AspenTech recently announced the new release of Aspen Unified™ to deliver what they call, “the next generation of production optimization solutions that will transform business processes for the world’s refineries. The Aspen Unified solution brings planning and scheduling together in one environment to connect and automate isolated processes, maximize the yield of high-value products, push closer to limits, and drive improved margins.” The Aspen Unified™ solution includes Aspen Unified PIMS™, with Multisite option Aspen Unified Scheduling™, Aspen Unified GDOT Builder™, and Aspen GDOT™.
Inside Unified
AspenTech defines the Self-Optimizing Plant as a facility that can automatically respond to changing operating conditions. With Aspen Unified™, they have integrated planning and scheduling with advanced control and optimization, thereby tightening the integration
between single and multi-site plans, scheduling, and unit optimization. With a single drag’n drop flowsheeting environment now serving both planners and schedulers, along with along with improved plan analysis to improve business results, and automated schedule optimization to save time generating the first-pass feasible schedule, Aspen Unified™ really delivers for planners and schedulers. Future releases will embed AI/ML to automate plan backcasting and schedule feasibility. The payoff in time savings and ease of use in the effort it takes to get to the optimum plan and feasible schedule is significant. So, no more working until midnight wrestling with spreadsheets to get a feasible plan and schedule ready for the 6 am shift.
The second highlight is the integration of GDOT’s dynamic optimization technology, which now directly connects the levers of coordination, optimization, and constraint pushing to better drive the plant and its units to deliver to the plan and schedule. Aspen GDOT constantly reconciles and adapts operations in real-time to changing conditions. The flowsheet modeling of GDOT is linked though Aspen Unified™ to the planning and scheduling environment. LNS has to say the integration of the workflows is impressive … well thought out and pretty slick.
AspenTech says that Aspen Unified™ is open so that end users can integrate it with existing systems such as blend control, crude assay databases, laboratory systems, and third-party BI tools.
LNS Research Perspective
LNS Research sees Aspen Unified™ as a major step in the right direction toward the autonomous plant, one of the subjects of LNS’s future research. We have previously discussed how various models (e.g., process and utilities) are coming together to provide a more comprehensive, non-linear representation of the plant functionality, expressed as a set of integrated digital twins. It’s worth noting that AspenTech had already demonstrated a link between Mtell’s predictive maintenance and their scheduling tools.
LNS foresees further consolidation of the various sub-twins in perhaps three to four primary groups which themselves are interconnected and share models, for example:
- Planning, scheduling, and APC/OPT
- Process and utilities with electrical and energy management
- Process and APC/OPT
- Maintenance and inspection with planning and scheduling
- All connected by an integrated Operational Excellence execution system
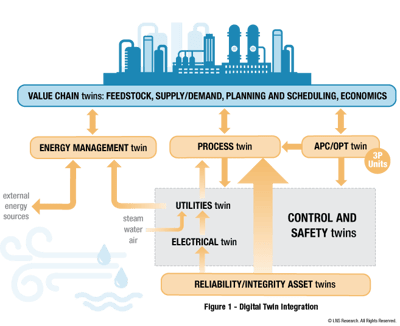
How all of these are ultimately arranged and come together remains to be seen. AspenTech, for example, is not the only vendor to offer a layered and coordinated advanced control and optimization solution in GDOT. But how they do it, where they leverage AI/ML, and now with planning and scheduling integration, sets them apart from the field.
Looking Ahead
AspenTech says Aspen Unified™ is the first step in realizing the vision for the Self-Optimizing Plant. LNS agrees. But there is much more work to be done, and so we look forward to the further elaboration of AspenTech’s vision.
The best news is for planners and schedulers. No more squinting at endless rows and columns! It’s high time for an upgrade. So speak up!
.png?width=2834&name=ATM%20CTA%20TEMPLATE%20(003).png)