Excellence in operational execution is hard to maintain and grow and is getting more challenging by the day in this era of post-pandemic-related societal upheaval, geopolitical tensions, economic uncertainty, supply chain fluctuations, and environmental concerns.
In an Industry 3.0 world, building a sustainable program for improvement experienced several barriers to entry.
Continuous Improvement Management Systems from the Industry 3.0 era heavily emphasize policies, procedures, and people.
-
-
-
People learn the skills and techniques needed
-
People execute the projects
-
People define the policies
-
People identifying opportunities
-
People determine the actions to take
-
People drive the culture change
-
People make the program go or falter
Figure 1: Embedded Unified Performance Excellence is the goal
Continuous Improvement toolkits and management systems, no matter what the flavor, require significant investment in:
-
-
-
People skill development
-
Patience for long-awaited results
-
Occasional project failure
-
Rapidly changing priorities
Additionally, in traditional Continuous Improvement toolkits and management systems, as time goes on, returns start to diminish. It is challenging to maintain focus over several years of effort (Figure 1).
Unified Performance Excellence (UPX), shown in Figure 2 below, leverages digital tools and technology to build a “Risk Control Tower” view of operational agility, flexibility, and resiliency. An Industrial Transformation (IX) embedded Performance Excellence program leverages digital tools, such as;
-
-
-
Low code/no code workflow
-
Robotic Process Automation (RPA)
-
Digital Twins
-
Machine Learning Models
-
Artificial Intelligence (AI)
-
Virtual reality
-
Digital processes
-
Advanced Industrial Analytics
-
Connected Frontline Workforce (CFW) applications
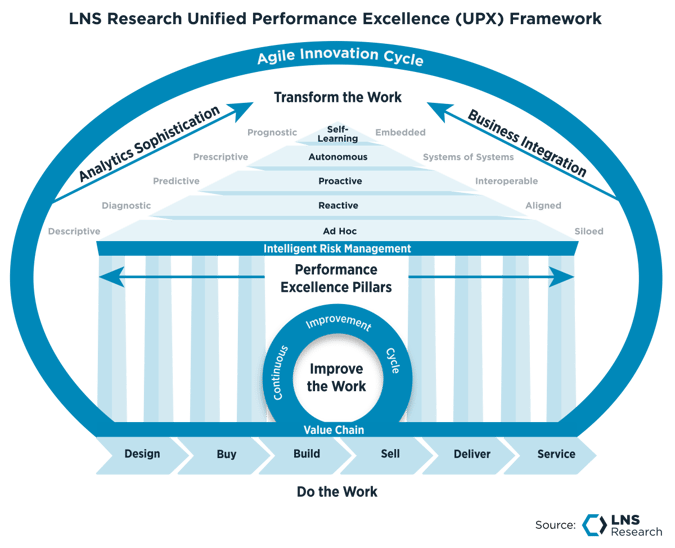
Figure 2: Embedded Unified Performance Excellence (UPX)
Leveraging these technologies standardizes and embeds aspects of the program around near-real-time operational risk management. Giving the Operations Leader a view of risk that makes shifting priorities and discerning significant transformation opportunities easy to see.
These same digital tools and environments allow for standardized process execution (Kaizens, DMAIC projects, Agile Scrums, etc.), ensuring people can follow a structured program to achieve improvement within the digital environment.
Digitization of the execution process significantly lowers the learning curve barrier to entry.
Turbocharge execution processes by leveraging advanced digital technologies, such as:
Empowering insights delivered to problem-solving at digital speed. Interconnectivity with a Connected Frontline Workforce delivers insights to the shop floor, where the improvement happens.
A New Way Forward
This situation reveals a new way to think about Performance Excellence and new ways to use UPX as the improvement engine WITHIN the Industrial Transformation (IX) Environment.
The conventional wisdom regarding transformation has been to optimize manual processes outside of the digital environment BEFORE digitizing and automating them. With the growing adoption of UPX, which leverages advanced digital tools, a new approach to conventional wisdom can be achieved.
Digitize processes as they are, then use advanced digital tools, like Digital Twins and AI, to improve the processes inside the digital environment before automating them. (Figure 3)
Figure 3: The Rise of the Digital Twin
Summary
Performance Excellence has long been a manual set of activities. Leaders are exploring the digital environment and finding significant value in digitizing the process. LNS Research recommends leveraging advanced digital tools to deliver the value of UPX as the improvement engine for transformation while at the same time integrating an Intelligent Risk Management approach focused on operational agility, flexibility, and resiliency.
Recommendations for Manufacturers
-
-
-
Adapt a low code/no-code workflow environment to digitize the preferred improvement process.
-
Connect advanced digital tools like Twins, AI/ML, and Analytics to the UPX environment.
-
Digitize manual processes as they are today, then use Digital Twins and AI to help improve them in the digital environment.
-
Utilize analytics technology to build Intelligent Risk Management (IRM) frameworks for your operational risks.
-
Leverage robust data connectivity to make the IRM dashboard as near-real-time as possible.
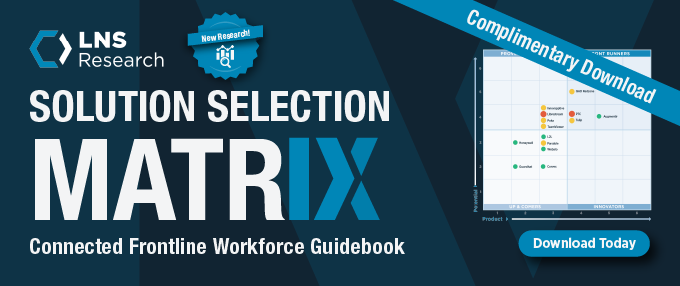