Traditional Continuous Improvement toolkits and supporting management systems in the Industry 3.0 world are people, policy, and procedure-centric processes. One characteristic they have in common is that high effort initially produces performance gains. Still, over time, gains diminish even with additional effort applied. In the manual process era, there are several “headwinds” that organizations experience in their journey to improved performance from industrial operations:
-
-
-
Special knowledge
-
Turnover of those with special knowledge
-
Long project cycle times
-
Project failure
-
Long wait time for results
-
Rapidly shifting priorities
Traditional approaches to continuous improvement rely heavily on the toolkit and supporting management systems approach. These include:
These traditional programs are characterized by the arch of early gains and enthusiasm for the process and results, building momentum, gaining practitioners, and spreading across the organization.
To a tipping point, where momentum and results slow, even despite an infusion of new energy. This is a common characteristic across people, policy, and procedure-based systems with little to no infrastructure to support the program except people’s personal discipline. (Figure 1)
Figure 1
In our UPX research, 75% of organizations reported a loss of momentum in their programs, with the top challenge to scaling being the turnover of trained practitioners. (Figure 2)
Figure 2: Seventy-five percent report a loss of momentum
Why Digital?
Digitizing the toolset and processes within the Industrial Transformation architecture and layering on Intelligent Risk Management has several benefits.
-
-
-
Speeds time to results through the application of advanced digital tools to problems
-
Lowers the special knowledge requirement
-
Gains insight into shifting priorities before its too late
-
Lowers the impact of turnover of specially trained personnel
-
Ensures priorities are correct
What is Unified Performance Excellence?
Unified Performance Excellence (UPX) expands and digitizes traditional management systems, adding an Intelligent Risk Management overlay. UPX brings together incremental improvement and step-change transformation processes across the value chain into a common integrated approach focused on maximizing operational agility, flexibility, and resiliency.
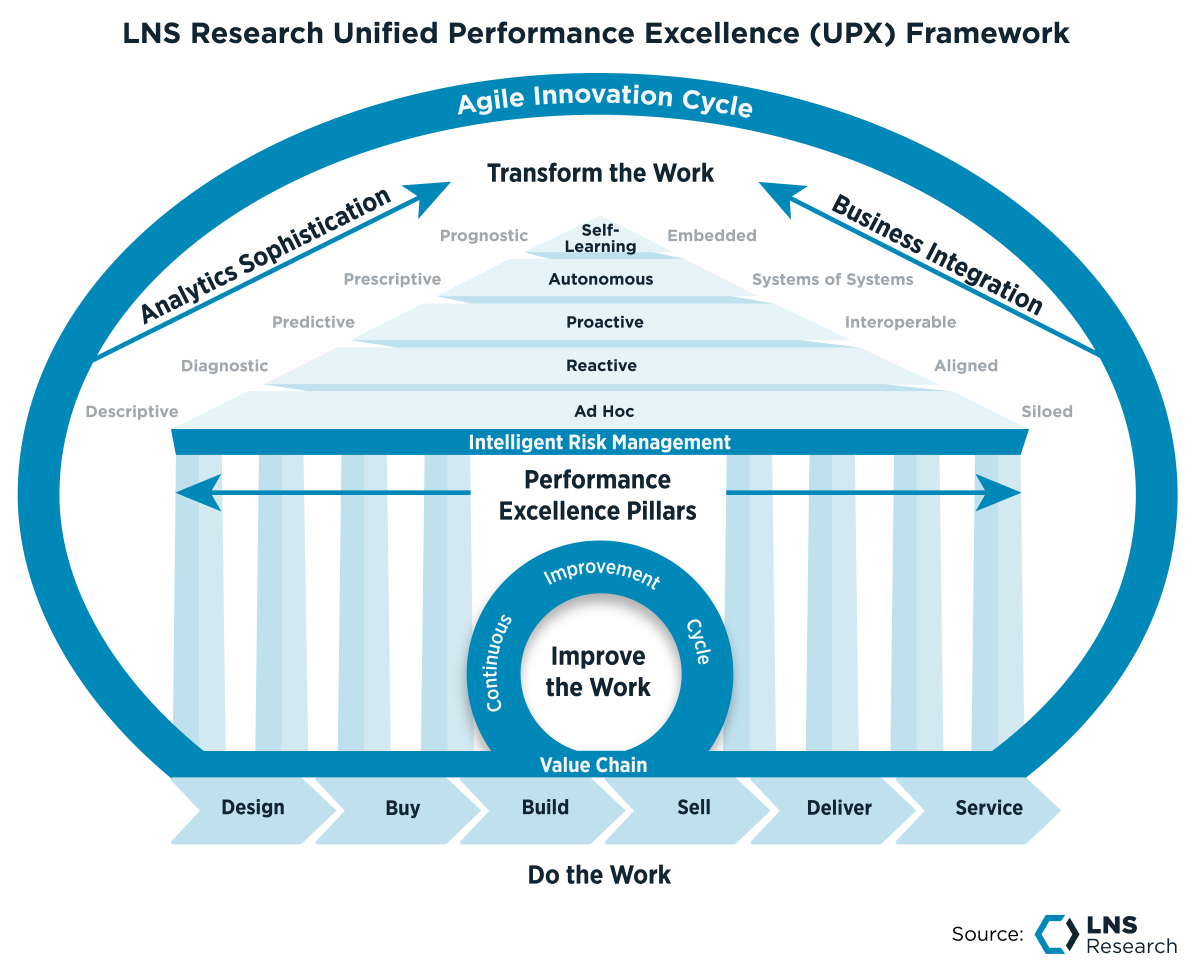
UPX integrates Intelligent Risk Management into the prioritization activity across pillars of risks to operational sustainment to give the Head of Operations an organization-wide view of threats. This allows proactive decision-making about actions to improve the work and transform the work of service, making operations threat-resistant.
There are six best practice clusters from our UPX research that deliver value. The most important of those clusters for transitioning the traditional, manual continuous improvement toolset and management approach to the digital environment are:
-
-
-
Build on what you have, and scale with what you need.
This cluster of best practices reflects the reality that today's preferred approach is a “build on what you have” mentality. The predominant platform used to digitize Performance Excellence methods and toolkits is an Enterprise Quality Management Software (EQMS). Leveraging existing applications early makes sense for digitizing and refining the approach and toolset, but this approach will run out of runway before scaling the program.
The proper “home” for UPX is a fit-for-purpose application set based on a Low Code/No Code environment with embedded or interoperable capabilities for:
• Digital Twins
• Data Connectivity
• Advanced Industrial Analytics
• AI/ML
• Interoperability with Connected Frontline Workforce (CFW) applications
-
Extend Intelligent Risk Management into UPX and build it into the Operational Architecture.
Heads of Global Manufacturing Operations face many challenges hourly, daily, and weekly.
It is very easy to get lost in the crisis of the moment from:
• Daily labor challenges
• Changing customer preferences
• Rapid product configuration changes
• Random supplier shortages
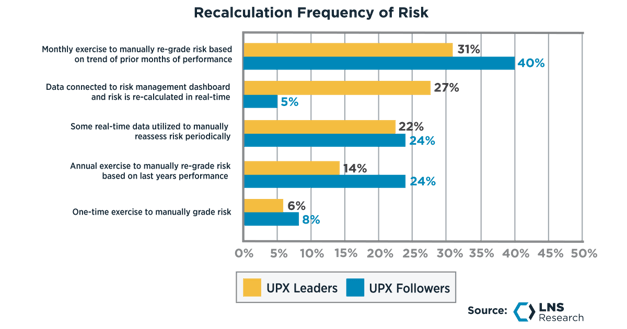
To stay ahead of threats that might shut down manufacturing operations, follow the lead of EHS professionals and build an Intelligent Risk Management framework, but focus it on threats to your manufacturing agility, flexibility, and resiliency.
• Invest in a comprehensive risk framework centered on operational agility, flexibility, & resiliency.
• Digitize and connect the risk framework to data sources. (Figure 3)
• Apply AI and ML to aid the monitoring of changing risk vectors. (Figure 4)
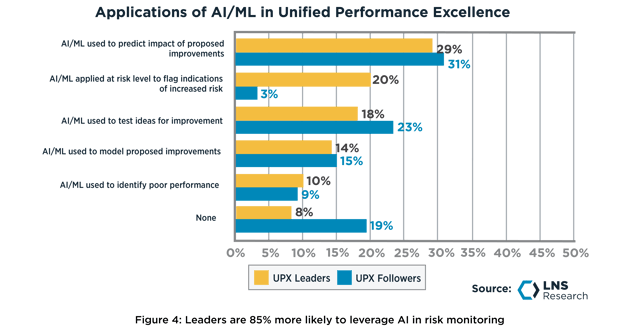
-
Start small, and aim high.
Our previous research on Industrial Transformation (IX) Readiness revealed an insight that comes into play here, the Center of Excellence (CoE). A Center of Excellence differs from a lighthouse in that it represents the plant network rather than an outlier where results would be difficult to translate across the plant network from pilots. A similar concept applies to UPX but in the opposite direction.
To begin to pilot and refine the approach for digitizing Performance Excellence, start with a digitally mature plant, with IIoT sensors covering most aspects of the operation and interoperability with an Advanced Industrial Analytics package.
The second aspect to consider when selecting a CoE is the stability of the existing Continuous Improvement toolkit and management system approach. Don’t try to digitize in a plant where the team still struggles with the Continuous Improvement culture. Trying to change culture AND digitize the process and tools simultaneously is a recipe for failure.
Summary
Unified Performance Excellence embeds the preferred method and toolset into the IX Architecture and leverages advanced digital tools such as Analytics, AI/ML, and Digital Twins to improve speed to impacts, lower the special knowledge requirement, harden the process to turnover of trained practitioners, and deliver a comprehensive view of threats to operational agility, flexibility, and resiliency.
Recommendations for Manufacturing Leaders:
Head of Operations:
-
-
-
Appoint someone senior from your team to focus on strategy. With so much happening daily, it is easy to slip into crisis-management mode. Heads of Operations need a “right-hand” person dedicated to focusing on strategy, Industrial Transformation, and coordinating & consolidating teams across the manufacturing footprint.
-
Build your risk frameworks for threat vectors. Thoroughly evaluate potential risks, starting with familiar risks that have happened or are likely to happen, to build out a risk framework relevant to the business.
-
Digitize risk frameworks, then connect them to real-time data. Leaders are 82% more likely to monitor threats to agility, flexibility & resiliency in near-real-time.
-
Apply Advanced Industrial Analytics and AI/ML to monitor and flag changes in risk.
Head of Quality/Performance Excellence:
-
-
-
Digitize the Continuous Improvement process within an existing “Island” platform, such as your EQMS. Even though EQMS is not the proper end place for UPX, much can be learned and refined in an EQMS or EHS solution before transitioning to an interoperable platform.
Recommendations for Vendors
-
-
-
For those firmly in the Analytics space, prepare for utilization of your platform for end users to “build their own” custom risk frameworks on top of your platform.
-
There are two use cases for Analytics in support of UPX, the first is the Intelligent Risk Management layer, and the second is at the operational layer to deliver insights at speed about:
-
For those with strength in the Low Code/No Code “Citizen Developer” enablement space, evaluate your interoperability situation and if not present, expand interoperability with Analytics, AI/ML, and Digital Twin product offerings to enable the end-user to build their own closed-loop approach between executing on Continuous Improvement projects, and managing risks.