Today, the days of simply managing quality through the ISO 9001 requirements are well behind us. Over the past few decades, a number of other ISO management systems have emerged to help companies improve business performance. Many organizations, because of the systems' proven success, have adopted multiple ISO frameworks and heavily rely on the Plan, Do, Check, Act methodology.
Often, there are now five or more families of ISO standards that a company may want to incorporate into its operations, including ISO 9000, ISO 50001, ISO 14000, and others. While having numerous standards in place helps to create an environment of continuous improvement, it also presents a set of challenges. Namely, if not implemented under one common system, it may result in disparity between business processes.
At LNS Research, we advocate for executives to consider every decision with respect to their company's operational excellence model. In this blog post, we'll discuss the most prevalent ISO standards employed in the industrial setting today and touch on how they can be built into operational excellence.
ISO Standards for Industrial Companies
In last week's post, we discussed how changes in production levels caused by growth should be accompanied by changes in quality management strategy. For the example used, adopting the ISO 9001 requirements was a critical next step for an organization that was experiencing difficulties with juggling high volume and quality control. The company plans to implement an Enterprise Quality Management Software (EQMS) as its needs continue to grow.
Although each company will have a unique scenario, leveraging an ISO system can be a tactical move to better manage operations. This can be particularly helpful during a period of rapid growth where homegrown and manual processes are becoming obsolete. Some of the ISO standards you should know are listed in the table below. It's broken down by functional area, listing the associated role, management system, and IT applications.
Understanding Mulitple ISO Standards
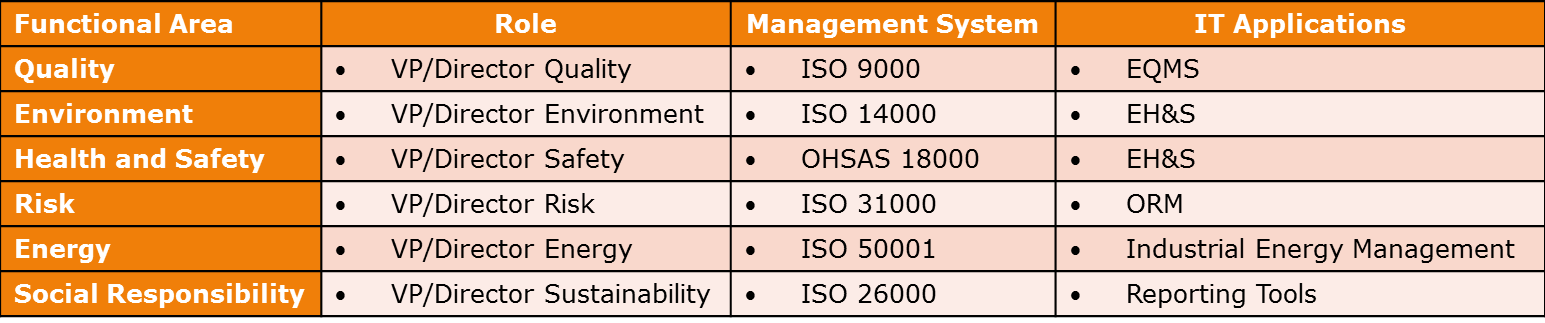
To help clarify the above table, it can be understood by saying, for example, that for the functional area of energy, it's the Vice President or Director of Energy that drives and uses the ISO 26000 family of standards to manage his or her organization. It also shows that implementing Industrial Energy Management Software will facilitate the management of ISO 26000. The same story can be told for other functional areas.
Building ISO Standards into Operational Excellence
LNS Research's operational excellence model advises companies to align strategic objectives with the right mix of people, processes, and technology. The various ISO standards listed above influence and ameliorate operations in numerous ways across the value chain. In addition to having their own sets of regulations, requirements, best practices, and processes, they're each overseen by different departments and senior managers. Also, they each use different IT mechanisms for monitoring and reporting on performance.
With information coming from a multitude of channels, it's easy to get overwhelmed by the sea of data. As a consequence, without a common information strategy, many organizations have little cross-functional communication and collaboration. In such a scenario, improvements will likely be siloed, rather than global, causing companies to miss out on the true benefits of the various ISO management systems.
Integrating ISO standards with the operational excellence definition takes a collaborative approach. After identifying strategic objectives, organizations should establish a plan for people, processes, and technology that is both local to a functional area, but also accounts for the operation as a whole. Making plans for a specific department without a global perspective lacks the long-term vision for operational excellence that companies strive to obtain.
In the case of quality management, a functional area that plays a part in many areas across the value chain, the VP of quality should be leveraging the ISO 9001 requirements and EQMS where applicable, but he or she should also work with cross-functional and cross-departmental teams to understand where systems may overlap with one another. That executive should be working with multi-disciplinary teams to determine potential areas of collaboration to drive long-term business improvements.
For more information on EQMS, read LNS Research's EQMS Solution Selection Guide. The guide covers 18 top vendors in the quality management software market, providing extensive analyses of functionalities, industries served, technology architectures, and more.
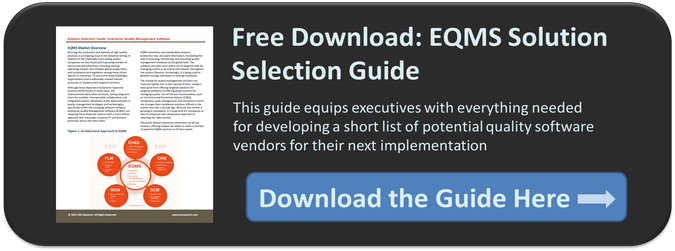
You might also be interested in:
EQMS: Understanding the Drivers behind Global Adoption
Top Integration Points for Enterprise Quality Management
Enterprise Sustainability Management: A Global Approach
