What is Unified Performance Excellence?
Unified Performance Excellence (UPX) is how the world's most successful manufacturers are reinventing Continuous Improvement (CI) programs and management systems. They are taking advantage of digital and AI toolkits and new approaches to innovation and transformation to drive significant gains across safety, quality, emissions, and productivity.
UPX transforms traditional CI management systems from a policy and procedure-driven manual activity, where people are the glue holding the program together, to a holistic, digitally embedded approach encompassing all aspects of operational agility, flexibility, and resiliency.
Traditional CI management systems are plagued with struggles to overcome organizational inertia.
Traditional CI management systems rely solely on people to hold the system together, enforce process discipline and tool usage, and make the program go, in addition to getting the results. As a result, workforce turnover and new leadership priorities can result in serious momentum losses, a defining characteristic of traditional CI management systems. In our research on UPX, LNS Research found that 75% of manufacturers reported losing momentum in their efforts to scale their Performance Excellence initiative (Figure 1).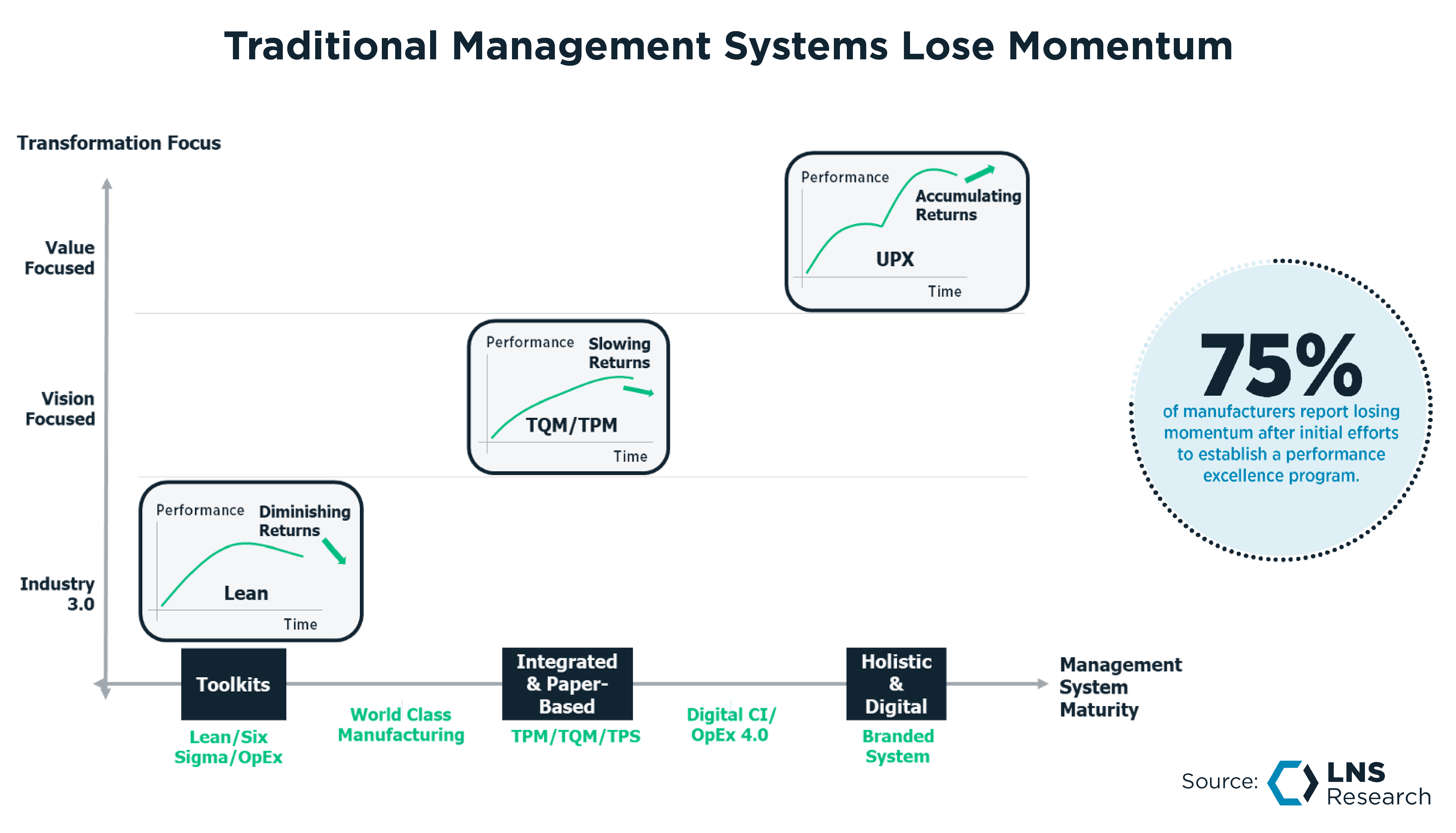
Figure 1: Traditional CI Characterized by Loss of Momentum
Why change now? Two primary reasons...
First, the cloud, digital, and now the AI revolution has been underway for over a decade. Yes, there will always be new technology that needs to have its true utility and business cases proven; we can throw Generative AI in this bucket for now. But that doesn’t apply to much of the Industrial Technology landscape. Cloud, IIoT, Vision Systems, Augmented Reality, NLP, Anomaly Detection, Digital Twins, Industrial Data Platforms, Advanced Industrial Analytics, and Connected Frontline Workforce (CFW) Applications are all mature and well-proven technologies that can add immediate value to traditional CI and management system approaches.
Second, the workforce’s makeup and expectations in manufacturing have dramatically changed over the past 10 years. The time when most frontline workers worked for 30 years or more at a company is gone and not coming back. For many companies, the reality has changed from 30-year employees to three (or less) years. And with that change has come the realization that traditional approaches to CI and management systems were almost entirely dependent on these tenured veterans.
How can different personas utilize what Unified Performance Excellence offers?
Heads of Global Operations:
Many manufacturing leaders struggle to get out of the day-to-day operations and find the time to think strategically, plan for the long term, and balance the business cases for sustaining today’s assets and investing in tomorrow’s future.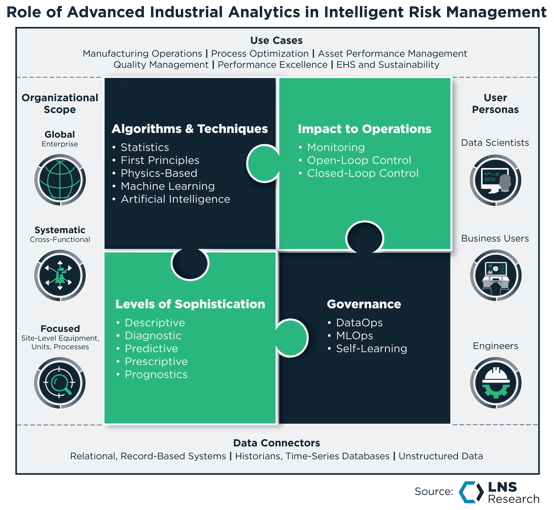
Figure 2: Analytics Landscape
Many supply chain leaders have developed either S&OP or IBP control towers to help address these concerns. Operations leaders need to do the same; an interactive, real-time management cockpit with embedded risk management can:
-
-
-
See the next crisis coming.
-
Develop strategies to mitigate or prevent risks from being realized.
-
Coordinate their teams more effectively.
Heads of Global Operations can leverage Advanced Industrial Analytics (Figure 2) in a flexible, composable platform to build their own unique risk frameworks from pre-existing pockets of risk thinking across the company. When connected to real-time data, these frameworks become the “early warning system” of potential impacts on agility, flexibility, and resiliency in manufacturing operations.
Performance Excellence Leaders:
In the “human glue” era of traditional CI management systems CI program leaders had several worries keeping them up at night.
-
-
-
Retaining expert practitioners.
-
Enforcing the process and tool usage disciplines associated with the preferred approach.
-
Running constant cycles of training, coaching, evaluating, communicating, building momentum, and reprioritizing, only to do it all over again.
-
Engaging the workforce in improving their work with guardrails.
Leveraging in-house expertise to build the tools and processes into a flexible, composable platform, such as a Connected Frontline Workforce Application, bakes in some level of process knowledge. An aspect of traditional manufacturing-focused CI systems has been the engagement of the frontline worker in improving their own work. Performance Excellence leaders can leverage Advanced Industrial Analytics and Digital Twins to upend conventional wisdom about the relationship between industrial digital architecture and improving processes before digitization.
Manufacturing Plant Leaders:
Leading at the plant level has no shortage of challenges or pressures, and these leaders desperately need help making performance transparent and building the guardrails of decision-making in the workforce. They also need help empowering the workforce to improve their own work and rely less on the chain of command to tell them what to do and how to respond. Plant leaders want a single source of near-real-time truth about how their plant is performing that can drive an ownership culture in their plant teams. These needs correlate well with the new generation of workers' desires for autonomy and a sense of ownership of their own work. Those who can do this well have lines out their doors of people wanting to work for them.
Shop Floor Workers:
As workers are tasked with more varied work, they need lots of help and guidance. As average experience levels tumble and workers are asked to do more varied kinds of work, demands for guided operations increase.
Like any other industry worker, manufacturing frontline workers start life motivated to succeed. They want to be part of something successful that they can be proud to be associated with, part of a cohesive team, coached on their journey to competency, grow into more prominent roles over time, and become leaders. They just need the right approach and technology to be successful. UPX provides that approach, and Connected Frontline Workforce Applications (Figure 3) offer the technology by:
-
-
-
Empowering workers to improve their own work within the guardrails of the company’s criteria.
-
Lowering the bar of ‘special knowledge” necessary to participate in improvement activities by standardizing the knowledge elements by baking them into digital process workflows and toolsets.
-
Building decision-making understanding within the context of what’s important at their plant, removing the mystery about how decisions are made, and priorities are determined.
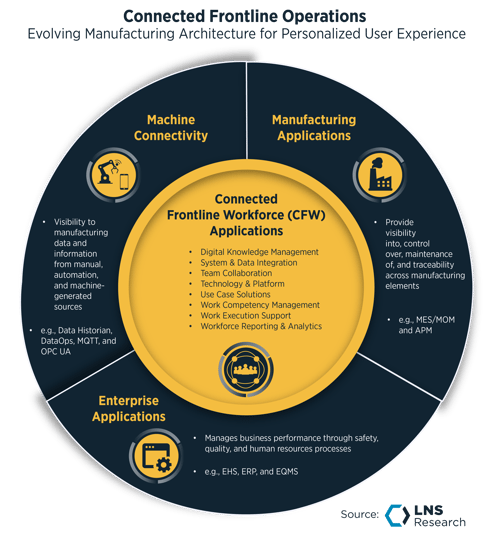
Figure 3: Connected Frontline Workforce Capabilities
Recommendations for Manufacturers
-
Identify a champion for UPX. Performance Excellence leaders seeking to develop their digital Performance Excellence platform must first identify a sponsor with P&L responsibility who is willing to support the approach. Achieving results earns you a license to scale the approach across the plant network.
-
Pull together existing pockets of risk thinking to build your unique frameworks that reflect your specific variables and tolerance levels for risk and how, if realized, it impacts your operations to finally get ahead of threats to agility, flexibility, and resiliency in industrial operations.
-
Engage the shop floor workforce in improving their own work. Frontline worker engagement is a philosophical value of manufacturing-focused improvement efforts. Lean and Six Sigma to Toyota Product Systems and World Class Manufacturing approaches all place a high value on the frontline worker. In traditional CI management systems, this value is hard to achieve in the real world of manufacturing. It is now achievable through a connected, holistic, digitally embedded approach that engages workers through a Connected Frontline Workforce Application interface.
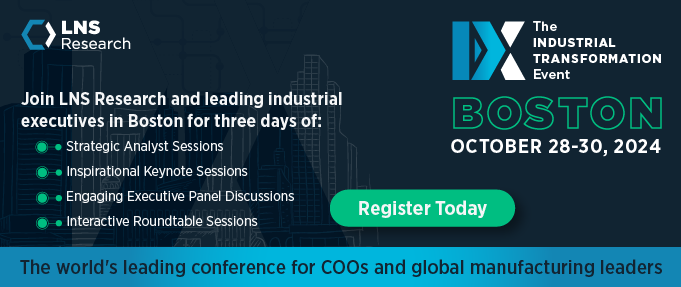