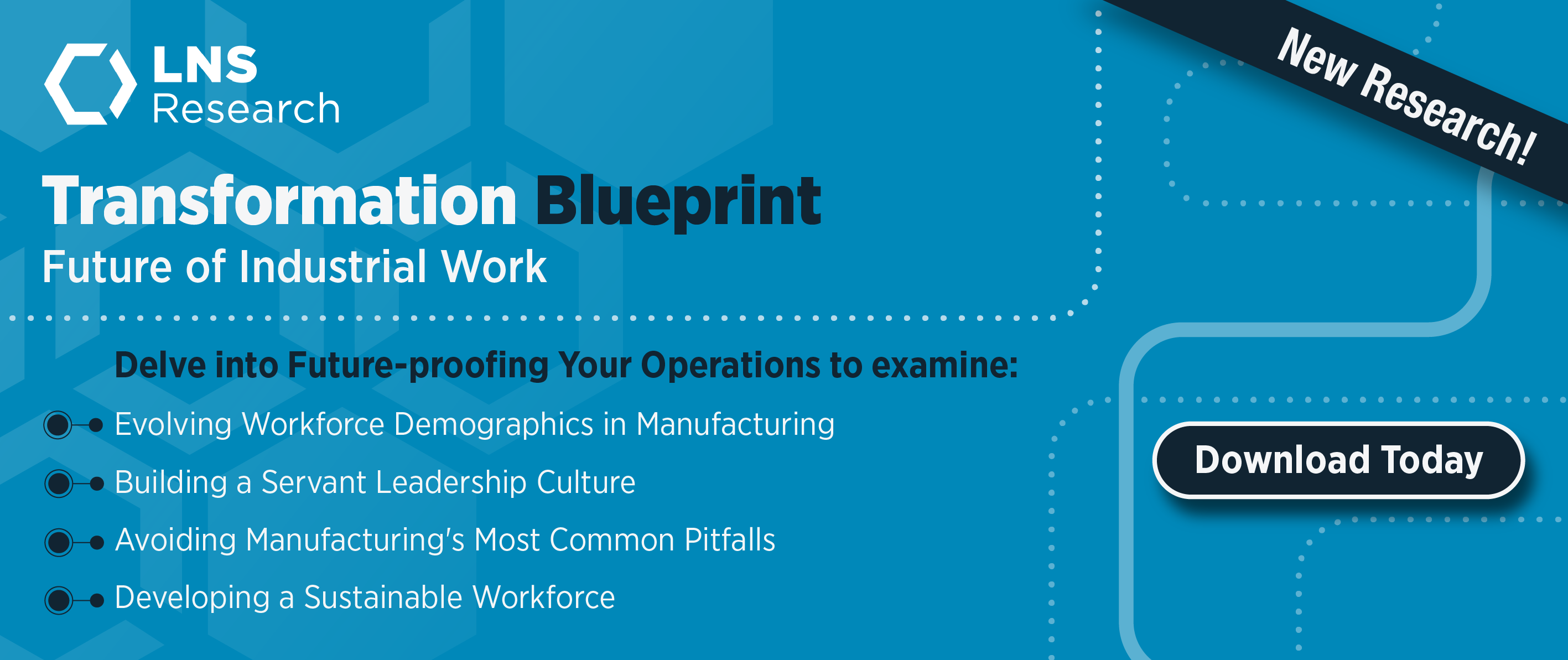