In 2014, 21% of companies reported having an Enterprise Quality Management Software (EQMS) deployment, and an additional 40% reported being in the planning stages of one. Clearly, the significance of EQMS as an enterprise quality hub is becoming greater and greater by the year. In order to justify budget for such an investment, a watertight business case is a prerequisite. This will include typical tangible benefits, but it’s also important to keep in mind the intangibles.
Most executive sponsors of EQMS can effectively describe the process improvements that EQMS will create as well as many of the intangibles, but mainly from a quality perspective. For instance, they know how it will improve the director of quality’s visibility into open corrective or preventive actions (CAPAs), the audit schedule, and ensuring the right quality documents are being used. Where many quality executives fall down, however, is in translating intangible benefits the quality department will experience into either benefits for engineering, manufacturing, the supply chain, or finance. There's often a disconnect between the story of a quality culture transformation, which these other functional groups would support, and how EQMS can support this transformation.
The challenge here of course is assigning a value, and therefore some tangibility of said benefits. Recently, we discussed elements of leadership and employee engagement to drive Operational Excellence, and in this post we'll briefly discuss some of the non-financial benefits implementation of an EQMS delivers.
Understanding Intangible Benefits
An intangible benefit is typically one that is not measured in financial terms and at best is estimated or alluded to in the ROI. It’s something that usually appears woven into case studies post implementation. The intangibles we’re talking about relate specifically to the people and cultural benefits of a technology implementation. Used effectively, technology such as EQMS can facilitate the transformation of fully informed teams into fully informed and engaged ones.
Informed and engaged teams are dramatically better for morale, collaboration and cooperation, and business all around. This is where you start to see the intangibles. Below, we’ll discuss three specific intangible benefits more in depth.
1. Accountability, Transparency & Recognition
Quality management professionals are typically the gatekeepers of actions and other task-driven elements of the QMS, whether in a "closed-loop system" or not, and whether CAPAs are completed on time and are considered effective or not often falls to the gatekeeper. The effort and commitment is made in good faith by the owner of an action, perhaps a result of an internal audit, unplanned event, or investigation.
The fact is, without an EQMS in place the gatekeeper often becomes the "nanny" who assumes a chasing role to get actions closed out on time. The inverse of this is that there are always those top performers who consistently perform QMS-related tasks in a timely and diligent manner but are not recognized. An EQMS reduces and even eradicates the need for the chasing role and due to the transparent and automated nature of the process drives timely close-out.
With this emotion gone, the evidence of those who consistently perform remains, making recognition evident and fact-based. Delinquency is not something any member of a workforce wants to be openly associated with and certainly not in an escalation notification or report that is easily obtained and circulated to executives.
2. Facts (Not Blame)
Blame is a strong and emotionally-charged word. Legendary football coach Lou Holtz said “Never blame the performer, only the performance.” In the case of quality management we are substituting performance for process. By virtue of managing deviations in a structured way, conducting and recording investigations and root cause analysis (RCA) is conducive to objectivity. An EQMS with an automated workflow for this will drive the process collaboratively, and the formally recorded, preserved record will provide the organization with an effective memory of events that are significantly less likely to be based on a blamestorming event but rather on the stated findings and root cause and therefore drives focus to derive appropriate action(s) required to correct or prevent recurrence.
3. Memory and Time (Sentiment)
The entire EQMS serves as the corporate memory of the organization from a Quality Management perspective. The ability to report, search, and interrogate across all the events, deviations, documents, audits, reviews, and regulatory submissions is a distinct and prominent time-saving enabler that a value can be attributed to in an ROI.
Less easily quantified is the value of having everything that came before the "now" available in that manner. It's synonymous with libraries and micro-fische prior to the Internet and search engines. Time is saved in finding artifacts but the value of everything being preserved in one or more seamlessly connected repositories is considered valuable especially when you need it.
Taking this one step further is the notion of ease of access to what came before the "now," the EQMS explicitly determines the format and structure of information common to all, so when expertise is lost or promoted, the successor has a much easier path to navigate as opposed to wading through paper logs, or spreadsheets that may or may not be locked or even flawed. Again, this time can be quantified and a value attributed but the frustration for those charged with keeping the organization moving forward is much reduced. In fact, this can be said of all stakeholders in a well-implemented and easy to use solution–this sentiment is potentially difficult to attain but should be considered "priceless."
Non-Financial Benefits Have Enormous Value
Being able to communicate the softer side of an ROI when discussing EQMS with stakeholders illustrates that the human part of the equation has been taken into account. By expressing the less tangible benefits, we openly demonstrate that the investment being made isn’t a fad or yet another layer of technology. It balances the demand for Operational Excellence and increased competitiveness with improvements in our everyday working experience.
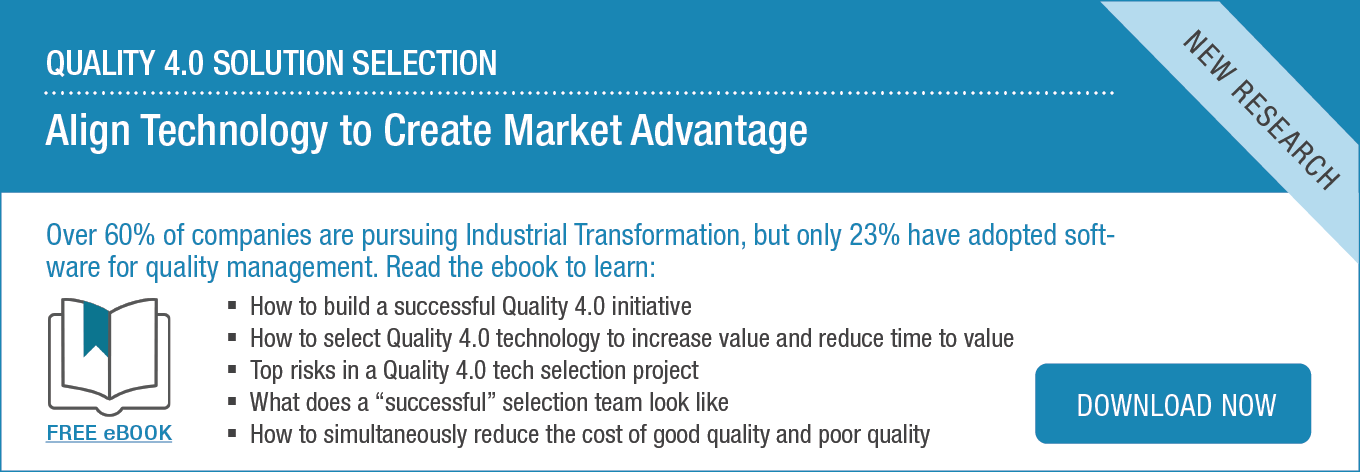