Manufacturers are facing a critical challenge: how to capture and transfer the expertise of experienced workers before it’s lost.
LNS Research data shows that the influx of less experienced employees is already contributing to declines in safety, quality, efficiency, and productivity (Figure 1). To sustain performance, organizations must rethink how they manage and share knowledge—leveraging new strategies and technologies to close the skills gap and empower the workforce.
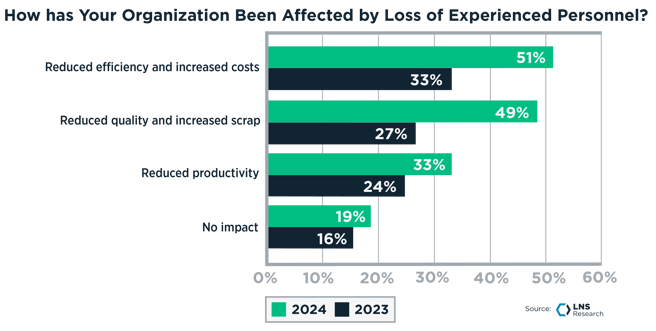
Figure 1: The loss of experienced personnel continues to impact operations significantly
As workforce tenure decreases across the industry, accelerating the competency and capability of newer workers has become a pressing challenge. For manufacturers, the ability to preserve critical institutional knowledge, upskill employees, and adapt quickly is no longer optional—it’s essential.
To future-proof operations and sustain long-term performance improvements, manufacturers must move beyond reliance on experienced employees and adopt a holistic approach to transfer accumulated knowledge to new workers rapidly. While generative AI and emerging technologies are powerful enablers, they alone cannot address the complexities of industrial knowledge management.
Defining Industrial Knowledge Management
LNS Research defines Industrial Knowledge Management as the processes and technologies used to generate, capture, evaluate, organize, transfer, and (re)use information and knowledge across the organization to support safe, sustainable operations.
The LNS Research Industrial Knowledge Management Framework (Figure 2) provides a scalable approach to leveraging digital technologies that address workforce gaps, optimize onboarding, and enable agile, data-driven decision-making:
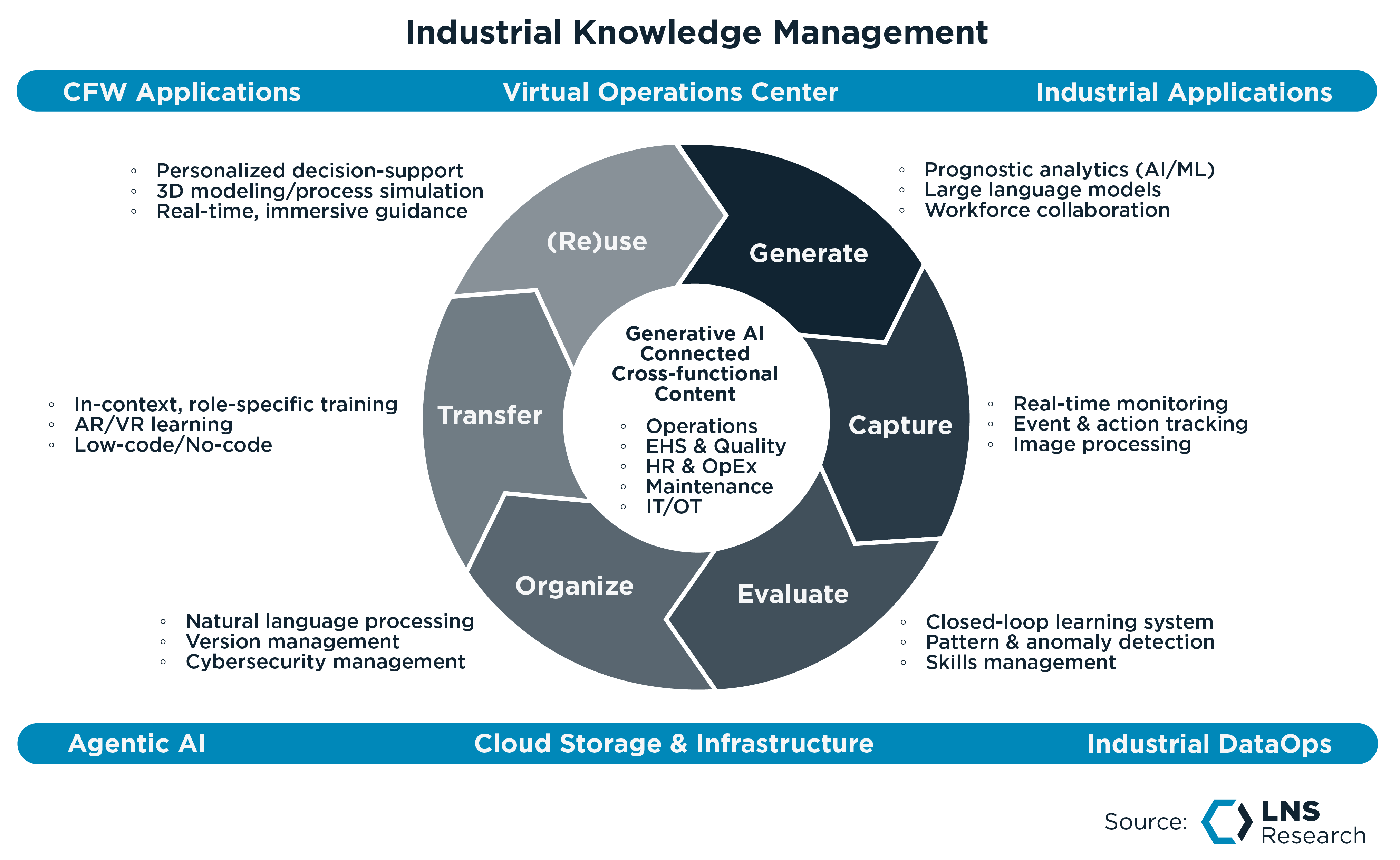
Figure 2: Applying newer techniques and technology
across the entire knowledge lifecycle is critical for survival
-
-
-
Foundational technologies such as cloud storage, infrastructure, and Industrial DataOps, layered with Agentic AI, create a secure and scalable foundation necessary to support enterprise-wide knowledge ecosystems.
-
Integrated processes dynamically manage knowledge by leveraging emerging technologies throughout the entire knowledge lifecycle to seamlessly connect employees to accurate, relevant, and context-aware knowledge and insights.
-
Generative AI is a transformative technology that automates manual processes, drives deeper cross-functional collaboration, and empowers employees to create, validate, and share actionable knowledge at scale.
Adopting a holistic Industrial Knowledge Management is critical as industries face the dual challenges of preserving institutional knowledge and building workforce competency amid growing demands for modern, digital tools across industrial operations. To future-proof operations and achieve business objectives, organizations must retool knowledge management strategies to empower the workforce with solutions that foster collaboration and support better, faster decisions.
Retooling Industrial Knowledge Management
Industrial transformation Leaders, those manufacturers leveraging digital technologies and achieving step-change improvements across industrial operations, are retooling industrial knowledge management with newer techniques and technology to unlock new levels of safety, efficiency, and productivity. The Industrial Knowledge Management Framework illustrates the technologies and approaches Leaders have adopted to support business outcomes.
LNS Research identified three key areas Leaders are investing in to streamline the knowledge lifecycle, eliminate inefficiencies, and empower their workforce:
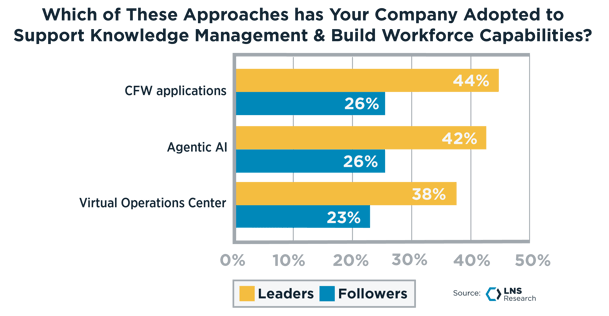
Figure 3: Leaders invest in Agentic AI, CFW applications, and Virtual
Operations Centers to enable seamless knowledge management
-
Agentic AI
Agentic AI is revolutionizing how manufacturers manage the knowledge lifecycle. These technologies automate processes, deliver actionable insights, and enhance decision-making by:
-
-
-
Creating role-specific work instructions and training materials.
-
Providing predictive and prescriptive insights to optimize task execution.
-
Contextualizing, organizing, and updating knowledge assets to ensure dynamic reusability.
-
Accelerating competency with in-context training and adaptive learning paths for employees.
Leaders have integrated Generative AI tools, such as Large Language Models (LLMs), across Industrial Applications and platforms to improve findability and minimize the need for version control. However, these tools alone are not enough to address the full complexity of knowledge management.
-
Connected Frontline Workforce (CFW) Applications
CFW Applications are transforming how manufacturers empower leaders, frontline employees, and cross-functional support teams. These applications streamline tasks, improve decision-making, and enhance collaboration by:
-
-
-
Providing real-time monitoring and actionable insights to reduce risks proactively.
-
Ensuring employees have the most up-to-date task-specific guidance at the point of work.
-
Enhancing safety with context-aware tools that provide personalized decision support.
-
Enables real-time visibility and collaboration platforms to enhance operational performance.
Leaders have scaled CFW application capabilities across the enterprise to enable the entire workforce with digital tools that automate the knowledge lifecycle and foster a knowledge-sharing culture.
-
Virtual Operations Centers
Virtual Operations Centers allow organizations to digitally connect employees at every level to a network of knowledge, expertise, and resources across the enterprise. This approach standardizes processes, optimizes resources, and enhances decision intelligence by:
-
-
-
Ensuring workers have the most accurate processes, techniques, and technology for tasks.
-
Enabling seamless IT/OT integration using Industrial DataOps frameworks to dismantle silos. Building secure, scalable solutions and technologies beyond standalone AI or cloud offerings.
-
Embedding a data-driven culture that aligns teams across operations, HR, and IT.
Leaders are creating Virtual Operations Centers that connect people, data, and processes with innovative, adaptable tools that streamline the flow of knowledge across the entire operations network.
Building Knowledge Ecosystems for the Future of Industrial Work
Leaders are achieving significant improvements in safety, efficiency, and workforce productivity (Figure 4) by adopting emerging knowledge management solutions that address skills gaps, streamline processes, and enhance collaboration. Manufacturers need more than just AI to unlock knowledge management's full potential; the Industrial Knowledge Management Framework provides a comprehensive blueprint for building a resilient, future-ready knowledge ecosystem.
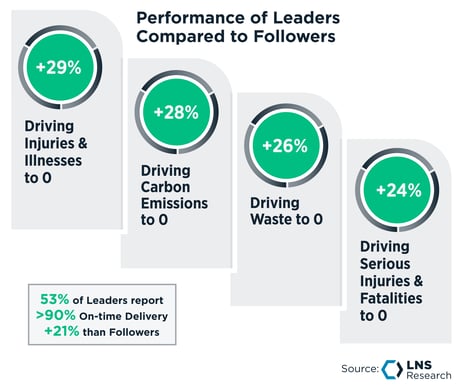
Figure 4: Leaders outperform Followers across key business and sustainability metrics
Chief Operations Officers must lead the charge by embracing knowledge management as a foundational enabler. Transformation requires bold organizational changes, strong partnerships with HR and IT, and a defined investment strategy. To leverage the framework’s principles, COOs should:
-
-
-
Elevate Operations Leadership: Appoint dedicated leaders focused on workforce development and knowledge enablement.
-
Redesign Roles and Responsibilities: Establish cross-functional roles and teams that align priorities across operations, HR, and IT, ensuring the seamless integration of knowledge management processes.
-
Develop Workforce Centers of Excellence: Create inclusive teams to drive innovation in knowledge preservation, safety, and productivity while scaling solutions across the value chain.
For actionable insights, strategies, and frameworks, download “The Knowledge Management and Industrial AI Imperative: Bridging the Skills Gap with AI, Connected Workers, and Virtual Operations Centers” for more LNS Research insights.
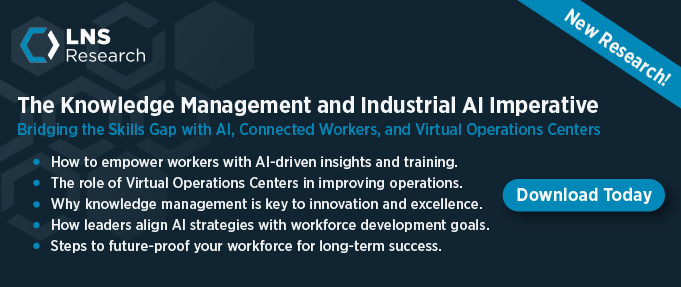