In a recent article by Andy Metzger, State House News Service, titled “Fed Review Faults MBTA for Inadequate Maintenance Plan”, reviewed the results of the Federal Transit Administration (FTA) released their triennial review of the Massachusetts Bay Transportation Authority (MBTA).
Click here to speak with Jason
In the review the FTA stated the MBTA lacked a comprehensive and overall maintenance plant for Heavy and Light Rail Transit. It was also reported that different divisions within the MBTA who were responsible for the maintenance of third rail, signals, facilities and power, and tunnel ventilation are operating “somewhat independently” from one another. Combine this with a $7.3 billion in backlog spending required to bring MBTA assets into a state of good repair create the potential for serious reliability and safety issues for years to come.
This was on full display last year with the Boston, MA area experiencing one of the toughest winter’s on record, resulting in the complete shutdown of some lines for days. Most of the issues resulted in old equipment not being able to handle the large amounts of snow on a weekly basis.
It’s clear the MBTA has its work cut out for it and knowing the scope of the issues are one thing, doing something about it with a sound plan is quite the different animal. So how do they tackle the daunting task of reducing a huge maintenance backlog while keep the transit system running on time, without significantly raising rates to commuters?
Siloed in Maintenance Departments
One of the biggest challenges faced in any organization is eliminating organizational silos. This was a key finding the FTA report affecting the MBTA. Our survey results point to why, 76% of the respondents do not have Enterprise wide solution suites or integrated solutions for Asset Performance Management (APM) activities. If there are no centralized systems and processes in place to plan critical maintenance activities, they will make their own decisions as to what is best, which often creates a very reactive maintenance practice.
How do you currently manage APM systems, processes, and performance (N=204)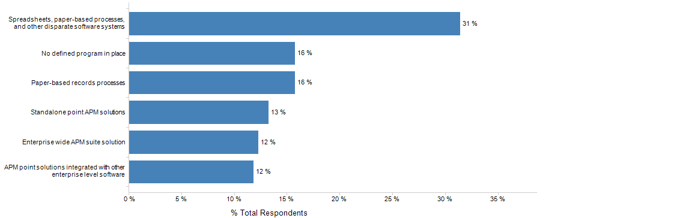
Companies like the MBTA that want to move from reactive to proactive, should first look at the solution landscape they have and see what critical elements they may be missing in order to management all maintenance activities in all departments more efficiently and effectively.
Reducing Backlog Calls for a Balance of Criticality and Risk
Once the solution landscape is understood and solidified, hopefully with no paper and spreadsheet based systems, organizations have their best chance to reduce maintenance backlogs. In the MBTA’s case, it’s a whopping $7.3 billion, sure the amount is daunting, but can certainly be addressed.
A first step is changing the culture and view of maintenance itself from reactive to proactive. There is no way to reduce a backlog by moving from one fire drill to the other. It has been proven many times over that a reactive approach is costly, and the results are large backlogs in maintenance activities that should have been done to reduce unplanned activities in the first place.
Getting a hold on this requires a complete understanding of the asset infrastructure and its relation to everything based on its criticality and risk to other assets and the organization itself. In order for the MBTA to become proactive in its maintenance activities and reduce the backlog, a complete evaluation of its assets based on both risk and criticality will be required. This will provide the insight as to what to tackle when and begin the maintenance planning process in which they are in desperate need.
Many Asset Performance Solutions provide a component of this measure to help with identification. Once coupled with a strong analytics package organizations can gain insight to the health of assets and identification of where to focus their efforts.
For a deeper dive see our recently released APM Solution Selection Guide. This provides in depth understanding of which suppliers serve their industry, geography, and business size. The licensing options each supplier offers as well as types of interfaces and functionality each supplier can deliver.
Find Solutions Now, Bigger Changes Coming
Recent proposed rules in the United State by the Department of Transportation have put public transit organizations on notice. The possible establishment of a National Transit Asset Management system to monitor and manage public transportation assets is a positive step forward to improving safety, increasing reliability and performance of the nation’s infrastructure that serves millions every day.
Other regions of the world face similar regulations, for example in 2013, the European Union completed a project called ACEM Rail. Its primary objective was to focus on track assets to reduce costs, time and resource required for maintenance activities and increase reliability and safety of infrastructure.
For those organizations that opt to wait for the new rules to take shape, we say why, the rule and its intent is something all organizations should be striving for and adhering to already. Otherwise, the assets under your management are already at risk and could be a possible detriment to public safety and asset reliability.
Understand the capabilities of twenty of the leading vendors in the APM space by downloading our APM Solutions Section Guide. The guide contains comparison charts for the factors listed above and the detailed profiles of the twenty vendors ranging from automation companies, to enterprise software providers and includes many specialized APM solutions as well.